Unlocking the Mysteries of 35-72-10 Oil Seals The Cornerstone of Mechanical Resilience
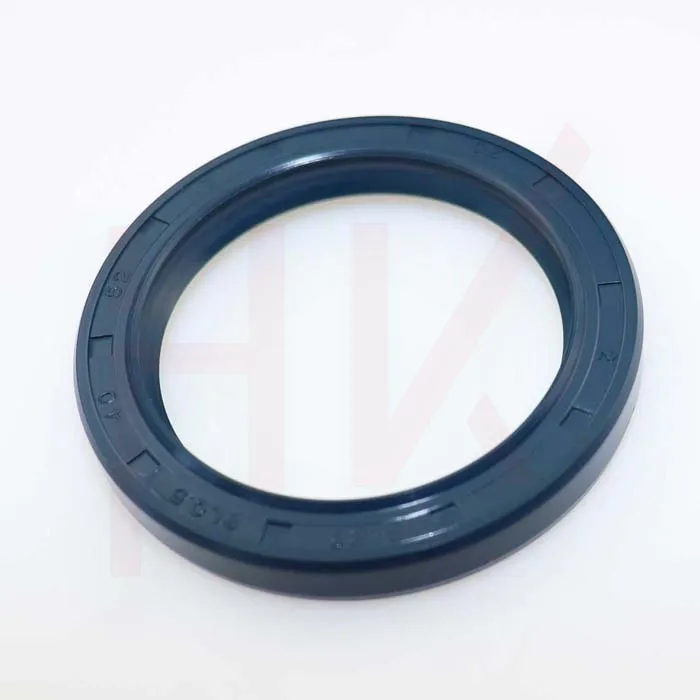
In the world of mechanical engineering and automotive components, oil seals play a pivotal role in ensuring the longevity and performance of machinery. Among the plethora of sizes, the 35-72-10 oil seal stands out as a vital component for numerous applications. Manufacturers and engineers often find themselves delving into the intricacies of these oil seals to maintain operational efficiency and prevent leakage, contamination, and system failures.
When it comes to experience in handling 35-72-10 oil seals, industry veterans highlight the importance of understanding their construction and function. These seals, typically made from high-quality rubber compounds, are designed to withstand aggressive contaminants and harsh environmental conditions. Their fundamental role is to keep lubricants from escaping the space between the rotating shaft and stationary housing. This is crucial; any failure in their function could lead to machinery breakdowns, unscheduled maintenance, and costly downtime.
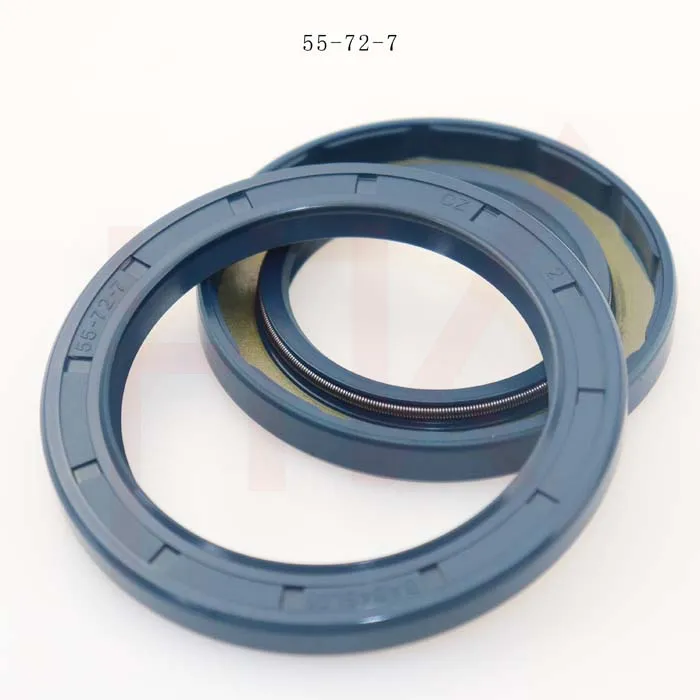
Expertise in selecting and installing oil seals is critical. Engineers need to consider several factors such as temperature ranges, pressure exposure, shaft speed, and environmental conditions. The 35-72-10 oil seal is engineered to fit shafts with a diameter of 35mm, an outer diameter of 72mm, and a width of 10mm. This dimensional precision ensures a perfect fit, which is essential for effective sealing. Selecting the right material composition based on the application—whether it requires resistance to heat, ozone, or chemicals—can significantly impact performance and longevity.
Manufacturers of oil seals wield authority in the marketplace by setting standards for quality and innovation. High-caliber manufacturers utilize advanced materials such as nitrile rubber, fluorocarbon, and silicone, each offering distinct advantages. Nitrile rubber, for instance, provides excellent resistance to oil and fatigue, making it suitable for general-purpose applications, while fluorocarbon offers superior heat and chemical resistance.
35 72 10 oil seal
In consulting industry professionals, trustworthiness often emerges as a paramount concern. It isn't only about a seal's specification on paper but also its real-world performance. Reputable brands often subject their seals to rigorous testing, simulating extreme conditions to ensure reliability. Such measures instill confidence in consumers who depend on these components to protect their machinery assets.
The successful application of a 35-72-10 oil seal involves much more than simply fitting it in place.
Proper installation practices are essential. Ensuring the shaft surface is clean and free of nicks or grooves reduces the risk of seal damage and leakage. Lubricating the seal's lip during installation can prevent dry running at startup, which could otherwise result in rapid wear or damage.
Innovation continues to enhance the capabilities of oil seals. Some advancements include integrated metal cases for additional strength, dual-lip designs for optimized sealing, and spring-loaded elements that maintain pressure on the sealing lip, adapting to shaft misalignments.
Product integrity rests on continuous improvements and feedback loops between the field and manufacturers. The 35-72-10 oil seal, like its counterparts, benefits from a legacy of innovation, rooted in mechanical engineering insights and evolving manufacturing processes. Engineers and researchers persist in exploring new materials and seal designs that promise greater efficiency, reduced friction, and longer service life.
In conclusion, the 35-72-10 oil seal serves as a crucial element in the smooth operation of machinery across industries. Its importance cannot be overstated, involving meticulous selection, precise installation, and ongoing innovation to meet the ever-growing demands of modern engineering applications. Understanding their nuances, from material composition to application-specific adaptations, empowers engineers and maintenance professionals to achieve best-in-class results, ensuring machinery resilience and productivity.