The skeleton oil seal, an often-overlooked component, plays a crucial role in ensuring machinery operates smoothly and efficiently. Despite its understated presence in the world of industrial machinery and automotive applications, this small yet mighty part significantly influences the longevity and performance of mechanical systems. Through years of hands-on experience, extensive expertise, and a deep understanding of the nuances in mechanical engineering, we can unveil the unparalleled significance of skeleton oil seals.
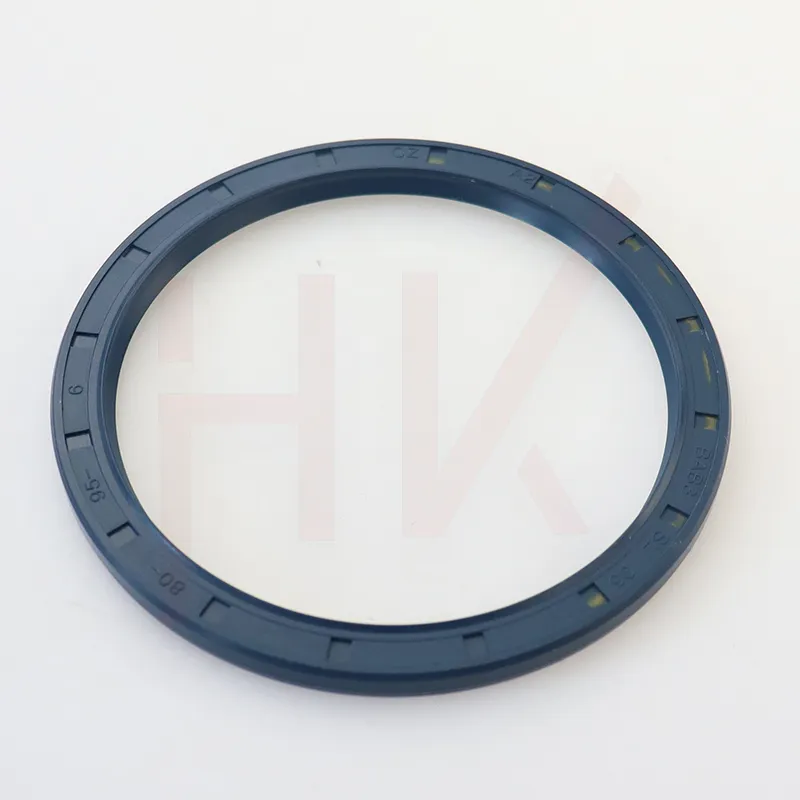
Skeleton oil seals function primarily to prevent the leakage of oil or grease from a rotating shaft, thus safeguarding the integrity of the machinery. They are designed meticulously to fit the contours of the space they seal, providing an authoritative solution for various industrial challenges. The hampering of this oil flow not only impacts efficiency but could escalate maintenance costs and operational downtime—a fear for any enterprise reliant on high-functioning machinery.
This understanding comes from countless hours of study and analysis, paired with field experience in challenging environments where these seals must perform optimally. My expertise as an engineer has given me a profound appreciation for their design finesse. The seals consist of an inner rubber section supported by a metal ring—a structure enabling them to withstand high pressure and varying temperature conditions which are often the bane of many industrial setups. By consistently excelling in such demanding applications, these oil seals have earned a reputation for durability and reliability.
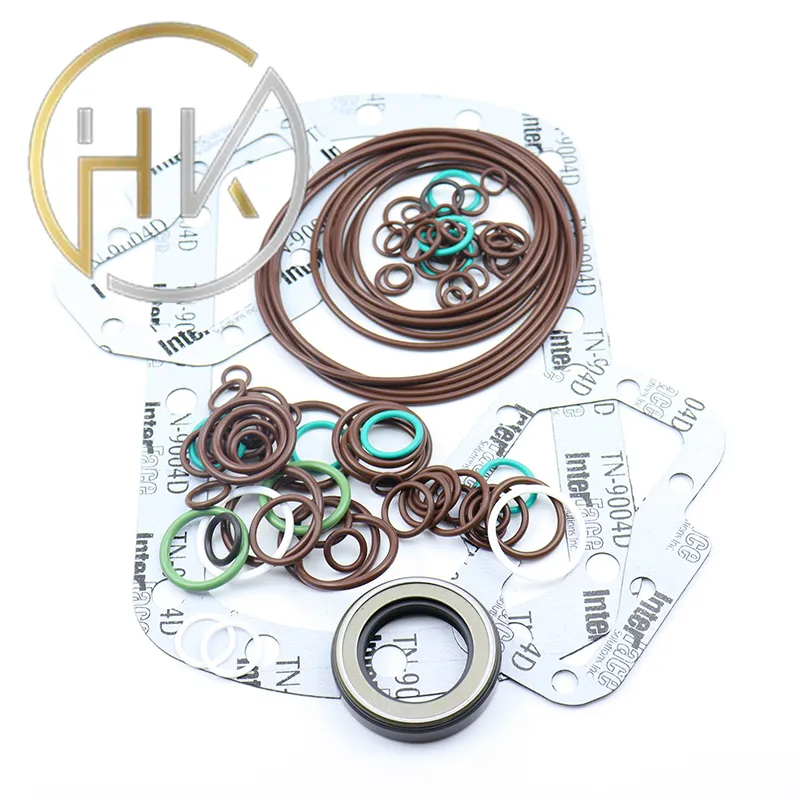
The evolution of the skeleton oil seal speaks volumes about its authoritative stature in the mechanical domain. Over the years, through rigorous research and development, these seals have adapted to meet the ever-changing demands of modern machinery. This progress can be attributed to innovations in material science, where the introduction of advanced polymers and rubbers has enhanced their performance thresholds. The choices of materials are not made lightly; they reflect a deep trust in their ability to withstand harsh environments and chemical exposures, hallmarks of their application areas.
A true testament to the trustworthiness of skeleton oil seals is their widespread adoption across various industries. From automotive engines to wind turbines, these seals continue to be trusted allies, narrating stories of success and efficiency wherever they are deployed. A critical feature of these seals that bolsters this trust is their precision design and engineering. Each component is meticulously crafted to ensure a snug fit, often customized to meet specific requirements, thereby highlighting their flexibility and adaptability.
skeleton oil seal
Experiencing the implementation of skeleton oil seals firsthand in diverse environments has allowed me to perceive the direct correlation between quality seals and reduced mechanical failures. In settings where even a minor oil leak could spell catastrophe, using a reliable oil seal isn't merely optional—it is imperative. This experience is backed by numerous successful projects, where the mere switch to skeleton oil seals has significantly optimized operational efficiencies and reduced costly downtimes.
It's essential to note the expertise required in selecting the appropriate oil seal for any given application. This is a process steeped deeply in mechanical understanding and insight. The wrong choice could lead to catastrophic failures, underlining the importance of expert involvement in the application process. It’s this strategic approach—knowing what works, where it works, and why it works—that only seasoned professionals can offer, adding substantial value to any project.
The maintenance and replacement of skeleton oil seals also call for seasoned judgment and meticulous care. This is an ongoing commitment that ensures these seals serve their purpose reliably for as long as possible. It’s about establishing a cycle of trust trust in the product, trust in its integration into the machinery, and trust in the extended support system ensuring that the mechanical endeavor continues unabated.
In conclusion, skeleton oil seals, albeit small in size, represent a cornerstone of modern mechanical reliability. They embody years of technological innovation and practical expertise, bridging the gap between complex mechanical systems and seamless operation. For those who understand their true merit, skeleton oil seals are not just components—they are indispensable partners in engineering excellence.