Oil seals, also known as rotary shaft seals, play a crucial role in maintaining the efficiency and longevity of machinery and automotive systems. Their primary purpose is to secure the interfacing surfaces between stationary and moving components, preventing leaks of lubricants and contamination by dirt, dust, or moisture. The oil seal’s significance is evident across various industries, from automotive and aerospace to manufacturing and industrial equipment, and understanding its purpose is pivotal for ensuring optimal operation and maintenance of equipment.
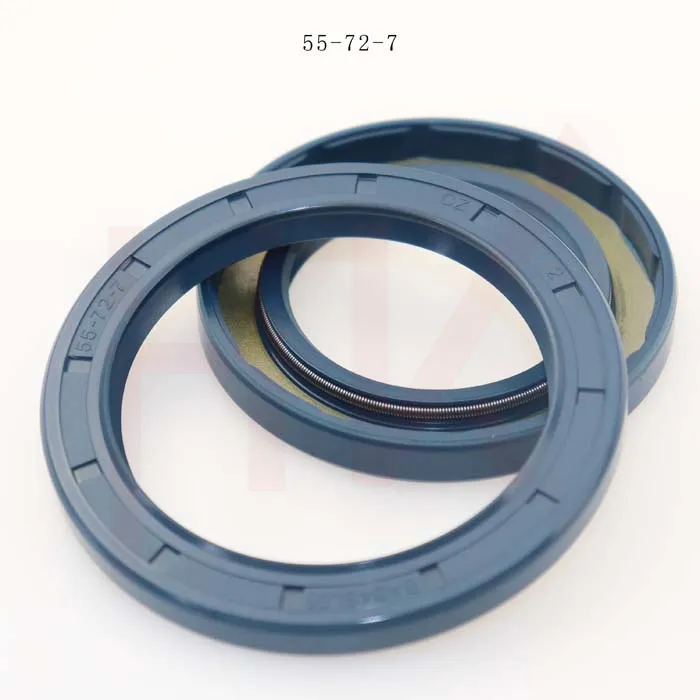
The quintessential task of an oil seal is to retain lubricants within the machine compartments. The efficient functioning of any mechanical system highly depends on the presence of lubrication within its components, such as bearings and shafts. By mitigating the risk of oil leaks, oil seals ensure that the lubrication environment remains effective, which reduces friction and wear and tear on moving parts. This contribution is particularly vital in high-speed applications where the efficiency of the lubricant can dramatically impact performance and the longevity of components.
Beyond retaining lubricants, oil seals serve the equally important function of preventing external contaminants from entering the machinery systems. Dust, dirt, and moisture can severely impair the functioning of machinery by corroding or rusting components, thus leading to breakdowns or reduced efficiency if allowed to infiltrate the system. By forming a tight barrier at the interface of moving parts, oil seals effectively shield sensitive components from negative environmental factors, ensuring continued production reliability and minimizing downtimes due to maintenance or repairs.
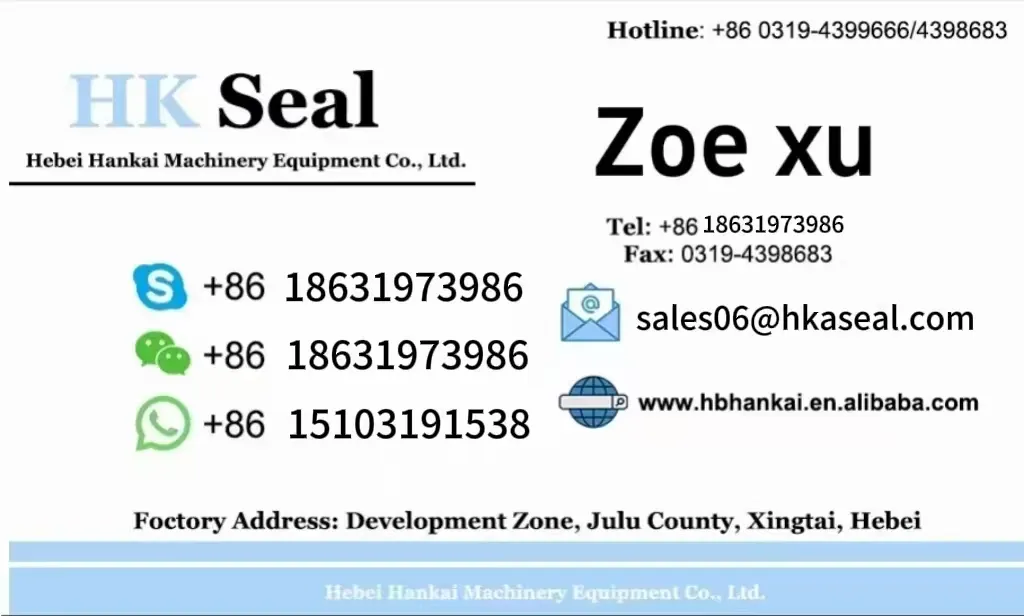
Expertise in the selection and application of oil seals lies in understanding the various materials and designs available, each tailored to meet the specific needs of different operating environments. Modern oil seals are typically crafted from materials such as nitrile rubber, silicone, or fluorocarbon elastomers, each possessing distinct attributes that make them suitable for various temperature ranges, exposure to chemicals, and environmental conditions. Engineers and maintenance professionals must possess the skill to select the right oil seal material compatible with the operating conditions and exposure factors of their specific application.
In applications subject to extreme conditions, such as high-pressure environments or applications involving aggressive chemicals, specialized oil seal designs such as double-lipped seals or seals with protective coatings are employed to offer enhanced protection and longevity. The expertise in determining the appropriate seal type extends beyond mere selection. It also includes considerations for installation techniques that ensure proper alignment and seating of the seal, preventing premature failures or leakage due to installation errors.
what is the purpose of oil seal
The expertise in oil seals also extends to their role in energy efficiency. By maintaining a tightly sealed environment, these components reduce energy loss that could occur through increased friction or resistance. In industries where energy efficiency translates to financial savings, the role of a well-maintained oil seal becomes economically significant. Optimizing seal performance can lead to cost savings not only through prolonged machinery life but also by diminishing energy consumption.
To establish authoritativeness and trustworthiness, professional organizations and bodies oversee standards for manufacturing and testing oil seals. Products that meet these standards, such as those set by the International Organization for Standardization (ISO) or the Society of Automotive Engineers (SAE), assure users of their reliability and performance capabilities. End users often rely on seals that carry certification from these regulatory bodies, trusting that they comply with stringent safety and performance benchmarks.
Additionally, advancements in oil seal technology are aligned with the principles of sustainable development. As industries seek to lower their carbon footprint, the development and application of eco-friendly seal materials and designs have gained traction. By investing in oil seal products that adhere to green principles without compromising performance, industries stay at the forefront of corporate responsibility and environmental stewardship.
In conclusion, the purpose of an oil seal in various industrial applications is multifaceted, encompassing the retention of lubricants, prevention of contamination, enhancement of energy efficiency, and adherence to safety and environmental standards. Mastery in the selection and application of oil seals requires a profound understanding of materials, designs, and standards to ensure optimal device performance and sustainability, positioning the oil seal as a pivotal component in mechanical engineering and industrial maintenance.