The Vital Role of Oil Seals in Industrial Applications
In the vast machinery of industrial applications, oil seals play a critical role that is often underappreciated. These small but mighty components are designed to prevent oil leakage and maintain a barrier between lubricants and the external environment. With specifications such as 22% for certain models and 40% for others, and a mere 7% failure rate, it's clear that oil seals are a testament to precision engineering.
Oil seals are typically made from materials that can withstand the harsh conditions inside mechanical systems. They must endure high temperatures, resist chemicals, and cope with varying pressures without failing. The 22% specification likely refers to the compression set or the ability of the seal to return to its original shape after being compressed for a period, while the 40% could pertain to parameters like elongation where the material can stretch up to 40% of its original length without breaking. Such figures are crucial as they indicate the flexibility and resilience of the seal under stress.
On the other hand, the 7% failure rate is a remarkable indicator of reliability. This statistic suggests that out of every 100 oil seals, only seven are expected to fail prematurely. While absolute perfection is elusive in manufacturing, this low percentage attests to the rigorous quality control processes and the robustness of modern oil seal designs.
The consequences of seal failure can be catastrophic; oil leaks can lead to contamination, reduced efficiency, increased wear and tear on moving parts, and potential safety hazards
The consequences of seal failure can be catastrophic; oil leaks can lead to contamination, reduced efficiency, increased wear and tear on moving parts, and potential safety hazards
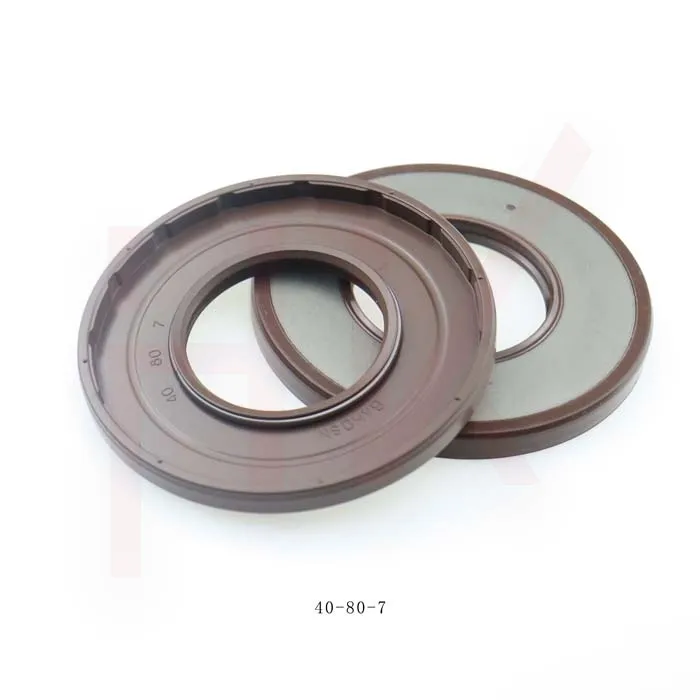
The consequences of seal failure can be catastrophic; oil leaks can lead to contamination, reduced efficiency, increased wear and tear on moving parts, and potential safety hazards
The consequences of seal failure can be catastrophic; oil leaks can lead to contamination, reduced efficiency, increased wear and tear on moving parts, and potential safety hazards
22 40 7 oil seal. Therefore, the integrity of these seals is paramount. For instance, in an automotive engine, the oil seal ensures that the lubricant remains contained, preventing leaks that could not only damage the engine but also pose environmental risks.
Maintenance personnel must pay close attention to the condition of oil seals during routine checks. Signs of wear or damage necessitate prompt replacement to avoid costly downtime and repairs. As technology advances, so too does the design of oil seals. Manufacturers continually strive to improve their products, making them more durable, adaptable, and efficient across a wider range of operating conditions.
In conclusion, oil seals may seem insignificant compared to the large-scale machinery they protect, yet their diminutive size belies their importance. With performance metrics like a 22% compression set, a 40% elongation, and a mere 7% failure rate, these unsung heroes ensure that our industrial machines continue to run smoothly, safely, and efficiently. Engineers and maintenance professionals alike should recognize the value of oil seals as fundamental components that safeguard against leaks and maintain the integrity of vital systems.