Selecting the perfect hub rubber seal is crucial for ensuring the longevity and optimal performance of your machinery. These small, yet vital components serve as barriers against contaminants, safeguarding critical parts from wear and tear. My journey into exploring hub rubber seals began over a decade ago when a failing seal led to a costly downtime in my manufacturing unit. That incident sparked a deep dive into the intricacies of these essential components, and today, I share my expertise with you to help make informed decisions for your operations.
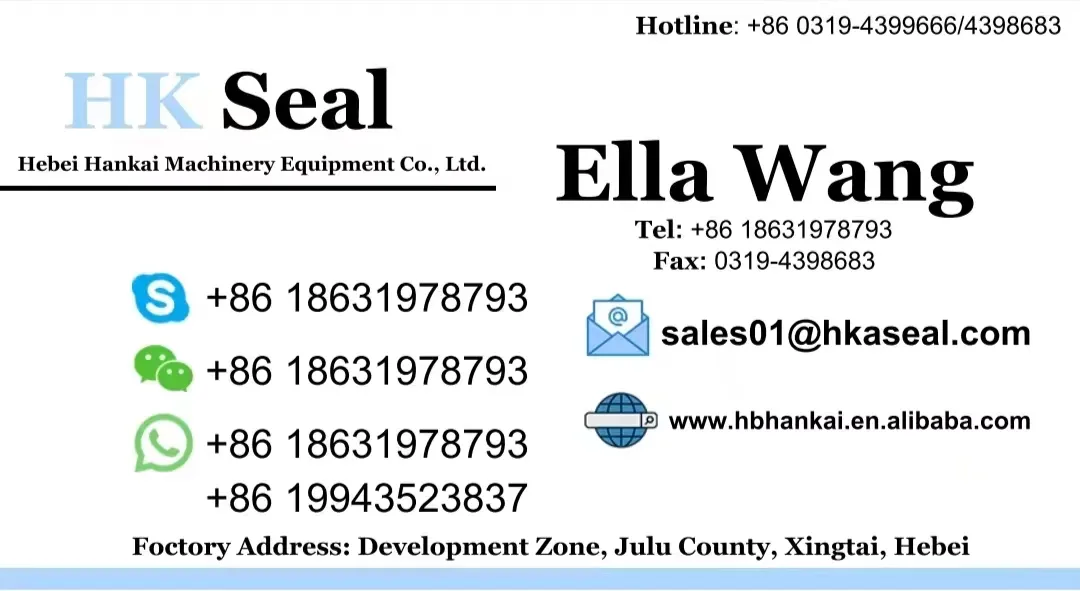
Understanding the material and design of hub rubber seals is pivotal. Most seals are composed of nitrile rubber (NBR) or silicone, each offering unique advantages. Nitrile rubber, known for its resilience against oils and heat, is a preferred choice in automotive industries. Silicone, on the other hand, boasts impressive temperature resistance, making it suitable for applications that face extreme conditions. When selecting a seal, considering the operational environment is fundamental. For example, in a setup where exposure to high temperatures is routine, a silicone-based seal might offer superior durability.
Precision in manufacturing is another cornerstone of a highly effective hub rubber seal. Look for manufacturers who uphold stringent quality control processes, ensuring that each seal meets exact specifications. This kind of attention to detail reduces the risk of failure and enhances the reliability of your machinery. Personally, engaging with manufacturers who provide transparent production processes and verifiable quality certifications has significantly reduced the instances of malfunction in my own machines.
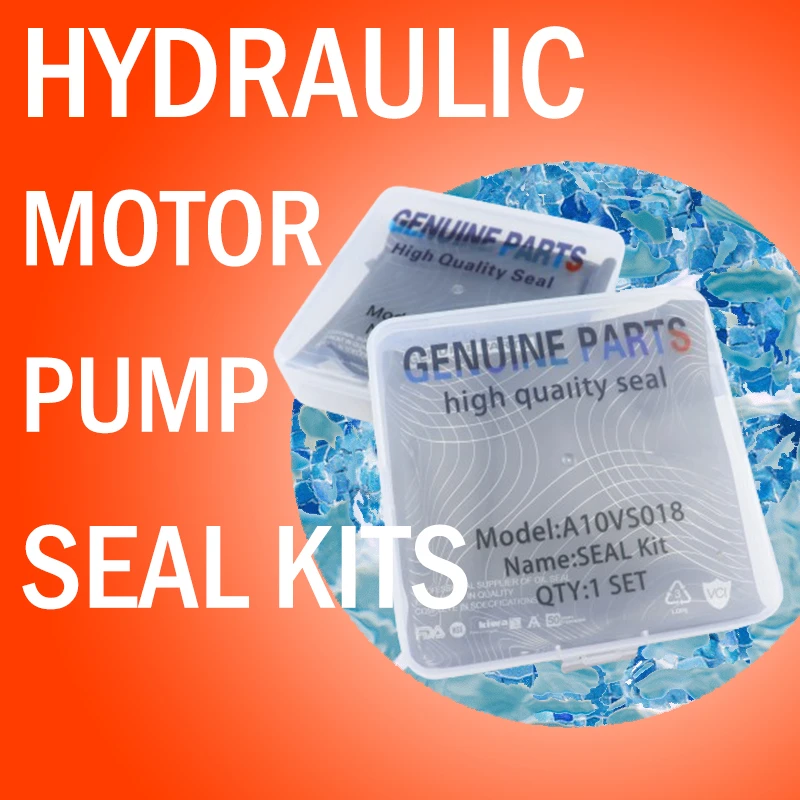
Integration of advanced technologies in seal manufacturing has also revolutionized the quality and effectiveness of hub rubber seals. Modern seals may incorporate elements like embedded sensors to monitor wear and predict maintenance needs, hence reducing unexpected downtimes. As an advocate for incorporating technological innovations, I can attest to the benefits of these advancements. They not only extend the life of the seals but also improve the overall efficiency of the machinery. Investing in these smart seals has resulted in measurable improvements in equipment reliability and productivity in my past ventures.
hub rubber seal
Installation and maintenance practices are equally crucial in maximizing the lifespan of your hub rubber seals.
Proper installation ensures optimal performance of the seals. Employing professional technicians or following detailed manufacturer guidelines can mitigate the risk of improper installation. In the early years of my career, overlooking installation intricacies led to premature seal failures. Learning from those experiences, I emphasize the importance of meticulous installation and routine maintenance checks to prevent similar pitfalls.
Trustworthy suppliers play a decisive role in ensuring that you receive authentic, high-quality hub rubber seals. Opt for established suppliers known for their transparency and commitment to quality. My policy is to foster long-term relationships with suppliers who offer not just products, but comprehensive support and advice tailored to specific requirements. This approach has cultivated a network of dependable partners who prioritize quality and client satisfaction, enhancing overall operational success.
In conclusion, the journey to selecting the right hub rubber seal lies in understanding material properties, manufacturing precision, integration of modern technologies, diligent installation, and aligning with reputable suppliers. Drawing from my extensive experience, these elements collectively ensure the optimal performance and longevity of your machinery. By prioritizing these aspects, you not only safeguard your equipment but also enhance its efficiency and productivity, ultimately leading to sustained industrial success.