Hydraulic cylinder seals play a crucial role in ensuring the effective performance and longevity of hydraulic systems. Their primary purpose is to prevent leaks, maintain pressure, and safeguard the system from contaminants. Over time, however, these seals can wear out or become damaged, necessitating replacement to keep the machinery running efficiently. This article delves into the intricacies of hydraulic cylinder seal replacement, providing insights drawn from years of experience and expertise in the field.
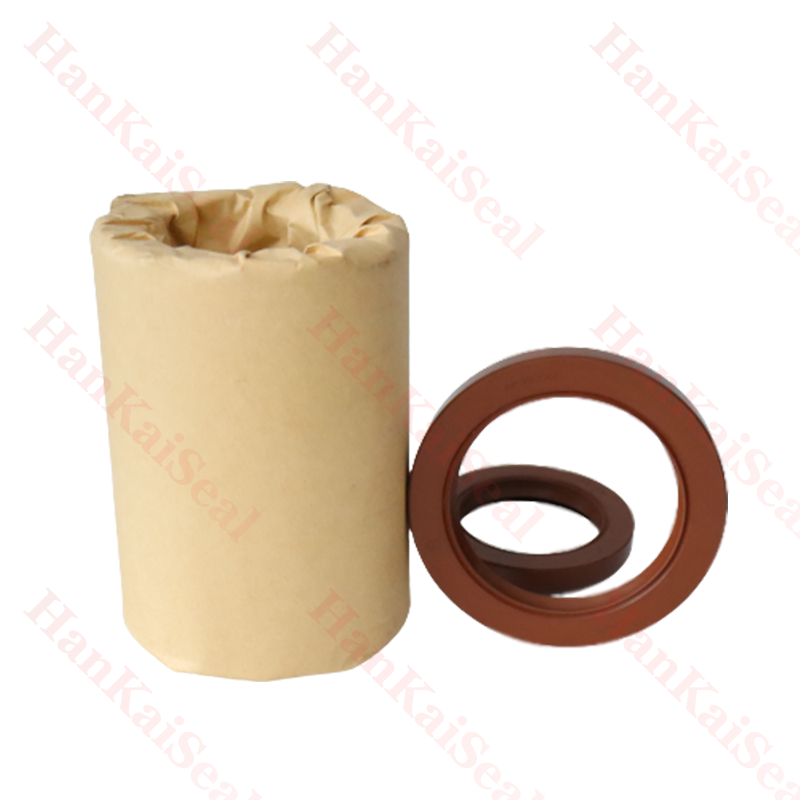
First and foremost, understanding the types of hydraulic cylinder seals is imperative. Seals come in various forms, including rod seals, piston seals, and wiper seals, each serving a distinct function within the cylinder. Rod seals, for example, are designed to prevent fluid leakage from the cylinder, while piston seals maintain the pressure necessary for the hydraulic system's operation. An effective seal replacement process begins with identifying the specific type of seal that needs attention, as well as understanding the symptoms of seal failure, such as fluid leakage, loss of pressure, or unusual noises.
The process of replacing hydraulic cylinder seals should always start with a comprehensive inspection. This involves disassembling the hydraulic cylinder carefully and examining each seal for wear or damage. Common indicators of seal deterioration include hardening, cracking, or deformation. Professionals approach this task with meticulous attention to detail, as missing even a minor flaw can lead to costly system failures. It is also essential to clean all components thoroughly to remove any dirt or debris that may interfere with the performance of the new seals.
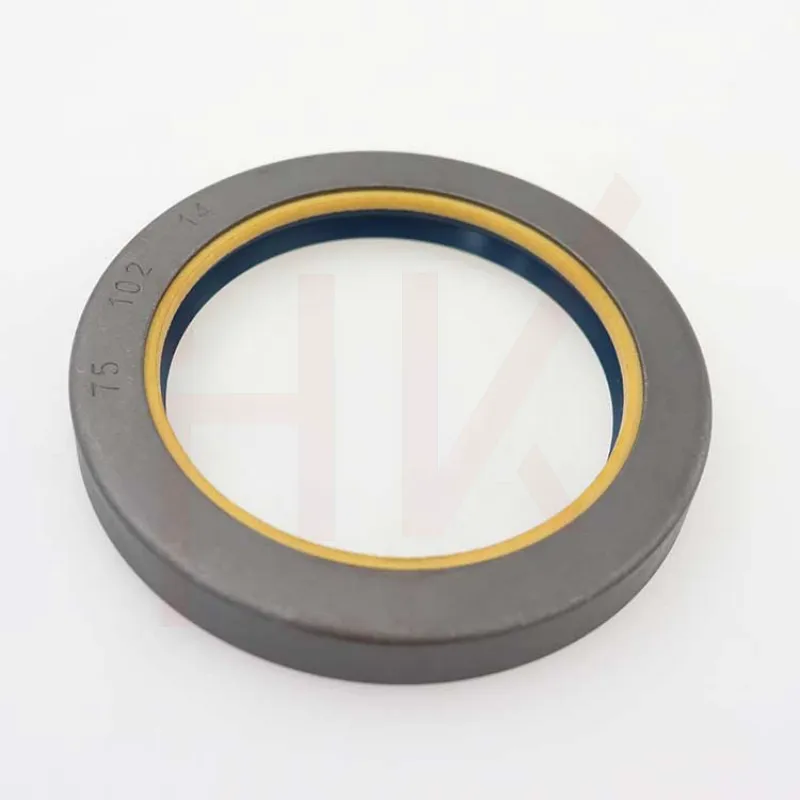
Selecting high-quality replacement seals is the next critical step. When choosing seals, one must consider factors such as material compatibility, environmental conditions, and the specific demands of the application. High-performance seals are often made from materials like polyurethane or nitrile, known for their durability and resistance to wear and temperature fluctuations. Opting for reputable manufacturers ensures that the seals meet the necessary standards and specifications, thereby enhancing the reliability of the hydraulic system.
hydraulic cylinder seal replacement
Installation of the new seals demands precision and expertise. The process requires specialized tools and techniques to avoid damaging delicate components. Experienced technicians follow a strict protocol, ensuring that the seals are properly seated and aligned. Incorrect installation can lead to premature seal failure, resulting in downtime and increased maintenance costs. Therefore, professional training and experience are invaluable in executing this task effectively.
Testing the hydraulic system after seal replacement is a step that should never be overlooked. This involves running the system under various parameters to ensure that the new seals are functioning as expected and that there are no leaks. It also provides an opportunity to adjust the system settings if necessary, ensuring optimal performance. Regular maintenance checks can help catch any potential issues early, prolonging the life of the seals and the hydraulic system overall.
In conclusion, hydraulic cylinder seal replacement is a task that necessitates a blend of experience, expertise, authoritativeness, and trustworthiness. Each stage, from inspection to installation, requires careful consideration and skill to ensure the system's continued efficiency and reliability. By prioritizing quality in seal selection and upholding rigorous maintenance practices, companies can safeguard their hydraulic equipment against unexpected failures and maximize operational uptime. Embracing new developments in seal technology and keeping abreast of industry standards further fortifies this commitment to excellence, ensuring that the hydraulic systems not only perform optimally under current conditions but are also prepared to meet future challenges.