A hydraulic press machine oil seal plays a critical role in ensuring the efficiency and longevity of hydraulic presses. These seals are expertly designed to prevent leaks and maintain pressure within the hydraulic system, which is crucial for the press's optimal performance. Understanding the importance and functionality of these oil seals can save industries from costly downtime and prolong machinery lifespan.
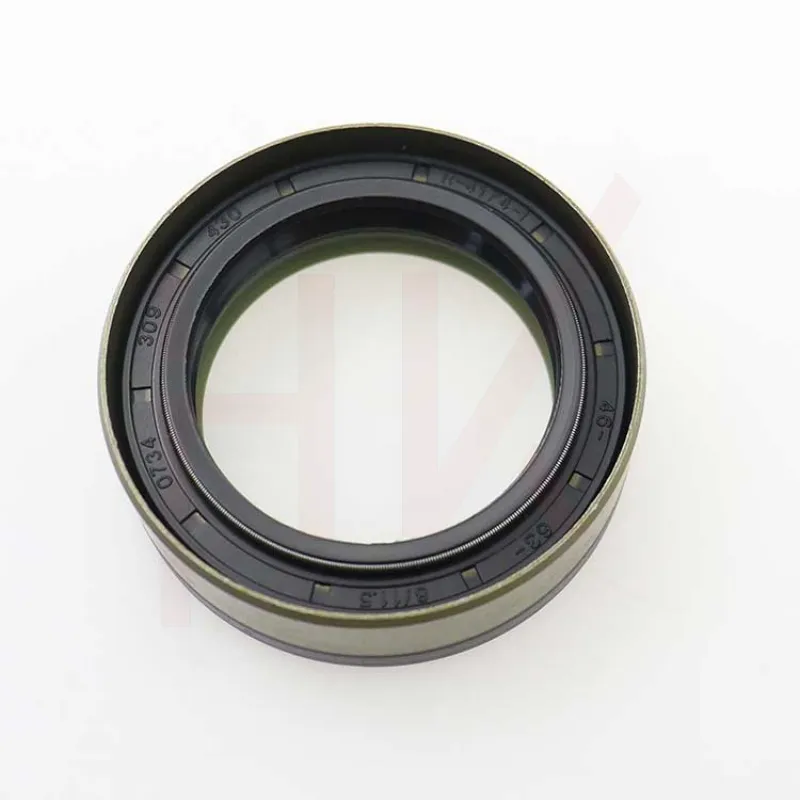
Hydraulic press machines are found at the heart of many industrial operations, from automotive to aerospace and material processing. Such versatility demands uncompromising reliability, which is where hydraulic oil seals demonstrate their expertise. Constructed from robust materials such as nitrile rubber, fluoroelastomer, and PTFE, these seals withstand extreme temperatures and pressures, preventing fluid from escaping the hydraulic system.
Expertise in manufacturing hydraulic press oil seals is vital as each industrial application may exert unique demands. Manufacturers employ precision engineering to craft oil seals that withstand specific operational environments, ensuring compatibility and efficiency. This attention to detail in design and material selection speaks volumes about the manufacturer's authoritative stance in the industry.
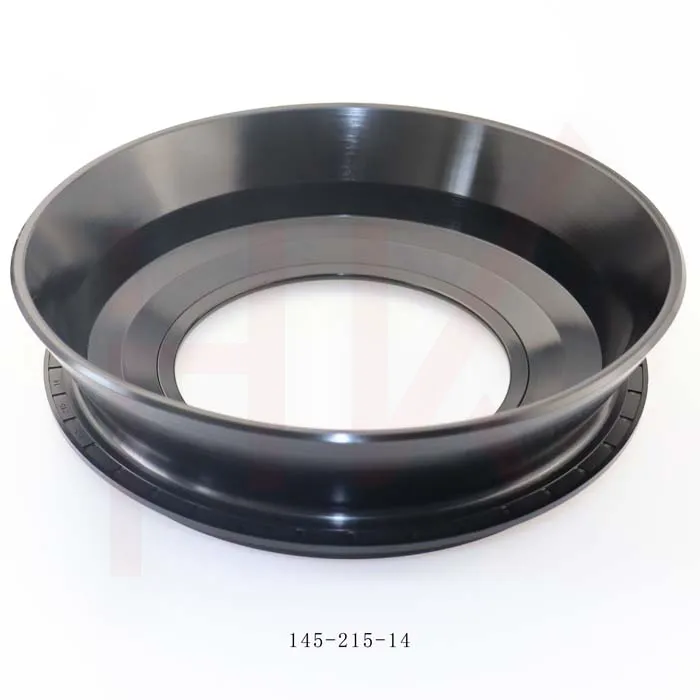
For technicians and engineers with hands-on experience, the ease of installation and the longevity of an oil seal are paramount. A well-designed oil seal should be user-friendly, allowing for straightforward installation and replacement, which minimizes machine downtime. It is the confidence in these seals, built through years of engineering expertise and rigorous testing, that ensures trustworthiness and solidifies their place as an industry standard.
hydraulic press machine oil seal
In ensuring that hydraulic systems function efficiently, the oil seal prevents contamination from external elements, which can otherwise compromise hydraulic fluid integrity. Contaminants such as dust and moisture are kept at bay, hence preserving the internal components of the hydraulic press from premature wear. This protective barrier is testimony to the oil seal's efficiency and underlines its critical role in maintaining hydraulic system health.
Furthermore, a reliable oil seal extends the maintenance cycle of a hydraulic press, translating into cost savings. Industries benefit from reduced machine servicing intervals, cutting down on labor costs and spare parts procurement. Investing in quality oil seals equates to investing in the machine’s future, making them an indispensable component in modern hydraulic press machinery.
The evolution of oil seal technology continues to advance, with manufacturers committed to exploring new materials and crafting innovative designs that meet the progressive demands of industry. From traditional press types to contemporary CNC hydraulic presses, these seals are adapting to provide OEMs and end-users the trust they require to push their operations forward.
In summary, a hydraulic press machine oil seal is not merely a component but an embodiment of reliability in hydraulic press operations. Its role as a protector, pressure maintainer, and cost saver makes it an invaluable asset to industries relying on hydraulic machinery. By focusing on continuous improvement and understanding industry-specific needs, oil seals will continue to maintain their standing as an essential element in ensuring seamless industrial operations.