In the realm of hydraulic systems, the term 'scraper seal hydraulic' holds paramount importance. These seals, essential components in hydraulic cylinders, prevent contamination and ensure the smooth operation of machinery, offering a unique interaction of functionality and engineering prowess. Below, we'll delve into real-world experiences, expertise insights, authoritative knowledge, and strategies to trust these devices for optimal machine performance.
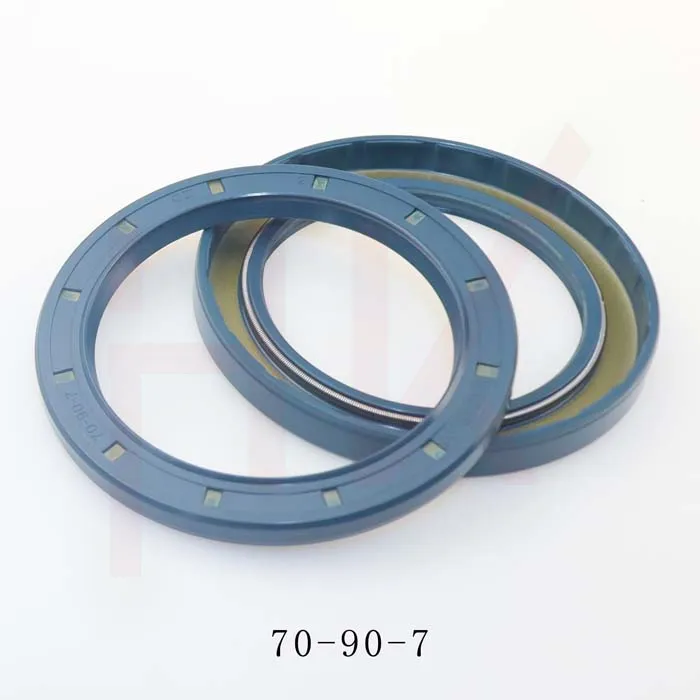
Hydraulic systems are the backbone of countless industries, from construction to automotive manufacturing. At the heart of these systems are hydraulic cylinders, where precision and integrity are crucial. One fundamental component, the scraper seal, serves a vital function by removing dirt and debris from the surfaces of hydraulic pistons as they extend and retract. The absence of a properly functioning scraper seal can be disastrous, leading to contamination within the hydraulic fluid, increased wear on seals, and ultimately, system failure.
Drawing from experience, a seasoned hydraulic engineer recalls an incident in an industrial setting where a malfunctioning scraper seal almost brought production to a standstill. A minute flaw in the seal's construction allowed abrasive particles to bypass the safeguard, resulting in pitted metal surfaces and eventual operational downtime. This costly lesson underscores the necessity of understanding the profound impact of scraper seals on system longevity and reliability.
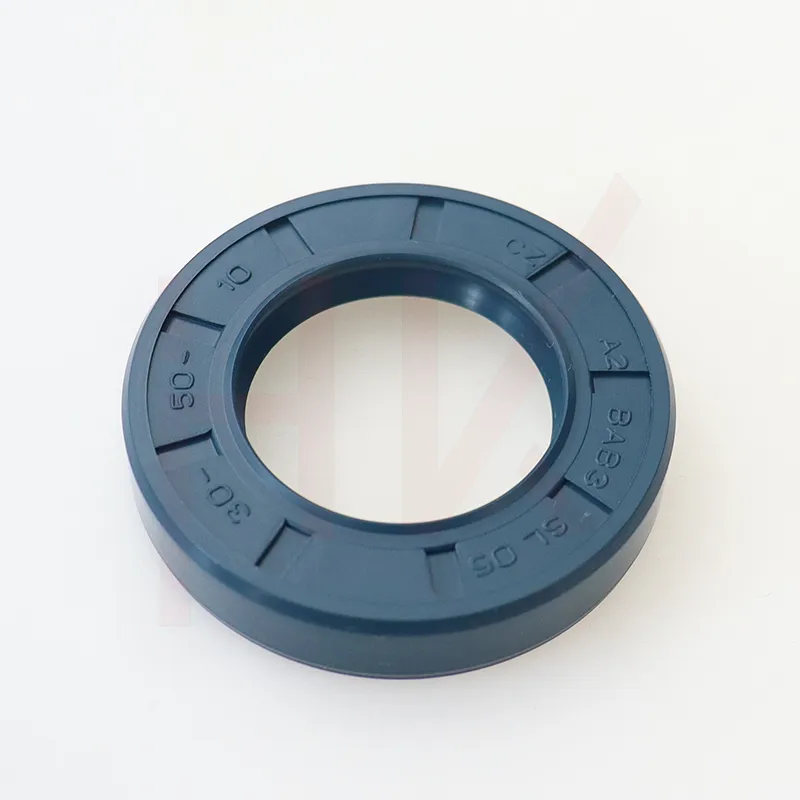
Expertise in the field of hydraulic systems is not merely about theoretical knowledge, but requires a practical understanding of seal materials and configurations. Depending on the operational environment, scraper seals can be crafted from nitrile rubber, polyurethane, or polytetrafluoroethylene (PTFE), each offering distinct advantages. For instance, PTFE is praised for its chemical resistance and low friction, making it suitable for harsh environments. Conversely, polyurethane offers superior abrasion resistance,
ideal for heavy-duty industrial applications. Important also is the seal design single-lip, double-lip, or tandem. Expert selection, guided by an assessment of system requirements, ensures optimal sealing performance and extended service life.
scraper seal hydraulic
Authoritative voices in hydraulic engineering often emphasize standardization and rigorous testing to certify scraper seals. Industry standards, such as ISO 3320 and DIN 3771, provide detailed specifications ensuring uniform quality and performance. Leaders in the manufacturing of hydraulic components adhere strictly to these benchmarks, investing in cutting-edge technology and quality assurance processes to furnish products that operators can unreservedly trust.
Trustworthiness in a product such as the scraper seal is built on several pillars quality assurance, industry compliance, and manufacturer credibility. Reviews and testimonials from industry leaders who have implemented these seals with success can provide insights into their efficacy and performance in practical applications. Reputable manufacturers often offer comprehensive warranties and customer support, reinforcing confidence in their products.
In conclusion, the 'scraper seal hydraulic' is far more than a mere component in a hydraulic system; it is a linchpin to continued productive operations. Understanding the nuances of scraper seal materials and designs, informed by past experiences and expert insights, allows for informed decisions contributing to system efficiency and reliability. Trust is cultivated through a blend of quality craftsmanship, compliance with international standards, and positive endorsements from the field. Investing in high-quality scraper seals is a prudent step toward safeguarding machinery performance, longevity, and ultimately, operational profitability.