In the realm of industrial maintenance and manufacturing, the term seal dust might not yet be on everyone’s radar, but understanding its implications can elevate operational efficiency significantly. Seal dust refers to the fine particles resulting from the wear and tear of seals, commonly found in machinery and industrial equipment. As these particles accumulate, they can impact machinery performance, necessitating both preventive and reactive measures to maintain optimal operations.
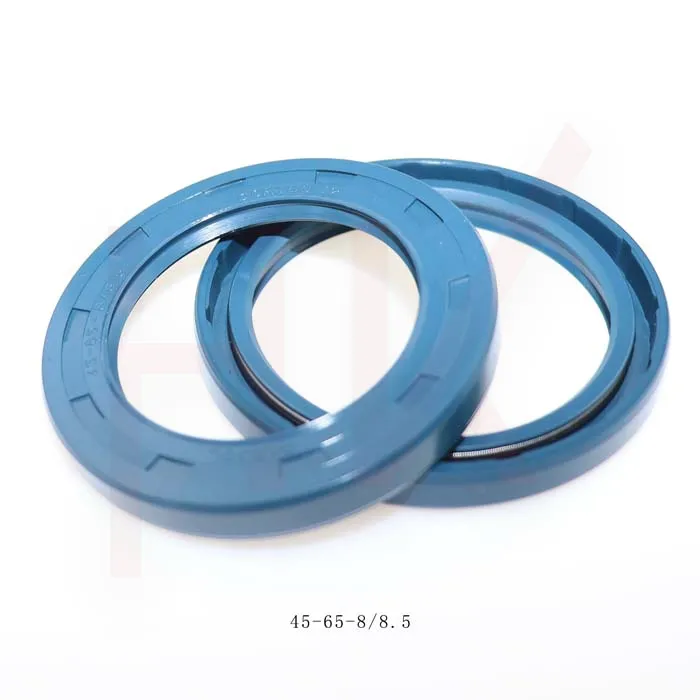
Cutting-edge research underscores the importance of maintaining clean machinery environments, where even minute contaminants like seal dust can play a crucial role. As machinery operates, seals are subject to friction and pressure, which can erode their material over time. This erosion is an inevitable process that, without adequate attention, can lead to micro-contaminations intercepted by machinery mechanisms, thus escalating wear and tear.
Manufacturers and maintenance teams must recognize seal dust as a potential disruptor of product quality and machinery performance.
Seal dust's adverse effects are not confined merely to a machinery system's lifespan. More critically, it can deteriorate product integrity, influencing both aesthetic and functional features. Imagine precision-based equipment where even the slightest misalignment caused by seal wear particles can skew product dimensions or performance, leading to potential losses both financially and reputationally.
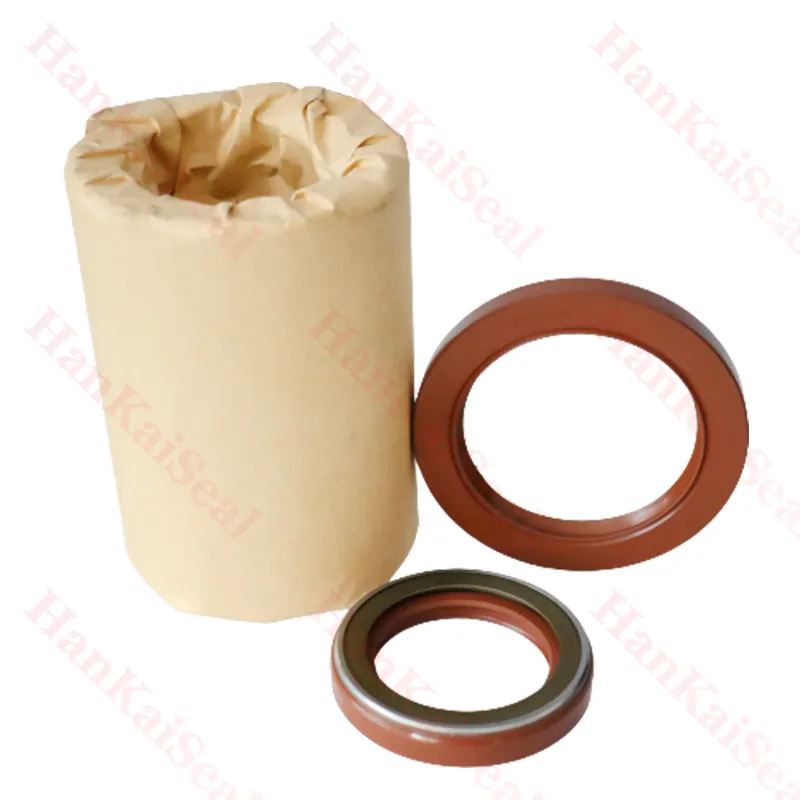
To counteract these effects, adopting a proactive maintenance strategy is essential. This involves routine inspections and cleaning regimens tailored to detect and eradicate seal dust at its inception. Implementing advanced filtration systems designed to capture fine particulates is another forethought method that can significantly diminish the accumulation of seal dust. Moreover, cutting-edge materials in seal manufacturing promise enhanced durability, thereby reducing erosion and minimizing dust production. Understanding the composition of seals and selecting high-performance materials tailored for specific environments can yield a crucial reduction in seal dust deposition.
seal dust
Evidence presented in industrial studies shows that operators who pivot their maintenance strategies to prioritize dust control experience fewer breakdowns and production interruptions. Ensuring clean air conditions and maintaining regulated humidity also support the reduction of airborne seal dust, further optimizing equipment operations.
Technological advancements in monitoring also provide significant support. Deploying IoT-based sensors that track seal performance and wear in real time allows for immediate responsive actions, thereby minimizing the impact of dust formation. An added benefit of these systems is the data they provide, offering a comprehensive understanding of dust patterns, which can then be leveraged to improve future seal designs and maintenance protocols.
Partnership with experts in industrial hygiene and maintenance can further bolster a company’s approach to managing seal dust. Expert partnerships offer specialized knowledge and cutting-edge tools to detect the invisible threats posed by dust. Certified professionals can perform audits and develop actionable strategies to mitigate risk, promoting a culture of trust and reliability in machinery maintenance.
To sum up, recognizing and mitigating the risks associated with seal dust is crucial for maintaining the longevity and efficiency of machinery. The commitment to understanding and addressing this issue signifies dedication to quality, operational excellence, and ultimately ensures a competitive edge in industrial sectors. Embrace a future of reliable, dust-free operations by integrating advanced monitoring, strategic maintenance, and expert collaboration into your organizational practices.