In the world of industrial machinery, where the longevity and efficiency of components are paramount, the skeleton oil seal emerges as an indispensable element. Despite its seemingly simple structure, this small but crucial part plays a vital role in safeguarding the integrity of mechanical systems. Drawing on years of experience and deep technical knowledge, we explore why skeleton oil seals are integral to any machinery that values reliability and performance.
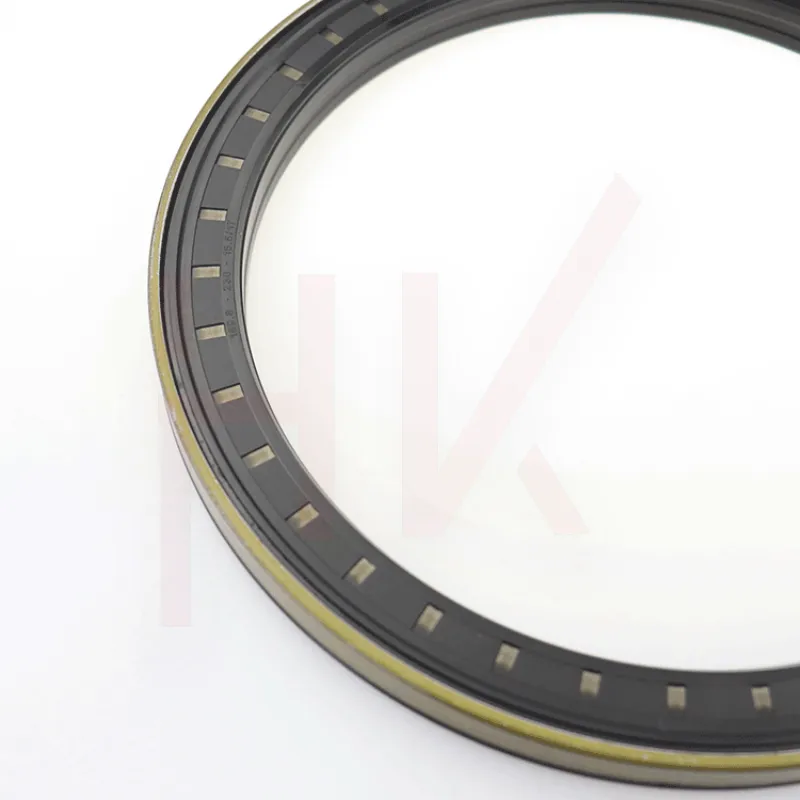
To begin with, the primary function of a skeleton oil seal is to prevent leakage of lubricants while simultaneously blocking contaminants from entering the machinery. This dual function is achieved by the precise engineering of the seal, which is meticulously crafted to fit snugly within the housing of rotating or reciprocating components. The importance of maintaining clean and consistent lubricant levels in machinery cannot be overstated. By ensuring that dirt, dust, and other particulate matter do not infiltrate the system, skeleton oil seals significantly extend the life and efficiency of the equipment.
The design and material composition of skeleton oil seals are pivotal to their performance. Typically, these seals are made from high-grade synthetic rubber or other elastomers, combining flexibility with resilience to withstand harsh operating conditions. The choice of material can greatly impact the seal's durability and functionality, especially in environments with extreme temperatures or exposure to chemicals. For instance, seals made from fluorocarbon rubber offer excellent heat resistance, making them suitable for high-temperature applications. This expertise in material science is what sets apart a basic seal from one that provides superior longevity and cost-effectiveness.
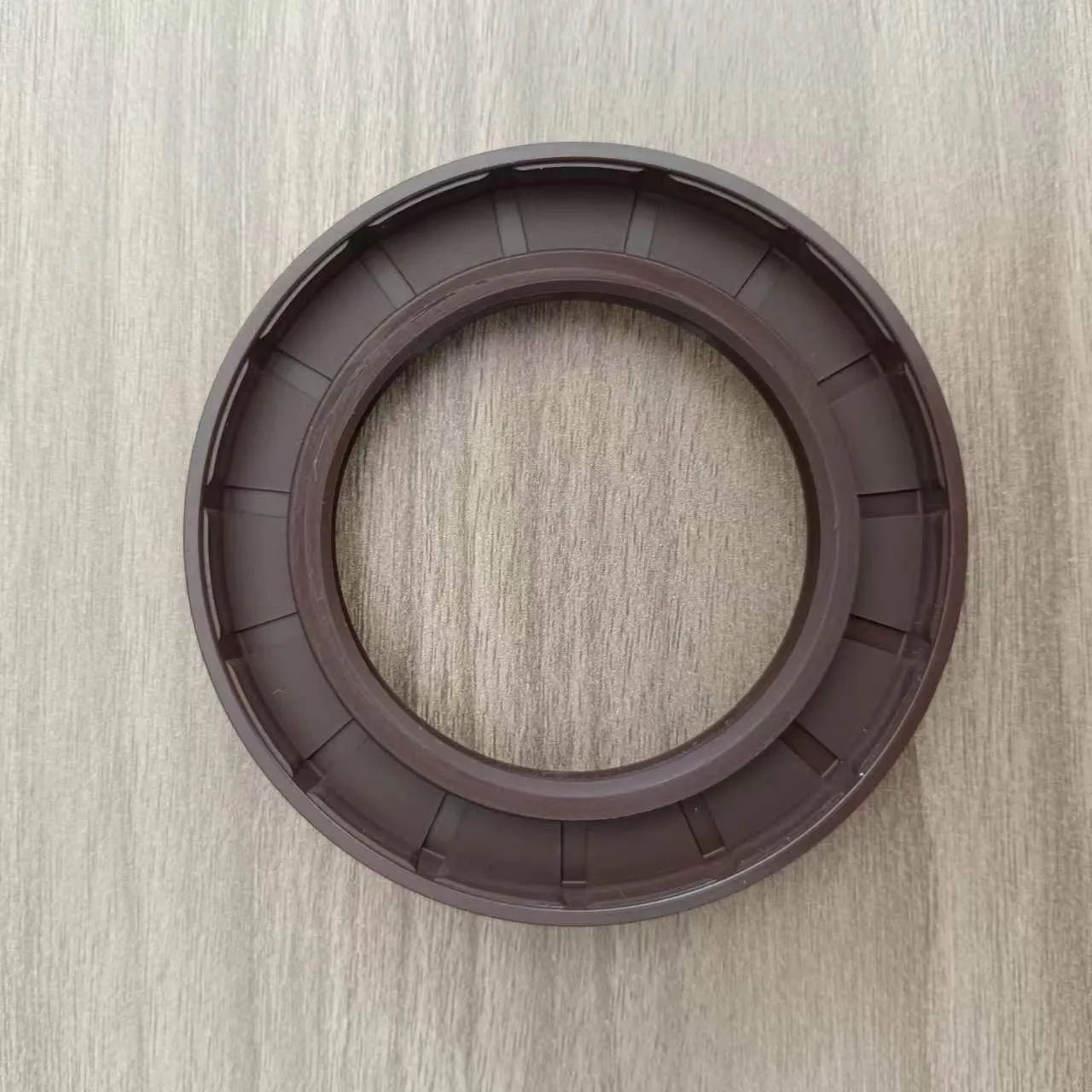
skeleton oil seal
Furthermore, a critical aspect that enhances the expertise surrounding skeleton oil seals is understanding the specific requirements of different machinery applications. For example, automotive engines, pumps, compressors, and gearboxes all demand different sealing solutions due to variations in pressure, speed, and environmental exposure. By conducting detailed analysis and customization based on the specific machinery specifications,
manufacturers can ensure optimal seal performance. This level of tailored expertise not only maximizes the machinery's performance but also ensures the trustworthiness of the manufacturer's solutions.
When selecting a skeleton oil seal, it's paramount that buyers consider not only the seal's specifications but also the reputation and authority of the manufacturer. A reputable manufacturer will not only provide high-quality products but also offer guidance and support throughout the lifecycle of the machinery. This customer-centric approach builds trust and fosters long-term relationships, which is crucial in industries where reliability and performance are non-negotiable.
In conclusion, the skeleton oil seal may be a small component, but its impact on the efficiency and durability of mechanical systems is monumental. Leveraging real-world experience, technical expertise, and a commitment to quality and reliability, these seals ensure that machinery operates smoothly and without interruption. By choosing the right seal and a trustworthy manufacturer, businesses can achieve significant savings in maintenance costs and downtime, securing their position as leaders in their respective industries.