Skeleton oil seals are a crucial component in numerous industrial applications, offering an essential barrier that prevents fluid leakage while safeguarding the inner mechanisms of machines. As an integral part of any machinery that relies on lubricants for smooth operation, understanding their function and proper implementation is vital for engineers, technicians, and maintenance professionals. Drawing from years of experience in the field, this article explores the nuances of skeleton oil seals, discusses their benefits, and provides insights into their installation and maintenance, ensuring optimal performance and longevity.
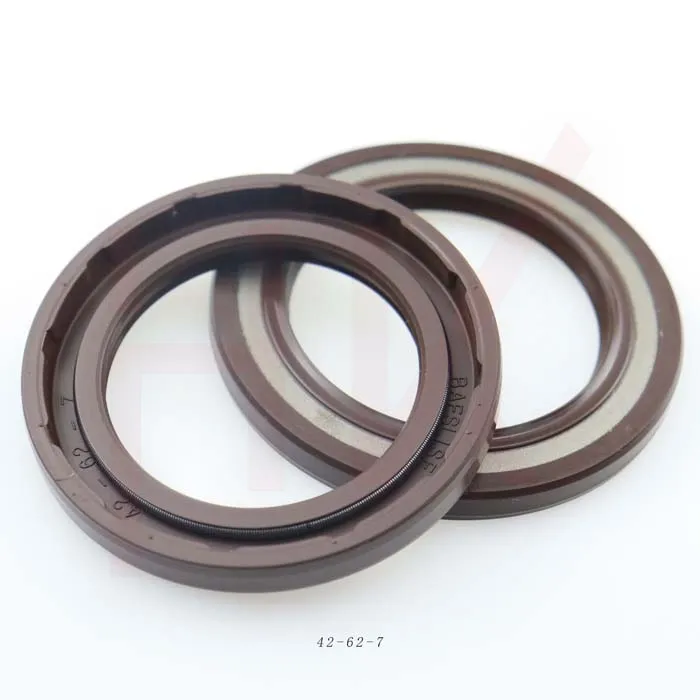
The fundamental purpose of skeleton oil seals is to retain lubrication oils within the machinery, preventing contaminants from entering and causing potential damage. These seals are designed in a way that allows them to withstand harsh operating conditions, including high temperatures and abrasive substances. A deep dive into my professional encounters reveals that choosing the appropriate material for skeleton oil seals is pivotal. Materials such as nitrile rubber (NBR), fluorocarbon (FKM), and silicone rubber are popular due to their resilience and adaptability to different industrial environments.
Skeleton oil seals come in several designs, each tailored to specific applications. A common variation is the single-lip seal, which is efficient in general applications where pressure is moderate. However, for scenarios with elevated pressure or where enhanced sealing is required, a double-lip seal proves advantageous. In many cases, I have recommended double-lip seals for automotive industries due to their capability to handle variations in pressure levels efficiently, thus ensuring uninterrupted performance and extending the life of the machinery.
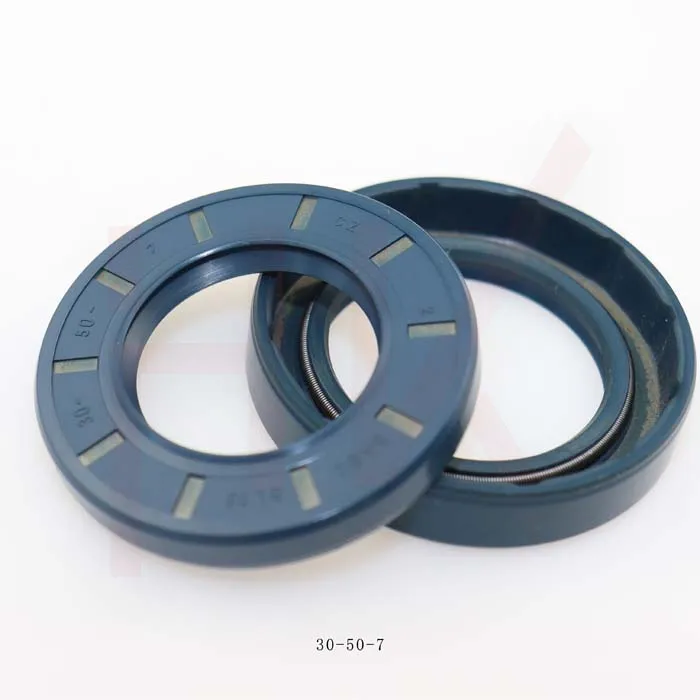
The installation of skeleton oil seals requires precision and an understanding of the operational environment. From my expertise, a correctly installed oil seal can significantly reduce the chances of failure.
Here are key steps to consider during installation
1. Inspection and Preparation Before installation, inspect the shaft and housing for any surface imperfections, as even minor nicks can compromise the seal's effectiveness. Cleanliness is paramount; any dirt or debris can erode the seal over time.
2. Proper Tooling Use the right toolkit to avoid damage during installation. Employ mandrels and press tools specifically designed for establishing seals to ensure that they are placed evenly and with the correct pressure.
skeleton oil seal
3. Lubrication Applying a thin film of lubricant to the seal and the shaft facilitates smoother installation and reduces the initial friction, which can lead to premature wear.
4. Alignment Accurate alignment is crucial. Any misalignment can cause an uneven wear pattern, eventually leading to failure. Using a dial gauge can help in ensuring that the shaft and seal are perfectly aligned.
Despite the high durability of skeleton oil seals, regular maintenance is essential to uphold their performance. Periodic inspections are necessary to check for signs of wear or damage. Replace seals that exhibit hardening, cracking, or excessive wear immediately to prevent potential leakage and machinery downtime. It's also recommended to keep a log of the seals' condition and any replacements made, which can serve as valuable data for understanding usage patterns and predicting future needs.
Moreover, in cases where machinery operates in extreme conditions, such as high temperatures or abrasive environments, consider upgrading to oil seals made from materials with higher temperature resistance and greater wear resilience. Engaging with manufacturers to customize seals for specific applications can lead to considerable improvements in efficiency and service life.
In conclusion, the role of skeleton oil seals in enhancing the productivity and reliability of machinery cannot be overstated. By leveraging my expertise, I stress the importance of selecting the right material and design, ensuring precise installation, and committing to regular maintenance. These practices not only extend the life of the oil seals but also reinforce the trustworthiness and dependability of the machinery they serve. Embracing these insights can significantly boost operational efficiency and minimize unscheduled downtime, affirming the importance of skeleton oil seals as indispensable components in industrial operations.