The 35x52x7 oil seal is a small yet crucial component widely used in mechanical equipment and automotive industries. Its main purpose is to seal lubricants within a confined space, preventing leakage and protecting the machinery from dust, dirt, and other contaminants. This necessity makes understanding its function, application, and selection essential for maintaining machinery performance and reliability.

Oil seals, specifically the 35x52x7 variant, are designed to fit shafts with a diameter of 35mm, housing bore of 52mm, and a width of 7mm. This specific size is a standard in many mechanical systems. Their application spans across various industries, predominantly in automotive engines, gearboxes, and axles, as well as in industrial pumps and equipment.
From experience, consistent and trouble-free machinery operation hinges on selecting the right oil seal. A poor choice can lead to lubricant leakage, contaminated environments inside machinery, and ultimately, premature equipment failure. Therefore,
the quality of the oil seal should never be compromised.
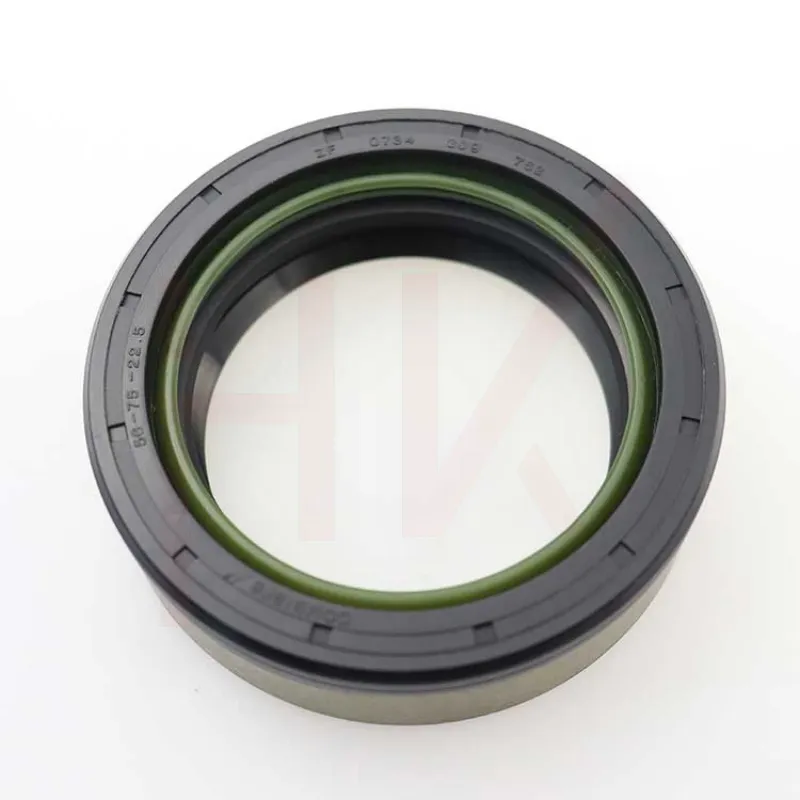
In terms of expertise, understanding the materials used for oil seals is critical. These seals are typically made from high-quality nitrile rubber (NBR) due to its excellent resistance to petroleum-based oils and hydraulic fluids. Moreover, nitrile rubber performs well at a temperature range of -40°C to 120°C, making it suitable for varied applications. For environments exposed to higher temperatures and aggressive chemicals, higher-grade materials such as Fluoroelastomer (Viton) may be required.
Knowing the mechanics and physics behind oil seals is also important. The 35x52x7 seal features a flexible lip that makes contact with the shaft, creating a barrier against fluid leakage. This barrier's effectiveness depends on factors such as shaft speed and pressure, both of which should be within the seal’s design limits to function optimally.
35x52x7 oil seal
Furthermore, installation expertise is vital to ensure longevity and performance. During installation, the seal’s lip must be lubricated, and installation should be done with proper tools to avoid lip damage. Any debris on the shaft or in the seal seat can cause premature wear and leaks.
Authoritativeness in this area is underscored by adhering to industry standards and certifications. High-quality oil seals often comply with rigorous ISO standards, ensuring they meet or exceed performance and quality benchmarks. Therefore, selecting seals from reputable manufacturers who provide certified products is advisable.
When discussing trustworthiness, consider the supplier’s reliability. Engaging with suppliers who offer technical support and after-sales service is beneficial. A trustworthy supplier should offer comprehensive warranties and have a reputation for quality assurance. Client testimonials can be a useful reference to gauge the supplier’s reliability and the product’s performance.
Complementary to understanding the product and supplier, leveraging advancements in seal technology can offer improved performance. Recent developments include using advanced materials and computer-aided design to enhance the seal’s life span and efficiency. Emerging technologies in digital monitoring can also facilitate predictive maintenance, reducing unexpected seal failures by providing alerts on wear conditions.
In conclusion, the 35x52x7 oil seal may appear to be a simple component at first glance, but its significance is immense. Its role in ensuring machinery efficiency and reliability cannot be understated. Through the effective selection, installation, and monitoring of these seals, industries can minimize downtime and optimize performance. By applying experience and expertise, while valuing authoritativeness and trustworthiness, one can ensure that the choice and application of these oil seals contribute positively to operational success.