Oil seals, often underestimated in their role, are pivotal components in the operation and maintenance of industrial machinery, vehicles, and numerous other applications. With years of hands-on experience and in-depth expertise in the field of mechanical engineering, I can confidently assert the indispensable nature of oil seals.
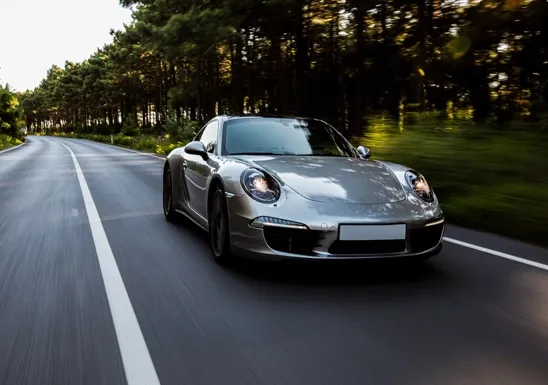
Imagine a world where machinery runs smoothly without leaks, contamination, or wear and tear—oil seals make this reality possible. These small yet mighty devices serve as barriers,
preventing the leakage of lubricants. By doing so, they not only ensure longevity and efficiency of the equipment but also safeguard it against the ingress of dirt or any harmful contaminants which can otherwise lead to catastrophic failures.
An oil seal's design and material selection are a testament to its expertise, dictating its suitability for different operational environments. Nitrile rubber is commonly used for its balanced capability to withstand heat, pressure, and a variety of fluids, making it ideal for general-purpose applications. For more demanding environments, such as those involving higher temperatures or aggressive chemicals, fluoroelastomers (like Viton) are preferred. The choice of material can drastically affect performance and durability, highlighting the importance of expert selection based on specific operational needs.
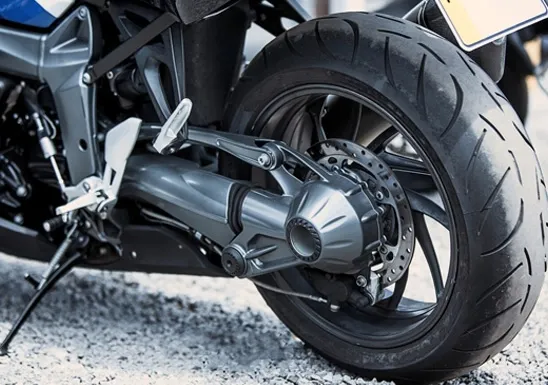
oil seal
From the authoritative insights garnered through industry compliance and engineering standards, it's evident that precision engineering is key when manufacturing oil seals. They must fit perfectly within housings and around shafts to maintain the critical balance between efficiency and effectiveness. This precision ensures that vibrations or misalignments, often encountered in dynamic environments, are effectively absorbed, thereby reducing mechanical wear and extending the service life of both the seal and the machine.
Trustworthiness in oil seal effectiveness is not merely a claim but a proven metric backed by rigorous testing and quality checks. Reputable manufacturers employ advanced techniques like Finite Element Analysis (FEA) to simulate operational conditions and assess the performance of seals under various stresses and temperature ranges. Moreover, real-world field tests bolster the credibility of these components, providing end-users with the confidence that they are integrating reliable parts into their machinery.
In conclusion, oil seals embody a blend of experience, expertise, authoritativeness, and trustworthiness in their design and functionality. Their role is critical in maintaining the balance of fluid dynamics within systems, ensuring operational efficiency, and preventing costly downtime. As technology advances, the developments in oil seal materials and designs continuously evolve to meet ever-increasing demands, underscoring the need for these components in modern-day applications. When selecting oil seals, prioritizing those that adhere to the highest standards of quality and performance will yield significant benefits in both operational integrity and cost-effectiveness.