Hydraulic pump seals are vital components in ensuring the efficient operation and longevity of hydraulic systems. They play a critical role in maintaining system pressure, preventing fluid leaks, and safeguarding the internal components from contamination. These seals are not merely accessories but are fundamental to the performance and reliability of hydraulic machinery used in various industries, including construction, manufacturing, and automotive sectors. This article explores the intricacies of hydraulic pump seals, providing insights into their types, functions, and the expertise required for their optimal use.
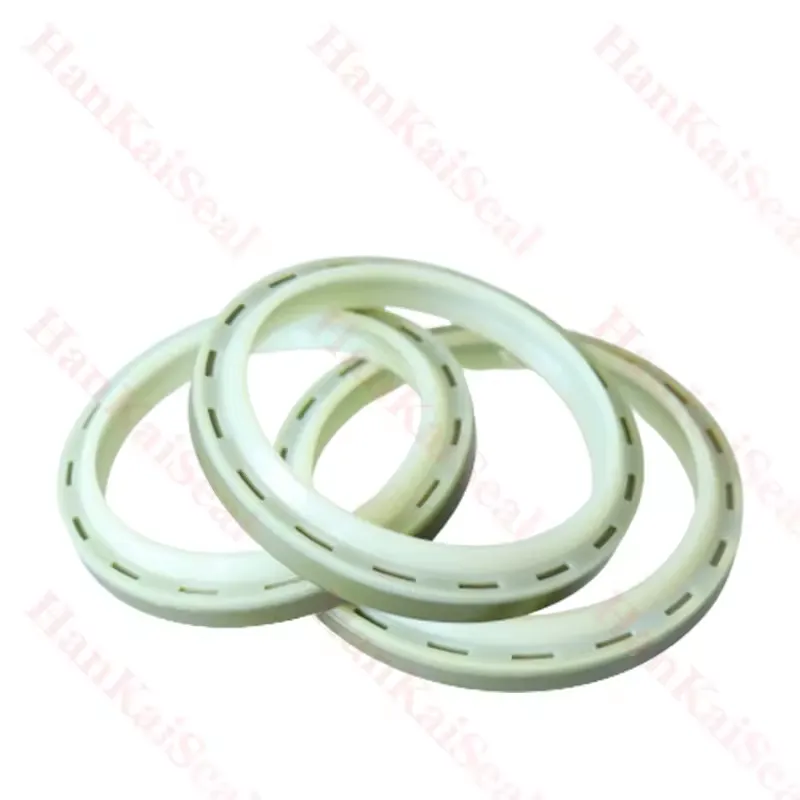
Hydraulic pump seals come in various forms, each designed to meet specific operational requirements. The most common types include rod seals, piston seals, and wiper seals. Rod seals are primarily responsible for sealing the dynamic movement between the piston and the cylinder, thereby preventing fluid from escaping. Piston seals, on the other hand, maintain the seal on the piston's circumference, ensuring that hydraulic fluid does not bypass the piston itself. Wiper seals protect the system by preventing external contaminants from entering the hydraulic cylinder. Each type of seal serves a precise purpose, and understanding the differences is crucial for selecting the right seal based on the application.
An expert’s knowledge encompasses not only the specifications of these seals but also the materials they are made of. Materials such as nitrile rubber, fluoroelastomer (Viton), and polyurethane are commonly used due to their excellent resistance to temperature variations, hydraulic fluids, and mechanical wear. A specialist would evaluate the operation environments to suggest the optimal material, ensuring that the hydraulic system operates with maximum efficiency and minimal downtime.
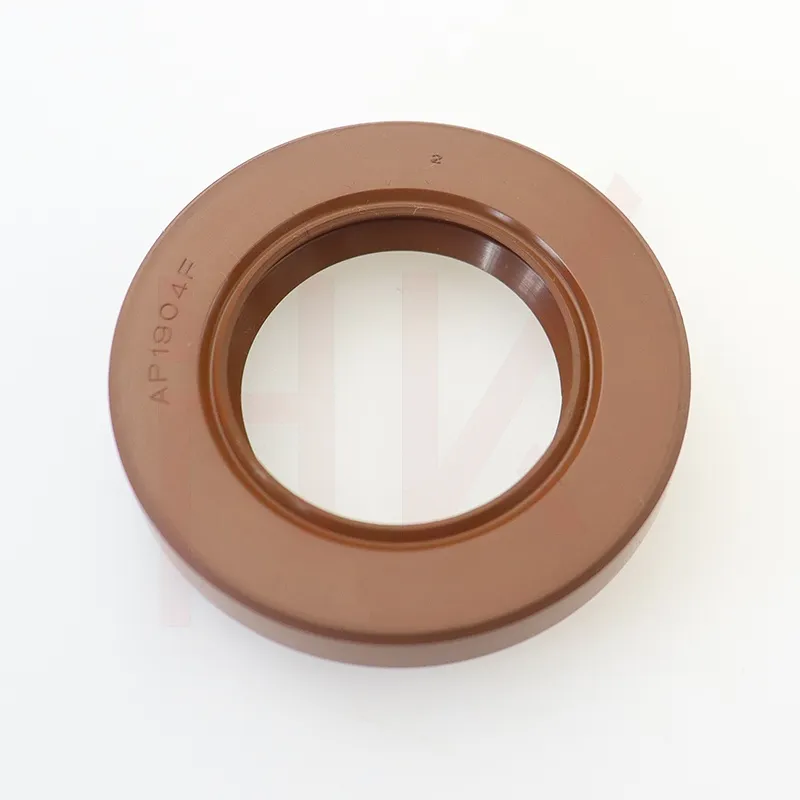
Experience in handling hydraulic pump seals provides a realistic perspective on their maintenance and troubleshooting. Even the highest quality seals can fail prematurely if not properly maintained. Skilled technicians will recommend regular inspections to identify wear and tear early. They are adept at recognizing the symptoms of seal failure, such as fluid leakage, noise, or diminished system performance. This expertise allows for timely interventions, which can save significant costs associated with system breakdowns or extensive repairs.
hydraulic pump seals
Furthermore, understanding the installation best practices contributes to the reliability of hydraulic pump seals. Proper installation requires precision, as improper alignment or forceful fitting can damage the seals or create potential points for leakage. Professionals in the field employ specific tools and techniques to ensure a seamless fitting process, which enhances the seal's effectiveness and extends its service life.
Authoritative voices in the industry stress the importance of quality assurance in the selection of hydraulic pump seals. Choosing products from manufacturers with a reputation for precision engineering and rigorous testing standards ensures that the seals will perform under a wide range of operational conditions. Such assurances are critical in safety-sensitive applications, where seal failure could lead to catastrophic consequences.
Trustworthiness in the context of hydraulic pump seals is achieved through transparent communication and reliable customer support. Manufacturers and distributors who offer detailed product specifications, performance data, and comprehensive warranties build trust with their clients. Trust is further solidified when these businesses provide expert consultations and readily available technical support to address specific challenges encountered by the users.
In summary, hydraulic pump seals are essential to the functionality and reliability of hydraulic systems across various industries. Their performance is heavily dependent on precise specification, material choice, expert installation, and ongoing maintenance. Industry experts wield a wealth of knowledge and experience, ensuring these seals function optimally, thereby safeguarding the integrity of hydraulic machinery. When these best practices are adhered to, businesses can trust in the sustained performance and dependability of their hydraulic systems, ultimately resulting in enhanced operational efficiency and reduced maintenance costs.