Wiper seals, often overlooked yet vitally important components in industrial and mechanical systems, are crucial for ensuring the smooth operation and extended lifespan of hydraulic and pneumatic devices. Their primary role in these systems is to prevent foreign particulates, dirt, and other contaminants from entering or leaving the space within mechanical components, thereby protecting delicate machinery from potential damage.
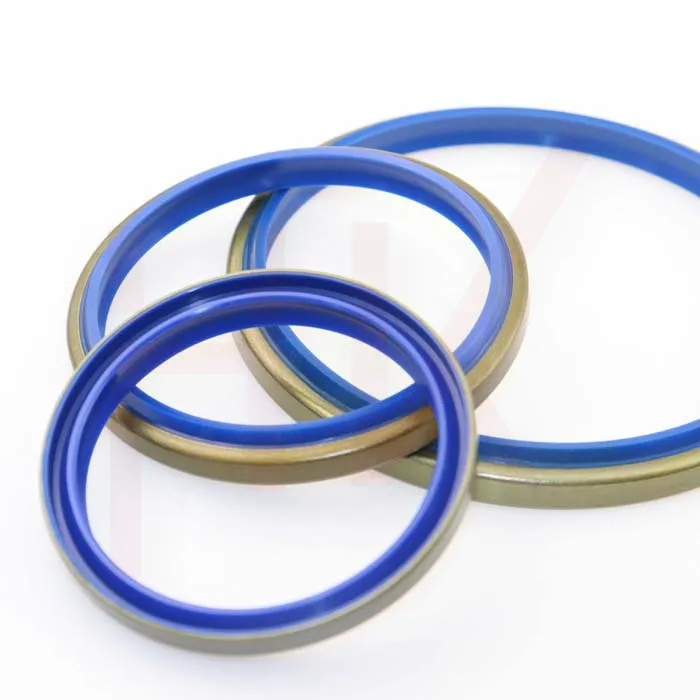
Industrial applications that utilize hydraulic cylinders, such as manufacturing equipment, agricultural machinery, and construction tools, greatly benefit from the effective use of wiper seals. The precision with which these seals perform contributes significantly to system integrity, reducing the risk of contamination that can lead to costly maintenance and downtime.
Constructed from a variety of robust materials like polyurethane, PTFE, and nitrile rubber, each wiper seal is crafted to meet specific environmental and mechanical requirements. The choice of material depends not only on the working conditions, such as temperature ranges and exposure to chemicals, but also on the specific application to ensure optimal performance and longevity. Polyurethane wiper seals, for instance, are renowned for their abrasion resistance and are ideal in environments with high wear and tear. PTFE, on the other hand, offers exemplary chemical resistance, making it suitable for applications involving exposure to aggressive substances. Nitrile rubber is praised for its flexibility and resistance to oil, often preferred in automotive and fluid power systems.
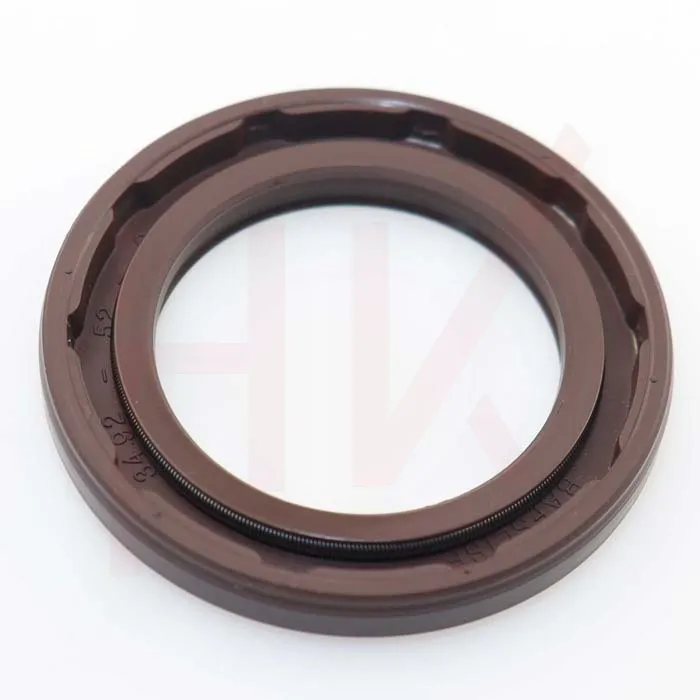
A genuine experience in the industry reveals that selecting the appropriate wiper seal extends beyond material choice. The design of the seal, whether it be an integrated or a flange type, also plays a crucial role. Integrated wiper seals, often used in applications requiring smaller installation space, offer a compact and efficient barrier against contaminants. Meanwhile, flange-type seals provide additional strength and stability, preferred in larger hydraulic systems where mechanical robustness is paramount.
wiper seal
For those in charge of maintaining industrial systems, understanding the expertise involved in wiper seal selection and maintenance is paramount.
Regular inspections are advised to assess the seal's condition, ensuring that they remain intact and effective. Signs of wear, such as cracks or abrasions on the seal, should be addressed immediately to prevent machinery failure. This preventive approach not only prolongs the equipment's lifespan but also optimizes its operational efficiency.
Authority in the field of hydraulic and pneumatic sealing is often held by those manufacturers and suppliers who prioritize precision engineering and rigorous testing of their products. Companies that produce and supply wiper seals invest heavily in research and development to advance seal technology, ensuring their products meet the ever-evolving demands of industrial environments. Such dedication to quality and innovation instills confidence in their reliability and effectiveness.
Trustworthiness in the wiper seal market is built through proven performance and customer satisfaction. When selecting a supplier, it is imperative to consider those who provide comprehensive support and consultation, guiding clients in making informed decisions tailored to their unique operational needs. Suppliers who offer detailed technical data, performance metrics, and compatibility guidelines enhance trust and ensure that customers are equipped with the necessary information to maximize their machinery's potential.
The indispensable nature of wiper seals in protecting and preserving mechanical systems cannot be overstated. Their contribution to the efficiency and reliability of equipment showcases the importance of employing high-quality seals tailored to the specific demands of each application. A poised understanding and carefully considered application of wiper seals ultimately serve as the foundation for successful and uninterrupted industrial operations.