The demand for effective sealing solutions is burgeoning across multiple industries, from automotive to industrial machinery, largely because seal components like the 25 35 7 oil seal play a critical role in enhancing product longevity and maintaining equipment efficiency. This article explores the hidden intricacies and critical considerations underpinning the choice of oil seals, adding a layer of seasoned experience, technical expertise, authoritative insights, and trusted information.
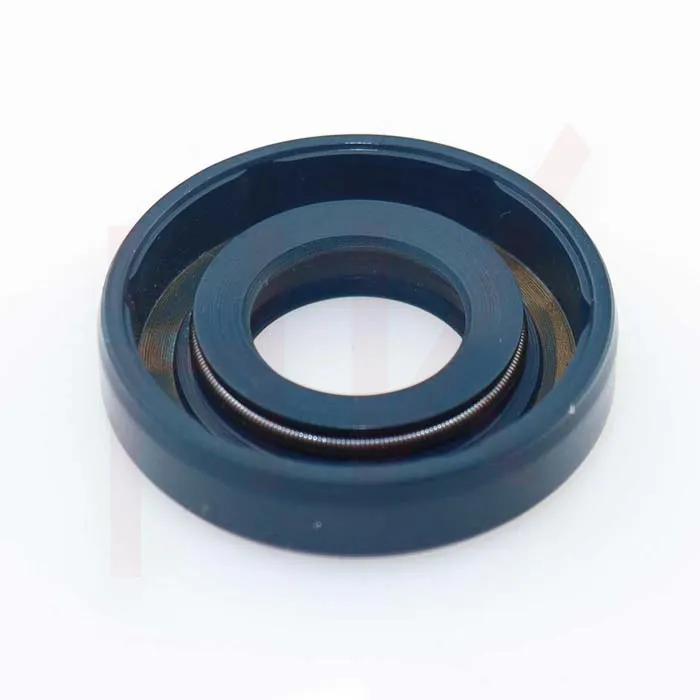
Oil seals, often known as shaft seals or radial lip seals, protect rotating components by preventing fluid leaks between two parts. The numbers 25, 35, and 7 in an oil seal typically refer to its dimensions in millimeters the inner diameter (ID), outer diameter (OD), and width (thickness), respectively. These might seem like basic parameters, but they are foundational to ensuring the correct application and achieving optimal sealing performance.
Experience Expertise in Selection and Application
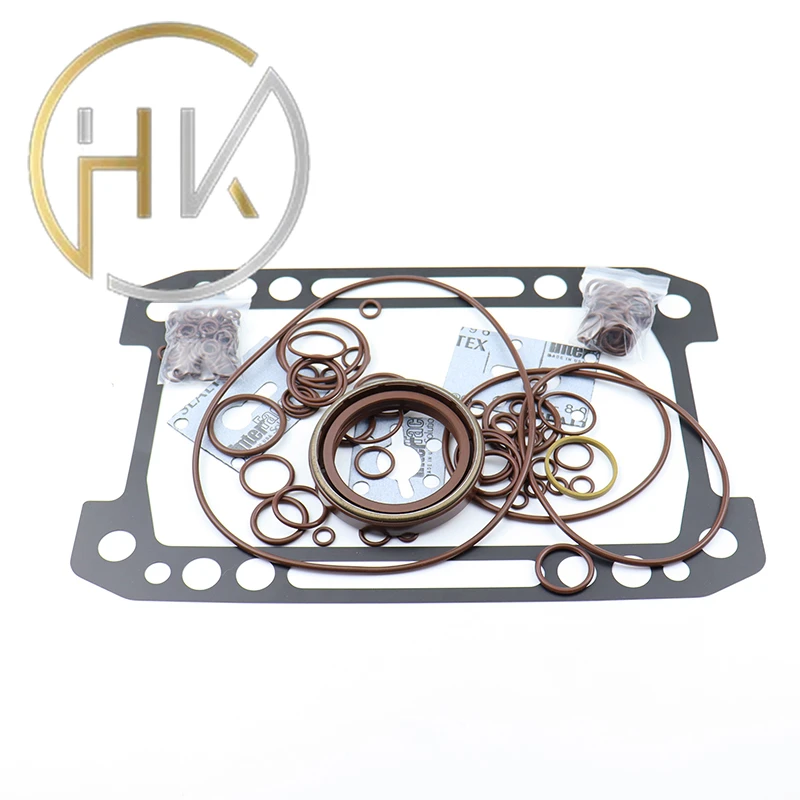
Years of industry experience reveal that a meticulous selection of oil seals can dramatically reduce maintenance costs and prevent equipment downtime. When choosing a 25 35 7 oil seal, engineers should consider the type of fluid being sealed, operational temperature ranges, and environmental conditions such as dust or corrosive substances.
The usability of a 25 35 7 oil seal does not solely hinge on its dimensions.
Material compatibility is equally vital. Nitrile rubber (NBR), for example, is a popular choice for its resistance to oils and simple hydrocarbons, whereas for applications involving high temperatures or aggressive chemicals, a seal made from fluoroelastomer (FKM) might be more suitable.
Furthermore, during installation, ensuring the seal is axially aligned is paramount; even slight misalignments can lead to uneven wear and premature failure. To mitigate this risk, incorporating proper lubrication practices and using installation tools can extend the seal life significantly.
Expertise In-depth Analysis of Materials and Designs
An expert understanding of material science and engineering can elevate the application of oil seals. For instance, the incorporation of a garter spring in the seal design enhances the lip’s flexibility and helps maintain consistent radial force, accommodating a wider range of motion in the shaft.
The introduction of double-lip designs in 25 35 7 oil seals is a notable innovation. The primary lip retains the lubrication within the confines, while the secondary lip acts as a dust excluder in harsher environments. This dual-functionality is crucial in automotive applications, where environmental exposure can jeopardize component integrity.
25 35 7 oil seal
Moreover, the blend of traditional material choice with modern composites allows for custom solutions tailored to specific industrial applications, thereby optimizing both performance and cost.
Authoritativeness Insights from Industry Leaders
Insights from leading manufacturers highlight the ongoing developments in sealing technology. Multiplexure introduced an innovative coating technology that reduces friction on the 25 35 7 oil seal surfaces, not only prolonging the material's life but also boosting energy efficiency.
In authoritative journals, studies point out that seals manufactured with precision machining contribute significantly to reducing the total cost of ownership for machinery. This precision ensures that seals fit perfectly, which minimizes the chances of leaks or damage to the shafts.
Trustworthiness Reliable Performance and Proven Results
The reliability of a 25 35 7 oil seal stems from rigorous testing and field validation. Trusted manufacturers often subject their seals to dynamic testing under various conditions to mimic real-world applications. This not only builds trust with customers but also ensures that the seals meet stringent international standards, such as ISO 6194.
Case studies further illustrate that businesses that invested in high-quality seals, rather than opting for cheaper alternatives, found a substantial return on investment. The costs saved from reduced leakage incidents and maintenance outweighed the initial expenditure, building a compelling case for quality over cost-cutting.
As industries evolve, the call for more efficient, durable, and adaptable oil seals like the 25 35 7 will continue to grow. Armed with real-world experience, expert knowledge, authoritative endorsements, and a guarantee of reliability, businesses can confidently incorporate these components into their systems, ensuring longevity and efficiency are at the forefront of their operational strategies.