Seal kits for pumps serve as essential components in the maintenance and efficiency of various pumping systems. They are specifically designed assemblies of sealing elements that prevent leaks and ensure the operational smoothness of pumps in numerous industries. The failure of seals can lead to substantial machinery downtime, financial losses, and even safety hazards. Therefore, understanding the intricacies of seal kits and their proper usage becomes crucial for anyone responsible for the upkeep of pump systems.
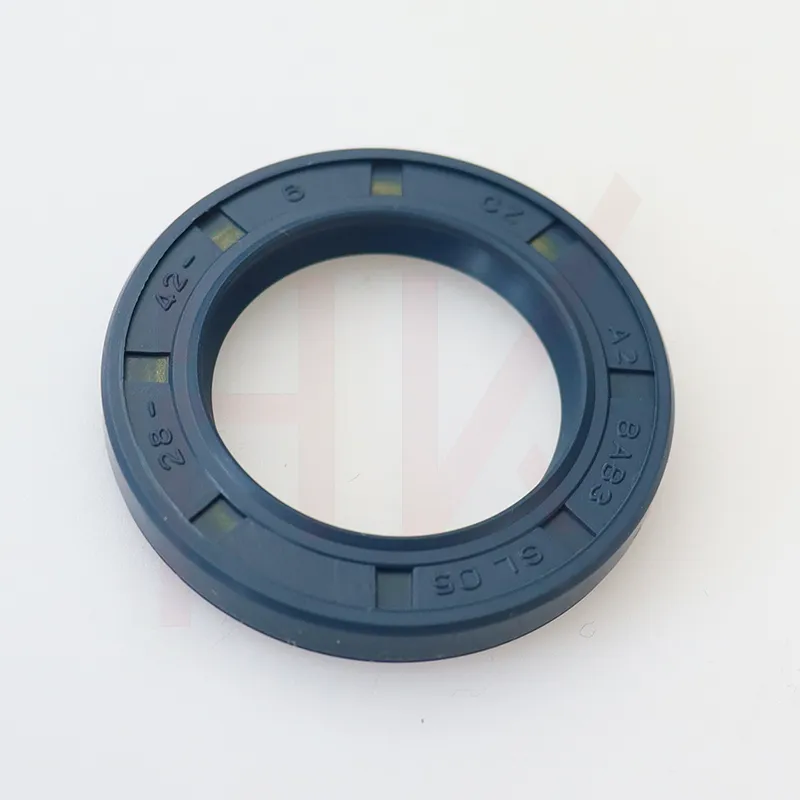
Expertise in seal kits for pumps begins with recognizing their composition and function. A typical seal kit might include o-rings, gaskets, and other sealing components tailored to fit a specific pump model. These kits are manufactured to endure high pressures and extreme temperatures while resisting corrosion and wear. The choice of materials is vital; for example, seals can be made from nitrile rubber for oil resistance, Viton for chemical resilience, or PTFE for its non-reactive properties. Experts recommend selecting a seal kit based on the pump's operating environment and the nature of the fluids being handled.
Experience in selecting and using seal kits can significantly extend the life of a pump. Regular inspections to assess the condition of seals can preempt failures. When users notice signs like unusual noises, drops in pressure, or visible leaks, this can be indicative of seal deterioration. Replacing seals before they reach a critical point is a proactive approach that saves time and money. Although it might seem straightforward to simply replace a damaged seal, ensuring compatibility with the pump specifications is essential. Mismatched seals can exacerbate wear and may void equipment warranties.
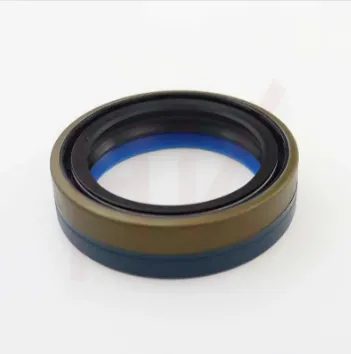
For a seal kit to be effective, authoritative guidelines suggest adhering strictly to installation manuals provided by the pump and seal manufacturers. As pumps vary between industries—from agriculture to petrochemicals—customization of seal kits might be necessary. Consulting with industry professionals or trained technicians who have specialized knowledge of both pumps and seals is advisable. These experts can offer insights into modifications that might be required to optimize performance under specific conditions.
seal kit for pump
Trustworthiness in sources of seal kits is another critical factor. Preferably, seal kits should be sourced from reputable manufacturers known for strict quality control and adherence to international standards. Certification bodies such as ISO ensure that products meet necessary performance criteria. It’s prudent for users to request documentation of quality assurance from suppliers. Additionally, engaging with suppliers who provide substantial technical support and after-sales service adds another layer of security in ongoing maintenance endeavors.
Case studies in the industry highlight successful usage of seal kits in prolonging pump life. For example, a large-scale water treatment facility observed a 30% reduction in maintenance costs over five years by incorporating a scheduled seal replacement program. This was achieved through diligent monitoring and collaboration with seal manufacturers to tailor kits specifically for their array of pumps. Similarly, a chemical manufacturing plant that invested in high-performance seal kits reported a significant decrease in production downtime caused by seal failures.
To conclude, mastery of pump seal kits involves a comprehensive understanding of their design and application, as well as diligent maintenance practices. By aligning with professional standards and leveraging the collective expertise of manufacturers and technical consultants, companies can ensure their pump systems operate efficiently and reliably. Recognizing the integral role seal kits play not only enhances pump longevity but also secures operational integrity in the fluid management processes.