Rubber hub seals are an integral component of many mechanical and automotive systems, serving as the unsung hero in automotive and industrial applications. The intricate role these seals play in safeguarding moving parts from dust, dirt, and moisture makes them indispensable for the longevity of numerous mechanical systems. When selecting a rubber hub seal for your application, understanding the nuances of their composition, functionality, and installation can make a significant difference in efficiency and output.
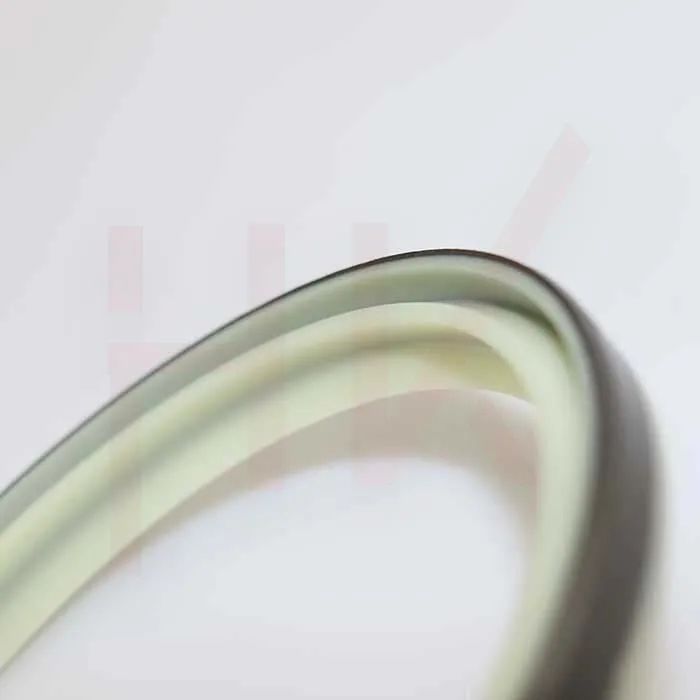
The primary function of a rubber hub seal is to create a barrier against contaminants while retaining necessary lubricants in rotating systems. Designed to withstand high rotational speeds, rubber seals offer the resilience and flexibility needed to maintain their form and function over time. Successful implementation of rubber hub seals demands expertise in both material science and engineering. The choice of rubber compound—whether it be natural rubber, silicone, or nitrile—should consider the operational environment, including temperature extremes and exposure to chemicals. The superior adaptability of rubber hub seals makes them suitable for diverse industrial applications, from automotive vehicles to heavy machinery.
An expert in rubber hub seals can differentiate between the various types available, such as contact and non-contact seals. Contact seals offer robust protection, making them ideal for environments with high contamination risks. Conversely, non-contact seals reduce friction, thereby enhancing energy efficiency—a desirable trait in applications like high-speed motors. Regardless of the type, the key to a seal's effectiveness is precise engineering which ensures a snug fit without compromising performance.
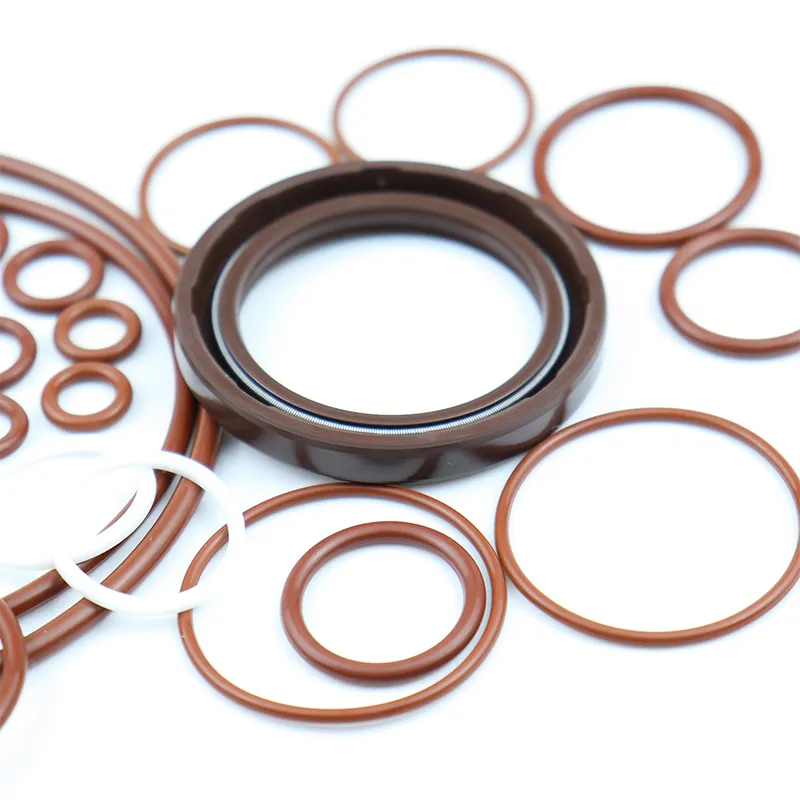
Installation and maintenance of rubber hub seals further emphasize the need for professional expertise. Improper installation can lead to premature wear and tear, resulting in potential system failures. Given the critical role of these seals, it is recommended to engage with certified professionals for their installation and maintenance, ensuring that they are fitted correctly and are functioning to their optimal capacity. Regular inspections for signs of wear, such as cracking or hardening of the rubber, can prevent failures before they escalate into costly repairs.
rubber hub seal
Trustworthiness in rubber hub seal products is largely influenced by the manufacturer's reputation and adherence to quality standards.
Industry authorities and experienced professionals should be prioritized for procuring these seals. Manufacturers who uphold rigorous testing protocols and quality certifications offer assurance that their products can withstand operational demands. User reviews, professional endorsements, and case studies often provide valuable insights into the seal's performance in real-world scenarios.
As industries strive to enhance machine lifespan, efficiency, and safety, the authoritative voice of engineers and technicians is vital in the selection process of rubber hub seals. Continuing education and updates on advancements in material sciences are necessary to maintain expertise in this field. By embodying trustworthiness, expertise, and sustained research, professionals can make informed decisions that align with both industrial standards and specific operational needs.
Rubber hub seals, therefore, represent more than just a component—they are a linchpin that holds together the integrity and functionality of mechanical systems. Integrating these seals with a foundation of expert knowledge and authority ensures that the systems they serve are protected to the highest standard, promoting their longevity and operational effectiveness.