Hydraulic ram oil seals are indispensable components in the assembly and maintenance of hydraulic systems. These seals, serving as critical barriers between high-pressure fluids and the external environment, ensure that the hydraulic systems operate smoothly and efficiently. In the ever-evolving world of hydraulic engineering, understanding the nuances of hydraulic ram oil seals can set your enterprise apart in terms of operational excellence and cost-efficiency.
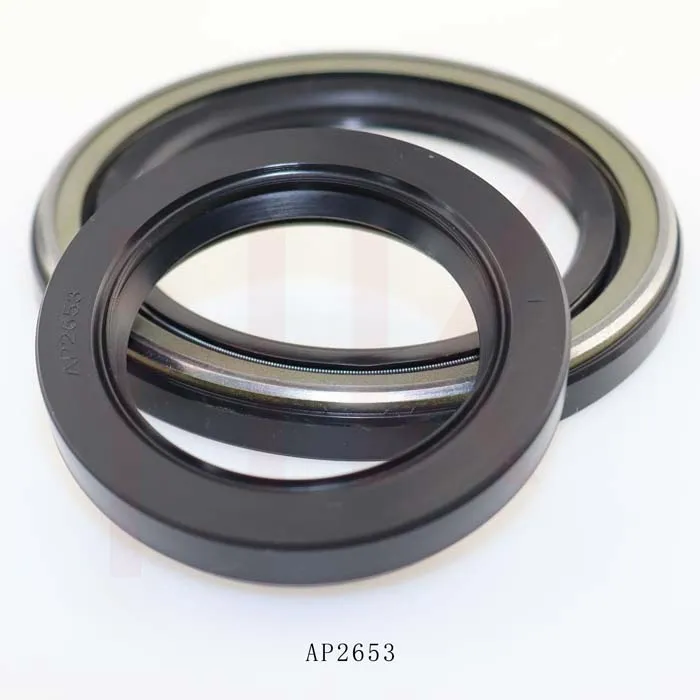
In recent years, advancements in materials science have introduced a plethora of new materials for hydraulic ram oil seals, each offering unique benefits suitable for various industrial use-cases. The traditional rubber seals are being complemented, and in some cases replaced, by advanced composites and polymers that exhibit superior resistance to extreme temperature variations and chemical exposures. Engineers must be informed about these materials, such as Polytetrafluoroethylene (PTFE) and Fluoroelastomers, to make strategic choices that best fit their operational requirements.
From an experiential standpoint, the correct implementation of hydraulic ram oil seals can dramatically extend the life of hydraulic cylinders and minimize the maintenance downtimes. However, to harness these benefits, meticulous attention to detail is vital during the installation process. For instance, surface finishes of mating hardware should be checked for compatibility with the seal materials to avoid friction and resultant wear.

Professionals in hydraulic engineering continually emphasize the importance of selecting seals with the appropriate pressure rating. Misapplication can result in catastrophic seal failure, leading to hydraulic fluid leaks that not only waste resources but also pose environmental hazards. Thus, partnering with reputable suppliers who test their seals to rigorous international standards, such as the ISO 3601, adds an authoritative layer of quality assurance to your procurement process.
hydraulic ram oil seals
Authenticity and trust in hydraulic ram oil seals also hinge on regular maintenance and inspection routines. It is advised that system operators conduct a thorough visual inspection of the seals at regular intervals for signs of wear, extrusion, or cracking. Many experienced hydraulic technicians test the hardness and elasticity of the seals periodically to ensure their ongoing efficacy.
With an eye on the future, the integration of sensor technologies within hydraulic systems is emerging as a promising trend. These sensors can monitor the condition of the hydraulic ram oil seals in real-time, predicting potential failures before they become critical, thereby enabling preemptive maintenance strategies. This digitization not only bolsters trust in seal reliability but also aligns with contemporary digital transformation trends observed across industries.
In conclusion, staying updated with the latest materials, executing precise installation, ensuring compliance with international standards, and adopting modern technologies are critical steps in the successful implementation of hydraulic ram oil seals. By prioritizing these elements, companies can enhance their hydraulic system performance, ensure safety, and achieve significant economic savings.
Ultimately, hydraulic ram oil seals, while seemingly minor components, are integral to the functionality and sustainability of hydraulic systems. Leveraging expert knowledge and authoritative practices in seal selection and maintenance can empower organizations to optimize their hydraulic systems, ensuring they remain robust, efficient, and environmentally sound over the long haul.