Navigating the intricacies of mechanical engineering and machinery maintenance often leads professionals to the pivotal component known as the oil seal. The term '20 35 7 oil seal' refers to a specific size of this critical part, crucial in the prevention of lubricant leakage and the exclusion of contaminants. While it might seem like a standard component, the distinct measurements of 20mm inner diameter, 35mm outer diameter, and a width of 7mm denote its unique application in various industrial environments.
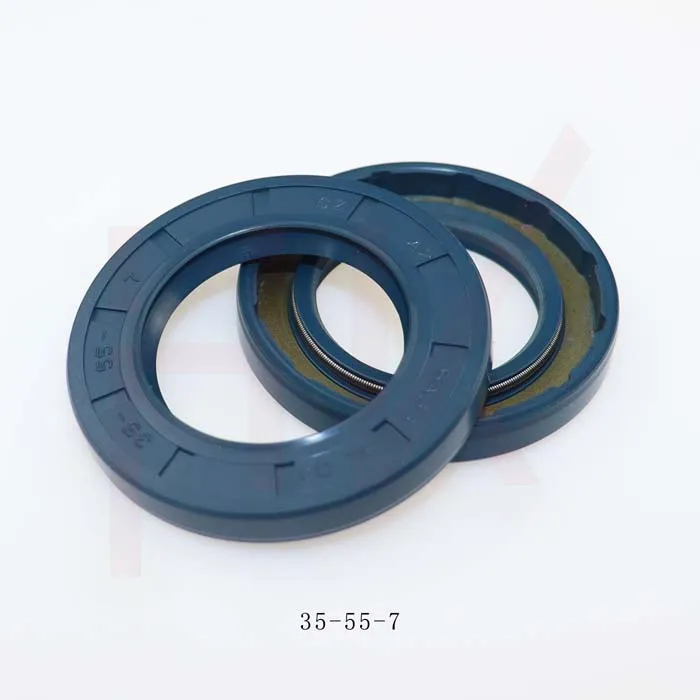
In the realm of experience, the real-world applications of the 20 35 7 oil seal are extensive. Used commonly in automotive and industrial sectors, these seals manage friction between moving parts, ensuring that machines operate smoothly. Mechanics and engineers have reported significant reductions in machinery downtime and maintenance costs when employing the correct oil seal dimensions. For instance, one case involved a manufacturing facility that integrated these seals into their conveyor systems, resulting in enhanced efficiency and prolonged machinery lifespan by minimizing wear and tear.
From an expertise standpoint, the 20 35 7 oil seal's design is a testament to precision engineering. Crafted from advanced materials such as nitrile rubber or Viton, these seals are equipped to withstand a variety of challenging conditions, including high temperatures and hostile chemical environments. The choice of material impacts seal performance; nitrile rubber offers good resistance to petroleum oils, while Viton extends the service life in high-temperature applications up to 204°C (400°F).
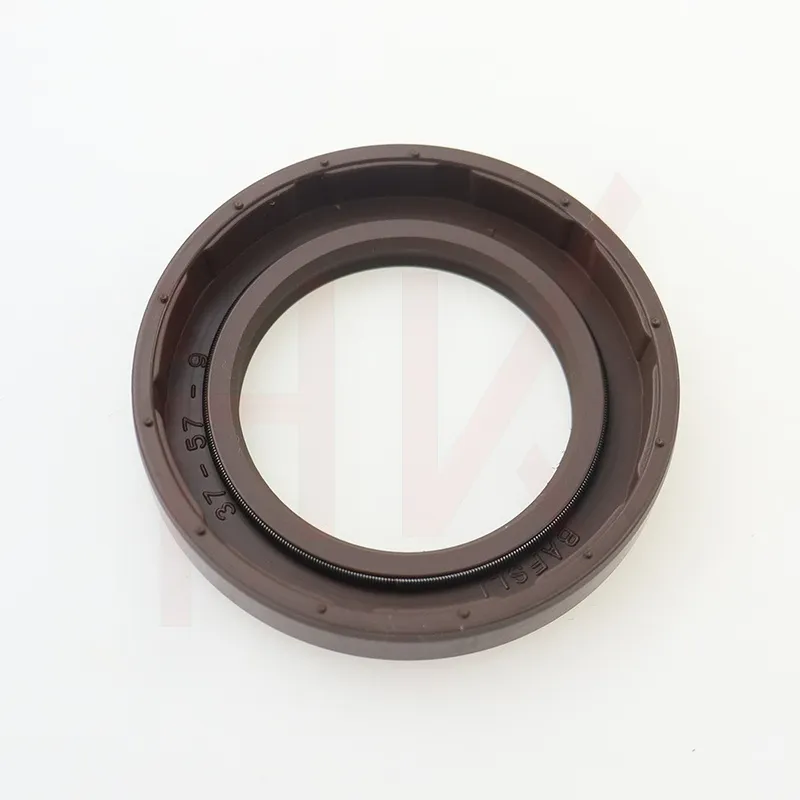
20 35 7 oil seal
In terms of authoritativeness, industry standards highlight the importance of choosing the correct oil seal size and material for specific applications. The 20 35 7 oil seals are manufactured to adhere to global standards, ensuring compatibility and reliability across different machinery and geographic locations. Experts recommend conducting a thorough assessment of the application requirements, including pressure, speed, and temperature, before deciding on the right seal. Industry leaders continuously invest in research and development to enhance the seal’s performance, thereby solidifying the importance of utilizing premium seals for optimal machinery function.
Trustworthiness is paramount when selecting components such as the oil seal. Choosing seals from reputable manufacturers guarantees quality and durability, backed by certifications that attest to their capacity to perform under specified conditions. End-users are encouraged to verify the supplier credentials and seek testimonials or reviews regarding the seal's performance in similar applications. This diligence not only ensures machinery efficiency but also aligns with environmental and safety standards by preventing leakages that could result in environmental hazards or machine failures.
In conclusion, the 20 35 7 oil seal, while a small component, plays a substantial role in the seamless functioning of machinery across various industries. Leveraging insights from real-world experiences, understanding the nuanced expertise behind their design, and trusting in reliable sources are critical steps to maximizing the benefits these seals offer. As machinery continues to evolve, so does the technology and science behind oil seals, cementing their place as indispensable elements in modern engineering solutions.