Understanding the essential function of an oil seal is paramount for anyone engaged in the maintenance and operation of mechanical systems. Oil seals, often known as rotary shaft seals, are integral components that protect machinery by preventing the leakage of lubricants, while simultaneously keeping out harmful contaminants. Their role is pivotal across a myriad of industries, reinforcing their prominence in mechanical engineering and machinery maintenance.
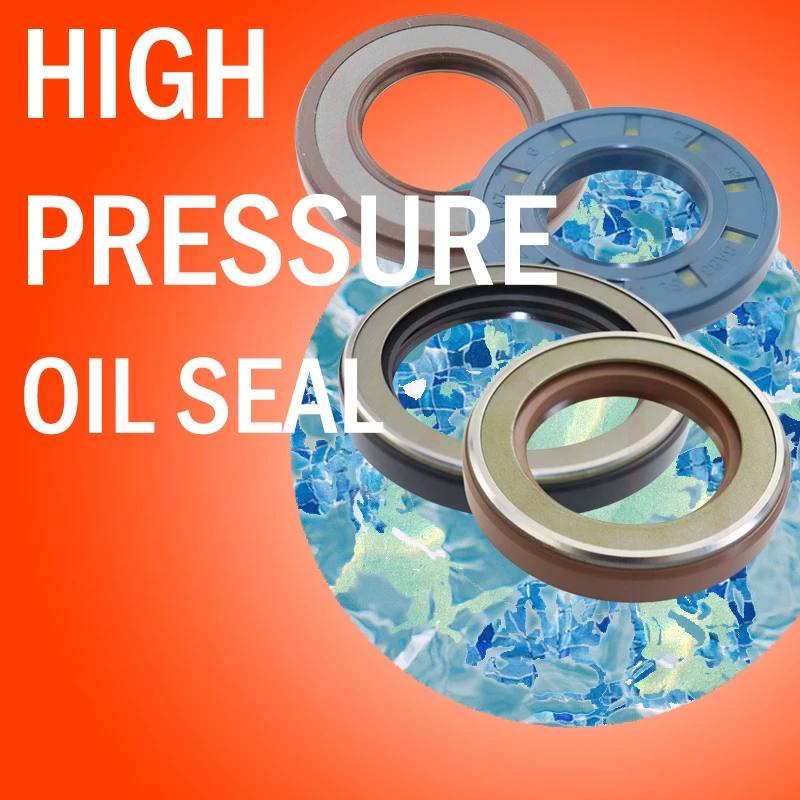
In essence, oil seals fulfill a dual purpose. Firstly, they provide a barrier to prevent lubricant from leaking along the rotating shaft, which is crucial in ensuring that machines operate smoothly and efficiently. Lubricants are vital for reducing friction between moving parts, and their retention within the system is crucial for minimizing wear and tear, enhancing the longevity of machinery. Secondly, oil seals are designed to block the entry of contaminants like dust, dirt, and moisture from entering the mechanical system. Such foreign materials can adversely affect the performance of machinery, cause corrosion, or lead to system failure.
The design and materials used in oil seals are key to their effectiveness. Typically, these seals are crafted from robust materials such as rubber, elastomers, or silicone. These materials are selected for their flexibility, resilience to temperature fluctuations, and compatibility with oils and greases. In high-performance contexts, such as automotive or aerospace industries, advanced materials like polytetrafluoroethylene (PTFE) or fluoroelastomers are utilized to withstand extreme conditions.
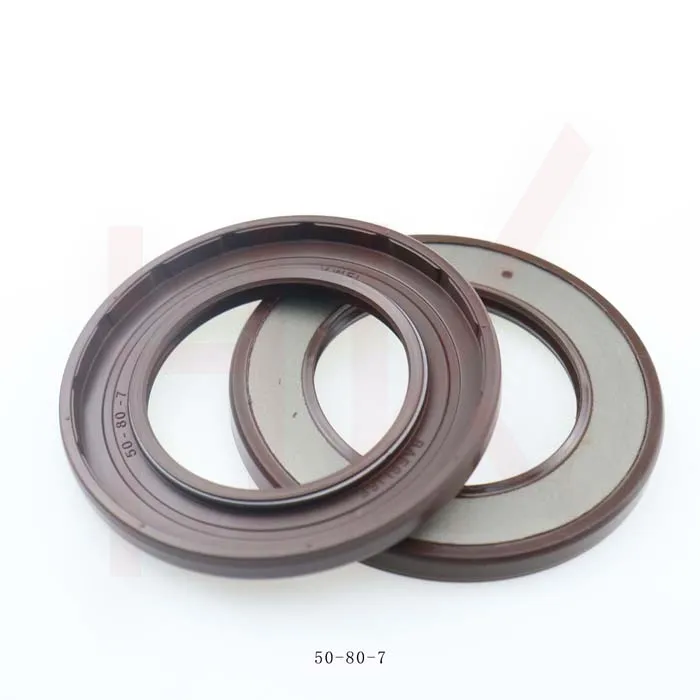
From an experiential standpoint, selecting the right oil seal involves a comprehensive understanding of the operating environment and specific machinery requirements. For those in the field, one must consider factors such as shaft speed, temperature, pressure, and the type of lubricant in use. Each of these factors can significantly influence the performance and durability of an oil seal.
Expertise in installing oil seals also cannot be overstated. Proper installation is a critical factor in ensuring the seal's effectiveness. Misalignment during installation or the use of incorrect tools can result in premature failure of the seal, leading to potential machinery damage or downtime. Technicians trained in the precise fitting of these components contribute fundamentally to the smooth operation of sophisticated mechanical systems.
what is the purpose of oil seal
Authoritativeness in the discussion about oil seals is bolstered by referencing industry standards and guidelines that dictate their design and application. For instance, standards from the International Organization for Standardization (ISO) and the Society of Automotive Engineers (SAE) provide comprehensive insights into the parameters governing the selection and application of oil seals. These standards ensure that oil seals meet stringent performance and safety criteria, ultimately safeguarding machinery operations.
The trustworthiness of oil seals, and by extension, a system's reliability, is corroborated by rigorous testing and quality assurance processes undertaken by manufacturers. Brands renowned for their quality in the production of oil seals, such as SKF, Garlock, and NOK, are trusted names in the industry. Their products undergo exhaustive testing to ensure that they perform consistently under varied operating conditions.
For individuals and companies invested in ensuring optimal performance of machinery, fostering an understanding of oil seals is indispensable. Opting for quality seals from reputable manufacturers, adhering to installation guidelines, and remaining informed about environmental factors all contribute to prolonging the service life of machinery. Through such meticulous attention to detail, one can significantly reduce maintenance costs and enhance operational efficiency.
In summary,
the purpose of an oil seal extends beyond mere containment of lubricants. It acts as a critical protector of machinery, ensuring optimal performance by barring contaminants and retaining essential lubricants. Mastery over their selection, installation, and maintenance is essential for anyone committed to upholding the reliability and efficacy of mechanical systems. For those in the pursuit of expertise in machining and engineering, oil seals offer insights into the intricate dance between components that keeps the world's machinery humming in perfect harmony.