Selecting the right wiper rod seal is critical to ensuring the longevity and efficiency of hydraulic and pneumatic systems. This seemingly small component plays a crucial role in protecting systems from various environmental factors and internal leakages. As someone with considerable expertise in system maintenance and parts optimization, I have gathered insights and deep understanding from years of hands-on experience and would like to share this comprehensive overview.
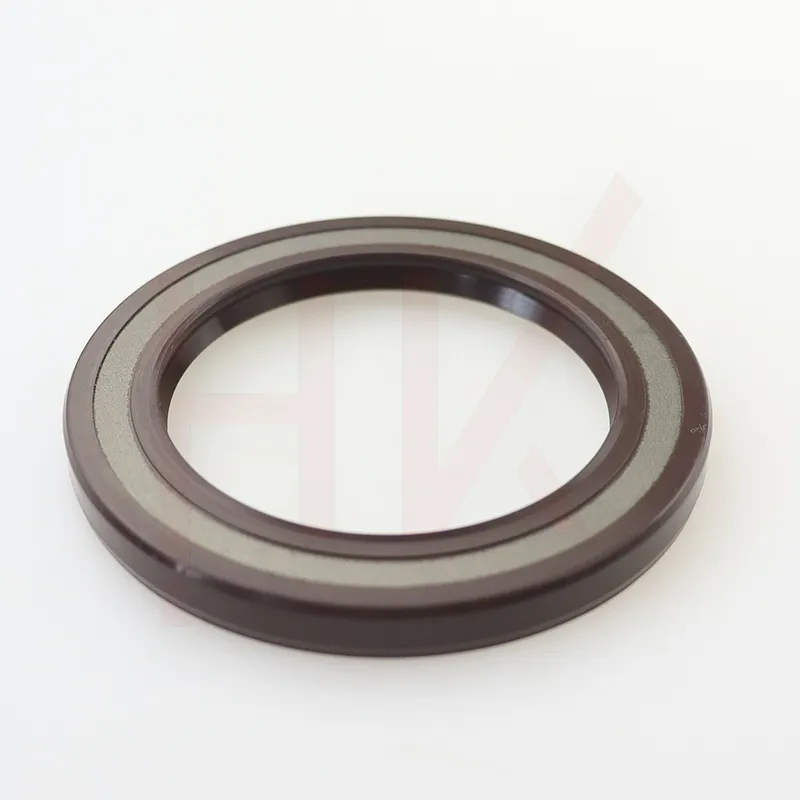
Wiper rod seals are pivotal in preventing external contaminants like dirt, dust, and water from entering the hydraulic system. They effectively 'wipe' the rod as it retracts into the cylinder, ensuring that no particle disrupts the system's smooth operation. This functionality is key in industries where machinery is constantly exposed to harsh environmental conditions, such as construction, agriculture, and mining.
From an expertise standpoint, choosing the right material for a wiper rod seal is paramount. The seals are typically made from materials like polyurethane, nitrile rubber, and fluorocarbon. Each material has unique properties, making it suitable for different working conditions. Polyurethane, known for its excellent abrasion resistance and energy absorption, is ideal for high-pressure environments. On the other hand, nitrile rubber offers excellent versatility and is perfect for applications involving oil and fuel exposure. Fluorocarbon, widely recognized for its high-temperature resistance and compatibility with chemical exposure, suits severe conditions found in chemical plants and high-temperature equipment.
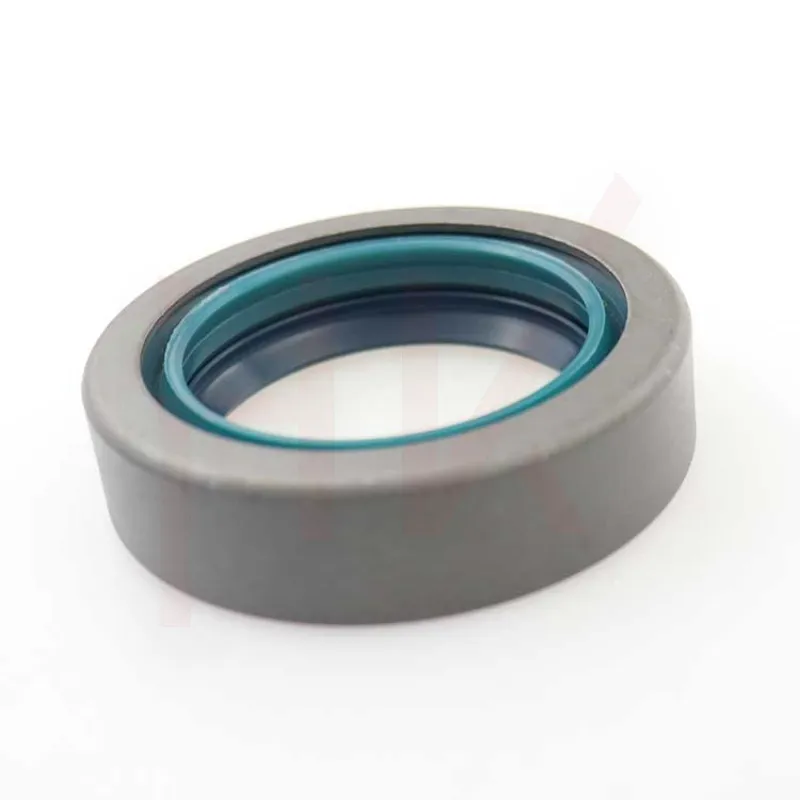
Authoritativeness comes from understanding not just the materials, but also the design aspects of wiper rod seals. The wide range of designs includes single-lip, double-lip, and custom configurations. Single-lip seals are the most common and provide a basic level of protection against contaminants. Double-lip designs offer enhanced protection, with one lip preventing external elements from entering and the other acting as an additional barrier to control internal fluid leakage. Custom seals can be engineered to meet specific operational requirements, providing tailored solutions for unique system designs.
wiper rod seal
The installation and maintenance of wiper rod seals heavily influence operational reliability and trustworthiness of mechanical systems.
Proper installation is crucial, as incorrect fitting can lead to premature wear and system failure. Regular maintenance checks ensure that seals remain in optimal condition, preventing any unplanned downtime due to seal failure. This has a direct impact on system efficiency, productivity, and cost-efficiency in the long run.
Wiper rod seals’ trustworthiness lies in their ability to extend the life of expensive machinery by safeguarding critical components. The selection process should involve a thorough consideration of the operational environment, pressure levels, temperature variations, and exposure to potentially harmful substances. Consulting with experts or manufacturers can provide valuable guidance in choosing the right seal for your specific application.
In conclusion, understanding the intricacies of wiper rod seals is essential for anyone looking to enhance the performance and durability of their hydraulic or pneumatic systems. By focusing on the right material and design, and ensuring proper installation and maintenance, these small components can make a significant impact on the efficiency and reliability of industrial machinery. This real-world experience and in-depth knowledge form the foundation of effective system optimization, offering unmatched expertise and trustworthiness in a competitive landscape.