Wiper seals, often understated yet essential components, serve as the unsung heroes in myriad mechanical systems. These pivotal components are meticulously designed to ensure that contamination remains outside of cylinders and machinery, thus maintaining the optimal performance and longevity of the equipment they guard.
Their role is not just preventative; it’s vital. Offering more than just protection, wiper seals enhance the efficiency and durability of systems across industries.
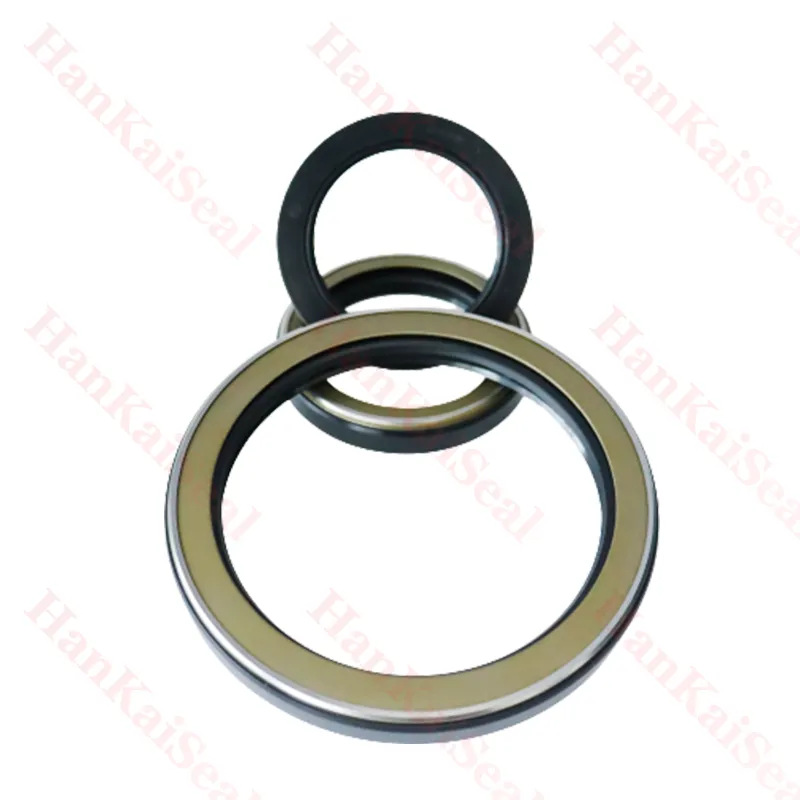
Experience in deploying wiper seals across various applications reveals their importance in preventing dust, dirt, and moisture from invading and compromising mechanical assemblies. While seemingly a minor part, their failure can lead to significant system breakdowns. In industries like automotive manufacturing, ride comfort and vehicle longevity heavily rely on the integrity of wiper seals. They work tirelessly in the background, significantly reducing maintenance costs and preventing critical failures.
Expertise in the development and application of wiper seals is drawn from a vast array of research and development efforts across engineering fields. These seals typically consist of robust materials like polyurethane, rubber, and PTFE (polytetrafluoroethylene), each selected for its unique properties and compatibility with specific environments. Modern advancements have seen the integration of hybrid materials blending these elements, granting wiper seals superior resilience against extreme temperatures, friction, and chemical exposure.
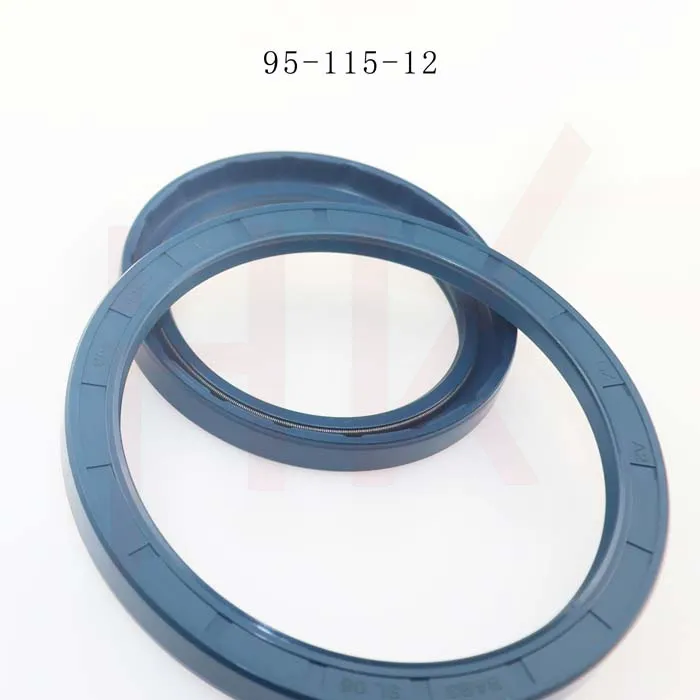
In hydraulics and pneumatics, the authority of wiper seals cannot be overstated. They function as the first line of defense against operational hazards. By preventing abrasive particles and contaminants from entering hydraulic systems, they maintain the integrity of internal seals, thereby safeguarding against potential fluid leaks and pressure deficiencies. Their proper application ensures that these systems function seamlessly, reducing downtime and extending equipment life—a testament to their critical role in equipment reliability and efficiency.
Trustworthiness in the performance of wiper seals is not an arbitrary claim; it is borne out of extensive testing and standards compliance. Recognized industry standards, such as those from ISO (International Organization for Standardization) and SAE International (Society of Automotive Engineers), set rigorous benchmarks that wiper seals must meet or exceed. These standards ensure that seals perform consistently under specified conditions, providing end-users with confidence in their applications.
The technical innovation surrounding wiper seals has been notable. Advanced manufacturing techniques have led to the development of seals with enhanced lip designs that improve scraping and wiping efficiency while minimizing drag. This evolution in design not only prolongs the seal's life but also optimizes mechanical performance by reducing energy losses due to friction.
wiper seals
For industries heavily reliant on mechanical operations, selecting the right wiper seal involves a comprehensive understanding of the operating environment, the type of contaminants expected, and the specific mechanical requirements. OEMs (Original Equipment Manufacturers) benefit from consulting with seal manufacturers early in the design process to tailor wiper seals that meet the nuanced needs of their equipment.
In heavy-duty industrial machinery, for instance, larger wipers with reinforced materials and convoluted designs provide necessary durability and protective coverage. Conversely, in precision instruments, compact and smooth-profiled wipers are imperative to avoid introducing unnecessary friction or disruption.
From an operational perspective, maintaining wiper seals is straightforward yet crucial. Regular inspections and replacements as part of preventive maintenance schedules prevent the gradual degradation that can lead to substantial system failures. When signs of wear, hardening, or cracking are evident, timely replacement ensures continued protection and optimal performance.
The continuous advancement in wiper seal design and technology promises even greater future efficiencies. Emerging materials with self-lubricating properties, for example, show potential in further reducing maintenance needs and extending service life. Moreover, innovations in environmental sustainability see the development of more environmentally friendly materials without compromising on performance.
In conclusion, wiper seals, while often overshadowed by more complex mechanical components, are integral to the reliable and efficient operation of systems across varied industries. Their design and application demand a high level of expertise and precision, underscored by extensive research and compliance with rigorous standards. They are a cornerstone of mechanical system integrity, ensuring that equipment operates under optimum conditions while safeguarding it against the intrusions of a harsh environment. Their trustworthiness is not simply a feature but a result of conscientious engineering and innovation—a testament to their role as unsung yet indispensable guardians of machinery.