Gearbox seals are vital components in the automotive and industrial machinery sectors, performing the essential function of preventing fluid leaks and maintaining optimal pressure within gearboxes. Understanding the nuances of gearbox seals can significantly enhance the efficiency and lifespan of the machinery, making it an essential area for managers, engineers, and technical operators to grasp with authority, precision, and trust.
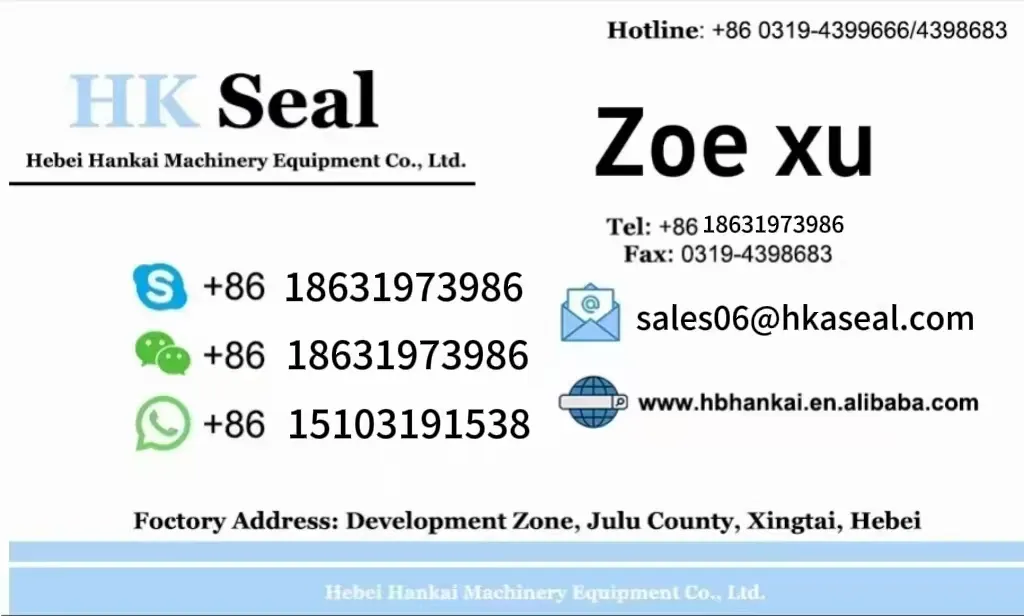
The first element to consider is the types of gearbox seals available in the market. These primarily include lip seals, mechanical seals, and labyrinth seals, each with distinct properties suited for different applications. Lip seals, popular for their simplicity and affordability, work effectively in less demanding environments. They consist of a flexible lip that presses against a rotating shaft, creating a seal that prevents leakage. However, in high-pressure and high-temperature conditions, mechanical seals provide superior performance with their complex construction, offering durability and precision. Labyrinth seals, although not directly touching the shaft, inhibit leaks through their intricate passageways, using centrifugal force to combat fluid escape.
With specialization in the field, it is critical to address the materials used in the manufacture of gearbox seals. Material selection significantly impacts the seal's performance, dictating its resistance to wear, temperature, and chemical exposure. Common materials include elastomers like nitrile rubber and fluorocarbon, which offer flexibility and chemical resistance. More advanced materials like PTFE (Polytetrafluoroethylene) and silicone are employed in extreme applications requiring robust thermal and chemical properties. Selecting the appropriate material demands a thorough understanding of the operational environment, including the temperatures, pressures, and types of fluid involved.
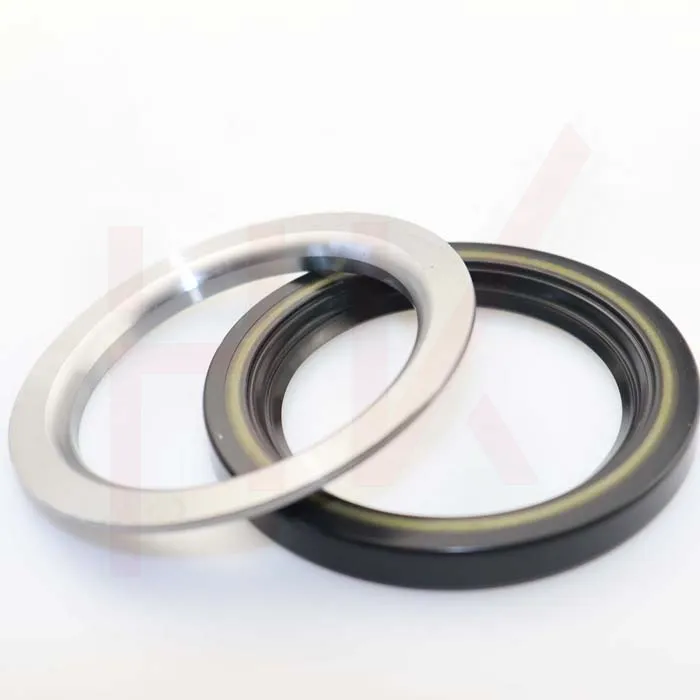
Installation and maintenance of gearbox seals directly affect their operational longevity and efficiency. Proper installation involves ensuring the shaft surface is impeccably finished and correctly aligned to minimize wear.
Misalignment or improper surface finishes can lead to premature seal failure. Regular inspections, aligned with a maintenance schedule, help in identifying early signs of wear such as oil leaks, which could escalate into significant mechanical failures if ignored. In-depth knowledge of maintenance best practices will bolster the operational integrity of the gearbox.
gearbox seals
From an engineering perspective, innovations in seal design and technology continue to evolve. Industrial revolutions and advancements in material science have ushered in new classes of seals that are more resistant to extreme conditions, boasting longer lifespans and better performance metrics. High-performance seals like those combined with hydrodynamic aids improve sealing efficiency while reducing friction and heat buildup—key innovations that extend the duration between maintenance cycles.
The practical application of gearbox seals spans multiple industries, each demanding unique solutions tailored to specific operational challenges. Automotive manufacturers rely heavily on high-performance gearbox seals to boost vehicle performance, reduce emissions, and improve fuel efficiency. Similarly, industries like aerospace, manufacturing, and oil and gas, harness advanced seal technologies to ensure machinery operates at peak efficiency, bolstering safety and productivity.
Investment in high-quality gearbox seals and a comprehensive understanding of their operation are non-negotiable for businesses seeking to maintain competitiveness in today's marketplace. Trustworthy suppliers with a track record of providing durable, innovative solutions should be prioritized. Engineers and technicians should remain informed about the latest trends and technologies in sealing systems to advocate for the best solutions within their operations.
In conclusion, gearbox seals, while often underestimated, are critical components warranting detailed attention. Expertise in selecting, installing, and maintaining these seals enhances machinery reliability and efficiency, turning innovative seal technology into a vital element of modern industrial success. Balancing cost with performance and reliability ensures that the machinery runs smoothly, minimizing downtime and maximizing productivity, promising sustained competitive advantages in highly demanding environments.