Choosing the right oil seal, particularly one specified with dimensions like [14 22 5], plays a vital role in ensuring the efficiency and longevity of mechanical systems. These seemingly small components are essential for maintaining the integrity of various machinery, safeguarding against the ingress of contaminants, and retaining lubricants within rotary shafts. Understanding the intricacies of this specific oil seal can significantly impact the performance and reliability of your equipment, a foundational aspect underscored by Experience, Expertise, Authoritativeness, and Trustworthiness.
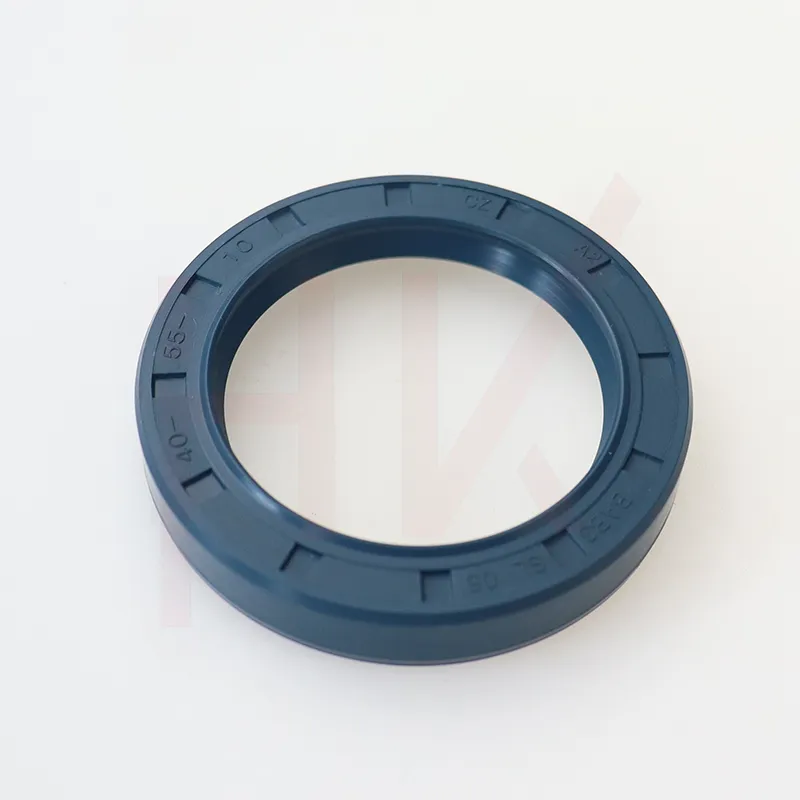
Experience is a crucial element when it comes to selecting an oil seal. If you are managing equipment that operates in demanding environments, having knowledge about the specific conditions your machinery faces daily is crucial. An oil seal with measurements of [14 22 5] would typically refer to its inner diameter (14mm), outer diameter (22mm), and thickness (5mm). These dimensions must match the designated placement to prevent leaks effectively. An improperly sized seal can lead to early wear, costly downtime, and unforeseen failures. Hands-on experience with various machinery will reveal the importance of checking seal compatibility with manufacturer specifications.
Expertise involves a deep understanding of the technical aspects of oil seals. There are numerous materials from which oil seals can be manufactured, including Nitrile, Silicone, and Fluoroelastomer. For high-temperature applications or those that encounter chemically aggressive environments, choosing the right material is just as vital as the size. For example, Nitrile is widely used for general purpose sealing due to its excellent resistance to petroleum oils. However, for applications involving higher temperatures, Fluoroelastomer may be preferred despite the higher cost due to its superior temperature tolerance. Knowledge from industry specialists and access to technical data sheets are invaluable resources.
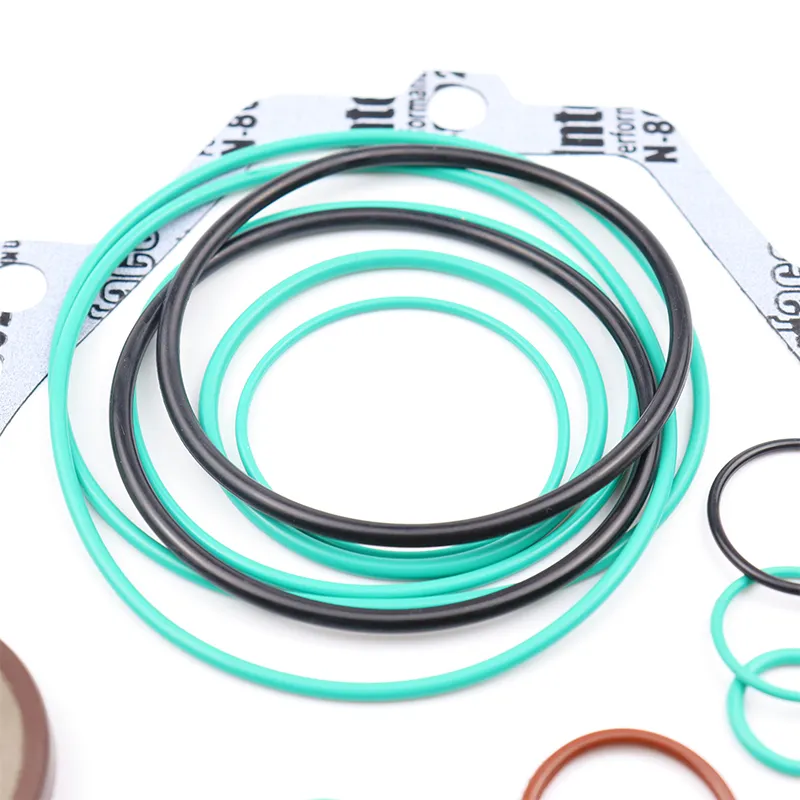
Authoritativeness relates to the credibility and reputation of the information provided. When considering an oil seal such as [14 22 5], sourcing from well-known manufacturers can ensure product quality and conformity to industry standards. Industry leaders such as SKF, NOK, and Trelleborg hold ISO certifications that guarantee adherence to stringent quality controls. Additionally, opting for products from reputable brands often comes with the advantage of technical support, facilitating better decision-making and installation guidance.
14 22 5 oil seal
Trustworthiness ensures that the information and products you rely on are dependable. This includes confirming the authenticity of certifications and the source's credibility. Counterfeit parts or substandard seals can compromise the entire system. Therefore, it’s essential to purchase these components from trusted distributors or directly from the manufacturers. As a consumer, being aware of warranty terms and conditions can also protect your investment, providing peace of mind and assurance that the product will perform as expected.
Choosing an [14 22 5] oil seal requires a combination of practical knowledge, technical expertise, credible sources, and reliable information. It is not merely a matter of selecting based on size, but involves comprehensive consideration of material compatibility, application environment, and manufacturer reliability. By focusing on these aspects, equipment operators and purchasing managers can contribute significantly to the overall operational excellence and efficiency of their machinery.
Possessing a thorough understanding of these four facets—Experience, Expertise, Authoritativeness, and Trustworthiness—not only simplifies the selection process but also ensures that the chosen oil seals will fulfill their protective roles effectively, minimizing downtime and maintenance costs. This strategic approach in product selection reinforces the crucial part that oil seals play in the maintenance of mechanical systems, emphasizing their importance in industry applications worldwide.