In the world of industrial machinery and automotive engineering, the skeleton oil seal stands as a critical component ensuring efficiency and longevity. These seals, often understated in their appearance, play a pivotal role in safeguarding mechanical systems from contaminants while maintaining the necessary lubrication. Their significance extends across various sectors, from automotive to heavy machinery, making their design and function critical to system reliability.
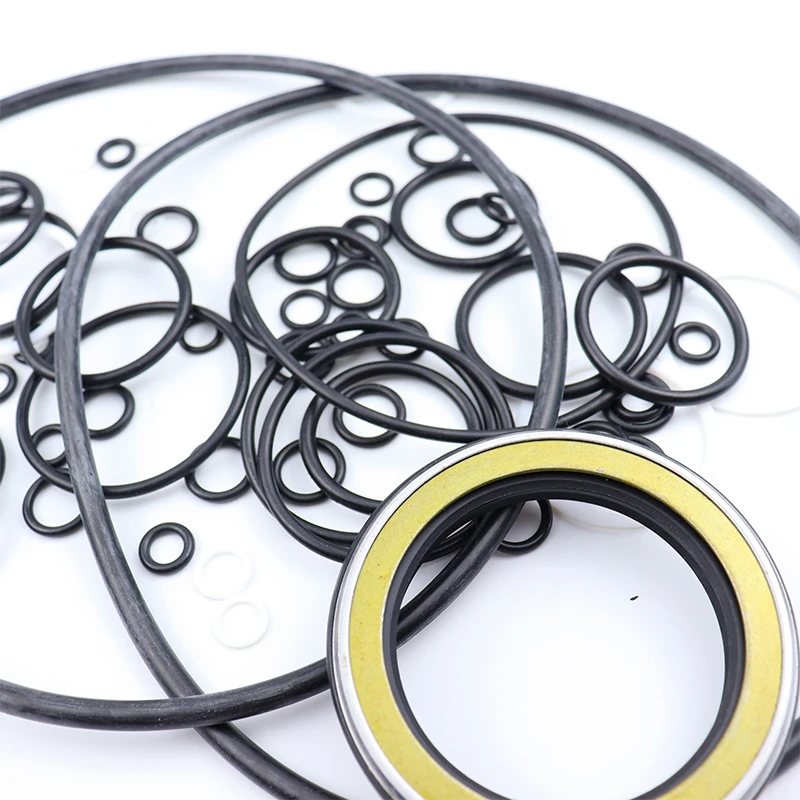
A skeleton oil seal is essentially a ring made of a flexible rubber material with an embedded metal skeleton for rigidity. Its primary function is to seal the spaces between stationary and moving components of machinery, preventing the escape of lubricants and the entry of harmful contaminants. This sealing capability not only enhances the efficiency of machinery by reducing friction but also prolongs the lifespan of the components.
When selecting a skeleton oil seal, understanding its material composition is key. Typically, the outer layer is crafted from a durable elastomer which must withstand the specific operational conditions such as temperature range, rotational speed, and the type of fluid it will be in contact with. The embedded metal skeleton provides structural support, which is crucial for maintaining the shape and effectiveness of the seal under pressure. This dual-material composition offers both flexibility and strength, a necessary combination for enduring various mechanical stresses.
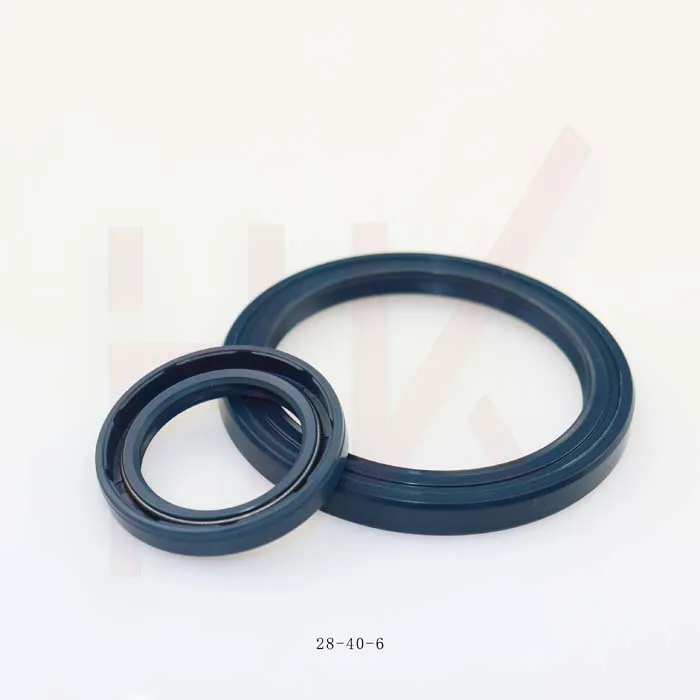
The importance of skeleton oil seals is evident in their wide application across multiple industries. In automotive applications, for example, these seals are vital in engines and powertrains where they help maintain oil circulation while keeping dirt and moisture out. This is crucial for maintaining optimal engine performance and efficiency. In industrial machinery, skeleton oil seals prevent the ingress of dust and other particulates that could interfere with machine operations, thus ensuring uninterrupted productivity and reducing maintenance costs.
skeleton oil seal
Installation of an appropriate skeleton oil seal requires expert knowledge to ensure its longevity and effectiveness. Misalignment during installation can lead to premature failure, resulting in costly repairs and downtime. Therefore, having technical expertise in both selecting the right seal for the application and installing it correctly is paramount. Regular inspection and maintenance can also extend the service life of these seals, ensuring continuous protection of the machinery.
For manufacturers and repair specialists, the choice of skeleton oil seal should align with both the functional requirements of the machinery and the economic considerations. Opting for seals from reputable suppliers with a proven track record of quality is advisable. These suppliers can often provide technical support and guidance, adding an extra layer of trustworthiness to the purchasing decision.
In conclusion, skeleton oil seals, though often overlooked, are fundamental to maintaining operational integrity and efficiency in various mechanical systems.
Their role in preventing leakage and contamination cannot be overstated. As machinery and automotive technologies advance, the demand for high-quality, reliable skeleton oil seals will continue to grow, making them an indispensable element of modern mechanical engineering. When choosing these critical components, prioritizing expertise, authority, and trustworthiness will ensure that the machinery operates smoothly and efficiently, minimizing downtime and enhancing productivity.