Replacing a pump seal kit is an integral part of maintaining optimal pump functionality in many industrial and domestic applications. The complex nature of pump systems demands a comprehensive understanding of seal mechanics to ensure precise replacements, preventing premature failures and costly downtimes.
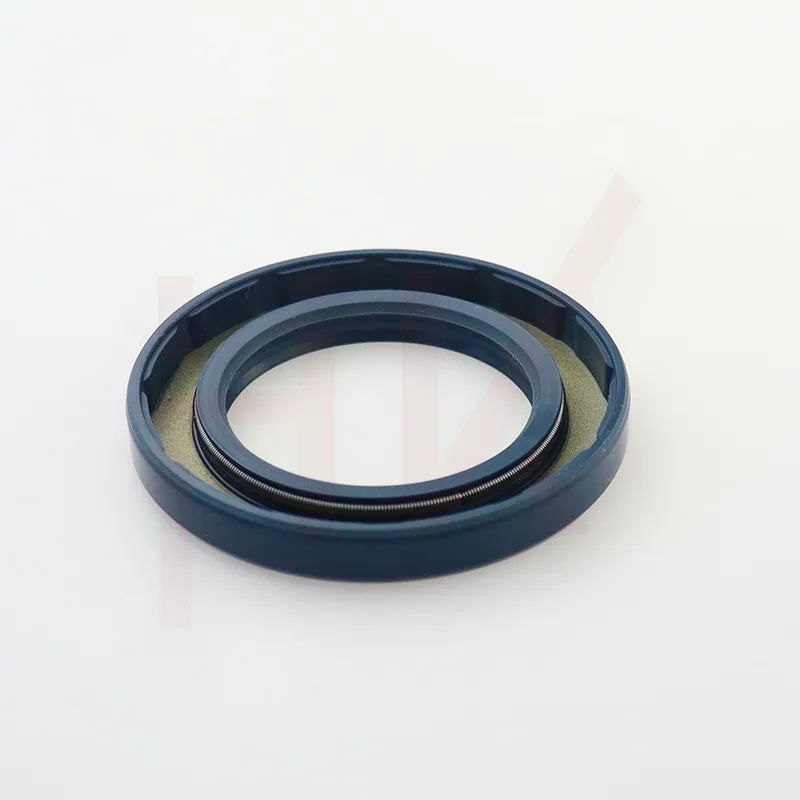
Pump seals play a crucial role in ensuring that a pump operates efficiently by preventing leaks and maintaining pressure within the system. Over time, these seals endure wear and tear due to factors such as pressure fluctuations, temperature changes, and chemical interactions, making their replacement inevitable for sustaining pump performance.
Beginners in the field might find the plethora of seal kits available overwhelming, but expertise comes with familiarity with the pump's specific requirements. Initially, one must identify the type of pump and its operational environment. For example, mechanical seals are often used in dynamic systems dealing with high-pressure fluids, whereas static seals, like O-rings, are more common in steady environments. Choosing the right seal kit directly influences the pump's longevity and efficiency.
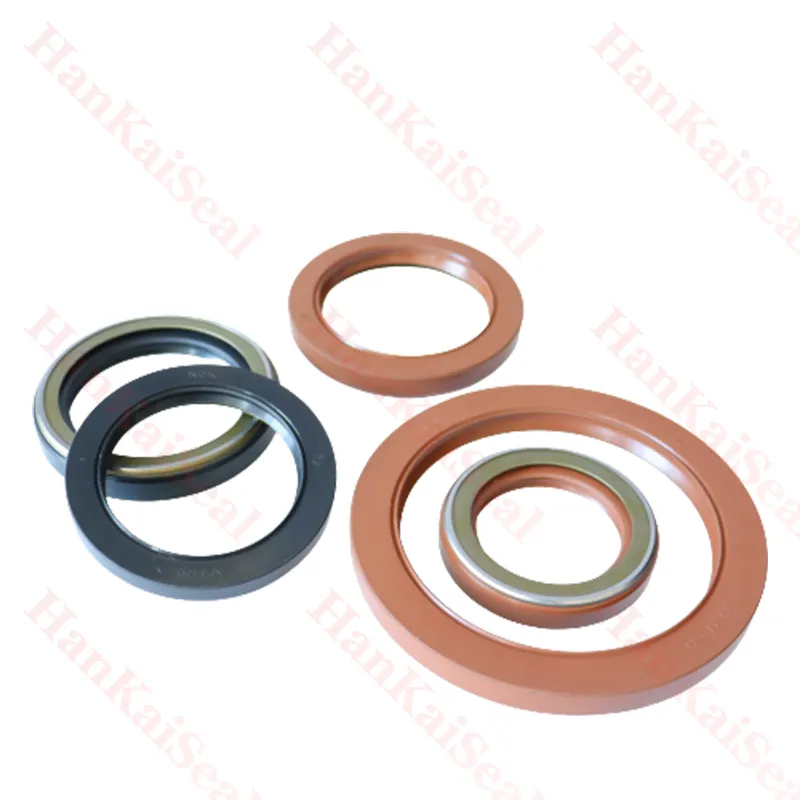
For replacing a pump seal kit, it is paramount to follow a methodical approach. Start by ensuring that the pump is completely disconnected from any power source.
This safety measure cannot be overstated as the primary step in seal replacement. Subsequently, draining the pump system of any residual fluids prevents environmental contamination and provides a cleaner workspace.
Next, the pump must be carefully disassembled. During this process, meticulous observation is essential, noting how components are positioned and secured. Photographing each stage can provide valuable reference points during reassembly. When reaching the seal compartment, defective seals should be cautiously removed to prevent damaging adjacent components. Attention to detail here reflects one’s expertise; any undue force can lead to expensive repairs.
A critical tip in enhancing trustworthiness in this procedure is to examine the pump shaft and housing for signs of corrosion or wear. Even the best seal kit will falter on worn surfaces. If necessary, professional refurbishment might be required to restore these components to their manufactured specifications.
pump seal kit replacement
Upon introducing the new seal, ensure it is lubricated appropriately to reduce friction during initial operation. Also, correctly align the seal, avoiding any angular distortions that might lead to future leakage. Considering environmental influences is also vital; for pumps handling aggressive chemicals, seals fabricated from resistant materials like Viton or PTFE should be selected.
Reassembling the pump involves reversing the disassembly process. Precision in alignment and torque settings is vital to prevent unnecessary stress on the newly installed seals. Expertise dictates the use of calibrated tools to achieve manufacturer-recommended specifications. Each component should seamlessly fit as it did originally, signifying a successful replacement.
Once the pump is reconnected to its power source, conducting rigorous post-installation tests affirms the effectiveness of the seal replacement. Observing for any immediate leaks and ensuring fluid flow and pressure parameters meet the established benchmarks indicates a meticulous job.
Ultimately, the authoritative guidance provided here is rooted in an amalgamation of field experience and advanced mechanical knowledge. A well-replaced pump seal not only extends the life of the pump but also reflects diligence in maintaining operational integrity. In a sector where reliability is paramount, following a detailed replacement strategy fortifies one's reputation as a skilled professional in pump maintenance. As technology and materials continue to evolve, adapting these practices to include the latest developments ensures a competitive edge, satisfying both operational and environmental safeguarding.
By following these guidelines, individuals and industries can significantly optimize their pump system's performance and assure longevity, underscoring the pivotal role of expert maintenance in equipment reliability.