With the surge in demand for effective machinery maintenance and longevity, the importance of bearing dust seals has grown significantly. These unassuming components play a pivotal role in safeguarding bearings from contaminants, thus enhancing equipment reliability and performance.
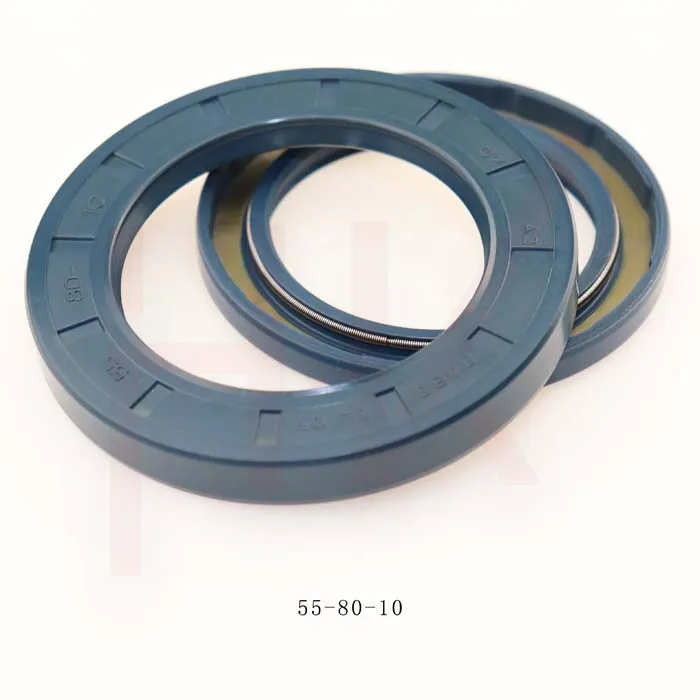
From the get-go, understanding the fundamental role of bearing dust seals sets the stage for their significance in mechanical systems. These seals act as barriers against environmental dust and debris, which, if uninhibited, can lead to increased friction, overheating, and eventually, the premature failure of the bearing itself. For industries reliant on precision and uptime, such as aerospace, automotive, and manufacturing, the implications of bearing seal failures can be both costly and catastrophic.
The efficacy of bearing dust seals lies in their design and material composition. Generally constructed from robust and resilient materials like rubber, silicone, or polyurethane, these seals are designed to withstand harsh operational environments characterized by extreme temperatures, varied pressure ranges, and exposure to chemicals. Advanced designs incorporate features like labyrinth paths which further deter dust ingress, promoting optimal performance of the bearing assembly.
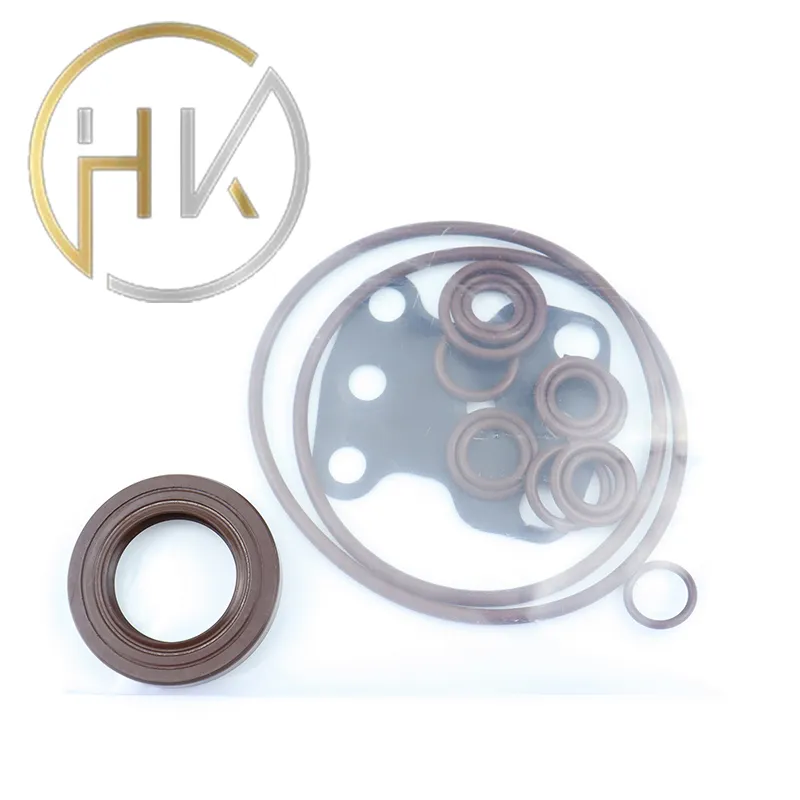
Expertise in choosing the right bearing dust seal is an invaluable skill for maintenance engineers and product designers. The selection process incorporates considerations such as the type of load on the bearing, the operational environment, rotational speed, and specific industry requirements. For instance, in high-speed applications, low-friction seals are essential to reduce torque and wear, enhancing overall efficiency.
bearing dust seal
Field experience has long underscored the cost-saving benefits of investing in high-quality bearing dust seals. A comprehensive understanding of how these seals can mitigate operational disruptions enhances an industry professional's capabilities in preventative maintenance. For example, in a case study from the mining sector, implementing more robust sealing solutions reduced unscheduled downtime by 25%, showcasing the seals' capacity to improve productivity while cutting maintenance costs.
In providing recommendations, always consider seal compatibility with the bearing type and lubricant involved. Understanding the interactions between these components ensures a longer service life and saves on replacement investments, aligning with industry best practices. When possible, consult with manufacturers or seasoned experts to ensure the compatibility and efficacy of these seals within specific machinery setups.
Acquiring authoritative knowledge in bearing dust seals fosters trustworthiness in professional circles. Engineers and technical teams that prioritize the right sealing solutions build a reputation for reliability and excellence. Furthermore, knowledge sharing through seminars, white papers, and professional forums can enhance collective understanding and innovation in sealing technology.
Ultimately, the integration of top-tier bearing dust seals is not just about protection; it's about precision engineering that champions equipment longevity, enhances operational efficiency, and offers substantial cost benefits over the equipment's lifecycle. Those equipped with the skills and knowledge to effectively implement and manage these components will invariably advance in sectors where technical excellence is paramount.