Understanding Hydraulic Lip Seals A Comprehensive Guide
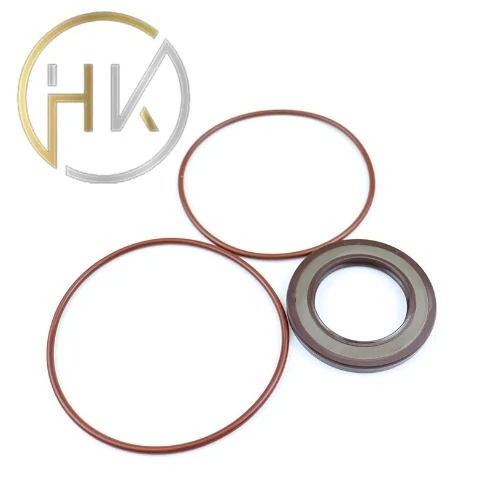
Hydraulic lip seals are a crucial component in various industrial applications, designed to ensure the integrity and efficiency of hydraulic systems. Their primary function is to prevent fluid leakage between the different mechanical parts, thus maintaining pressure and enhancing the mechanical performance of the entire system.
Experience with hydraulic lip seals reveals their indispensable role in industries ranging from automotive to aerospace. These seals are engineered to withstand extreme pressures and temperatures, providing reliable service in challenging environments. One notable real-world application is their use in heavy machinery,
where maintaining hydraulic fluid integrity is essential for operational efficiency.
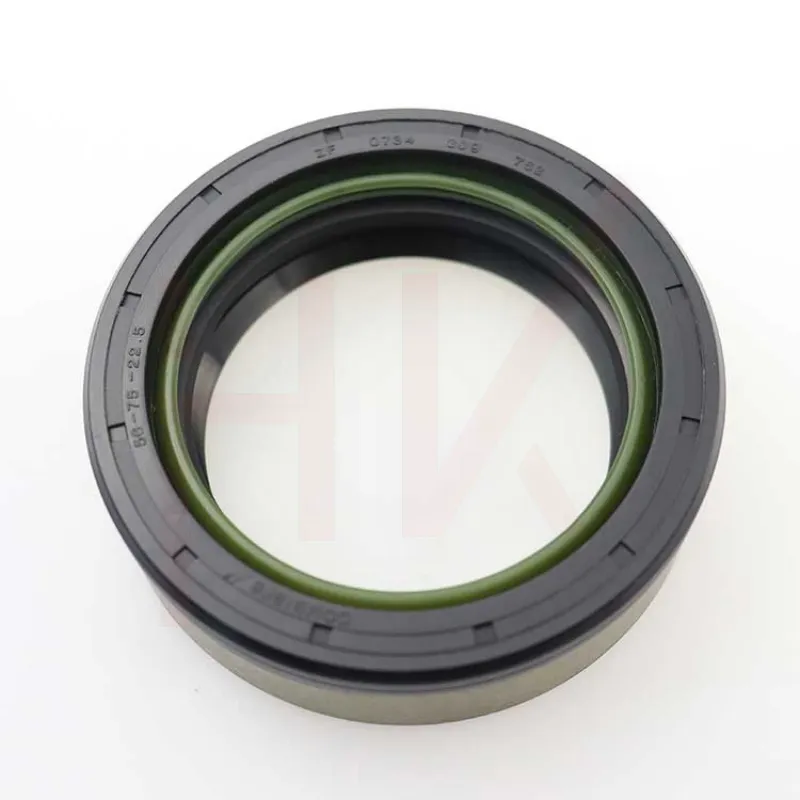
The design of hydraulic lip seals involves meticulous attention to detail, focusing on material composition and structural design to cater to specific operational needs. Experts emphasize the importance of selecting the right seal material, such as nitrile or fluorocarbon, depending on the fluid type and system temperature. Each material offers unique properties—nitrile is known for its vibration damping ability, while fluorocarbon is ideal for high-temperature applications.
In addition, hydraulic lip seals must be crafted with precision to ensure that they fit perfectly within the hardware. This precision manufacturing plays a significant role in the seal's longevity, preventing premature wear and failure. Professional engineers and manufacturers continuously innovate seal designs to combat friction and wear, which are common challenges faced by users.
hydraulic lip seal
The authority of hydraulic lip seal manufacturers is established through rigorous testing and quality control. These seals are subjected to various standards to ensure they meet industry requirements, such as ISO and ASTM guidelines. Trust is built through consistent performance, reliability in sealing, and the ability to handle dynamic pressures, which are validated by third-party testing and certification.
Trustworthiness in hydraulic lip seals is further reinforced by detailed end-user feedback. Field operators and maintenance personnel provide valuable insights into seal performance, with real-life case studies often highlighting the seals’ durability and effectiveness in arduous settings. This experiential feedback, combined with scientific expertise, supports the continuous improvement of hydraulic lip seals.
It is critical for users and purchasers of hydraulic lip seals to consider the installation process and ongoing maintenance. Proper installation is paramount to avoid operational failures. Experts recommend following manufacturer guidelines closely, using the correct tools, and employing skilled technicians for installation. Routine inspections and maintenance checks further ensure long-term reliability, minimizing downtime and costs associated with seal failure.
In conclusion, the significance of hydraulic lip seals in maintaining system efficiency and reliability cannot be overstated. Their design, material selection, and manufacturing process are grounded in expert knowledge and stringent testing, providing a trustworthy solution for various high-pressure applications. Users who value performance and longevity should not underestimate the role of these seals and must prioritize quality when selecting hydraulic components. By doing so, industries can enjoy the benefits of heightened equipment efficiency and reduced maintenance costs, fostering sustainable and profitable operations.