Hydraulic lip seals are integral components in various hydraulic systems, serving a critical role in maintaining system integrity by preventing fluid leaks. These seals are designed with a precision fit that allows them to effectively block the passage of fluids while enduring considerable pressure and temperature variations. Understanding the technology behind hydraulic lip seals, their applications, and best practices for maintenance is essential for anyone involved in the planning, engineering, or maintenance of hydraulic equipment.
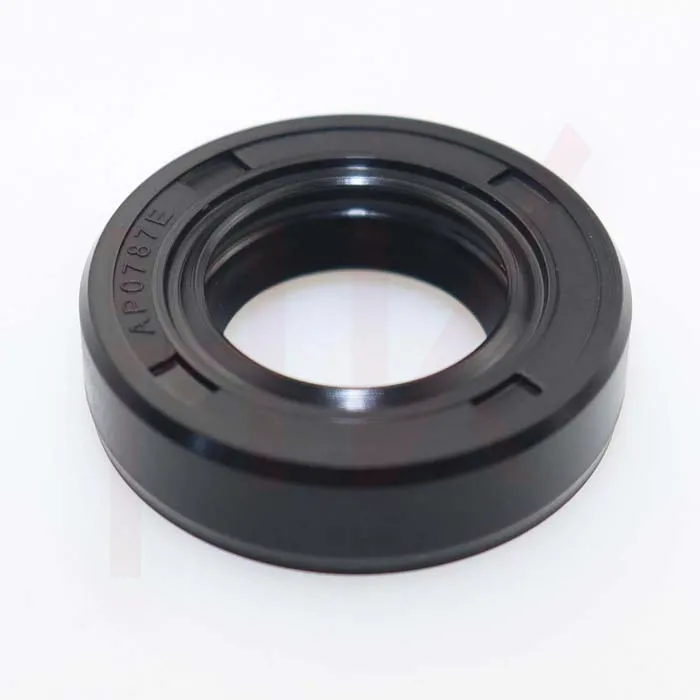
At their core, hydraulic lip seals consist of a flexible lip component that is pressed against a rotating shaft or stationary component. The lip's primary function is to create a barrier against fluid escape, employing a combination of material elasticity and system pressure to enhance its sealing capability. These components are fabricated from advanced materials such as Nitrile Rubber (NBR), Fluorocarbon (FKM), and Polytetrafluoroethylene (PTFE), each chosen for its specific capabilities to withstand particular operational demands like high temperatures, chemical exposure, or abrasion.
In hydraulic systems, lip seals are often employed in cylinders, pumps, motors, and valves—essentially any component where fluid control is vital. The specific choice of lip seal material and design can significantly impact performance, with certain materials offering superior resistance to heat, chemicals, or physical stress, depending on the application.
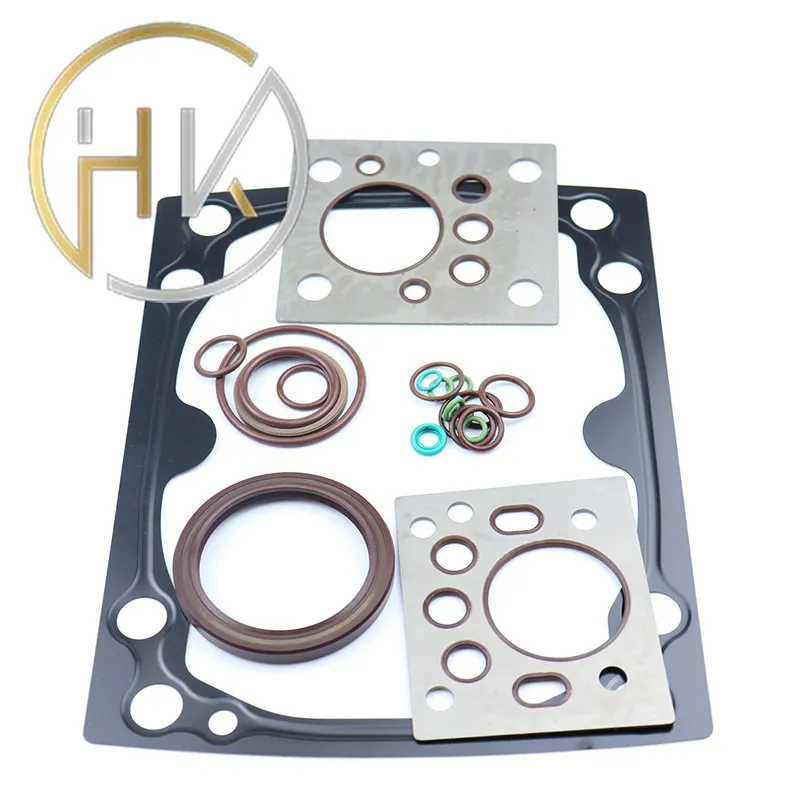
Expertise in selecting the right hydraulic lip seal begins with an understanding of the operational environment. Factors such as pressure,
temperature, fluid type, and the speed of rotation must all be considered. For high-temperature applications, fluorocarbon seals can offer superior performance, while PTFE seals offer excellent chemical resistance, fitting for environments involving aggressive fluids.
The expertise required extends to installation and maintenance, as improper handling can lead to premature seal failure. It's crucial to ensure that the sealing surfaces are clean and free from debris during installation. Furthermore, regular inspection and replacement are recommended to maintain the efficiency and longevity of the seal. A common pitfall is neglecting the importance of shaft surface finish and hardness, which can drastically affect the lifespan and sealing efficiency of the hydraulic lip seal.
hydraulic lip seal
Authoritativeness in the realm of hydraulic lip seals is demonstrated by manufacturers through rigorous testing and quality assurance processes. Products from reputable companies are typically accompanied by comprehensive technical documentation, detailing specifications, installation guidelines, and recommended practices. This documentation is invaluable for technicians and engineers, providing a reference point for ensuring that seals are applied correctly according to specific operational needs.
When assessing the trustworthiness of a hydraulic lip seal supplier, consider their track record within the industry and their commitment to innovation and customer support. Trusted manufacturers will not only provide high-quality products but also support through technical assistance and services such as predictive maintenance solutions to preemptively address potential problems before they lead to operational downtime.
Experience shared by industry professionals also plays a crucial role in understanding the practical applications of hydraulic lip seals. Real-world case studies and user testimonials provide insights into how these components perform in various conditions, equipping engineers with the knowledge needed to optimize system design and maintenance strategies.
In conclusion, hydraulic lip seals are indispensable in managing fluid dynamics within hydraulic systems. Through a comprehensive understanding of material properties, system requirements, and proper maintenance practices, one can optimize the performance and longevity of these components. Engaging with experienced suppliers and utilizing technical resources can further enhance outcomes, ensuring hydraulic systems operate efficiently and reliably in demanding conditions.