Rotary oil seals play a critical role in the reliable operation of various mechanical systems. Their primary function is to maintain a secure barrier between two environments, often keeping lubricants in while preventing contaminants from entering. Understanding the nuances of rotary oil seals is essential for any engineer or mechanic looking to optimize machinery efficiency and longevity.
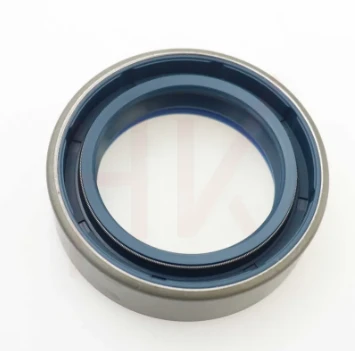
The primary function of these seals lies in their name they seal. But, it's not just about keeping oil in. They also keep dirt, moisture, and other potential contaminants out. This dual-action sealing ensures that the internal environment of an engine or gearbox remains pristine, prolonging the life of the components and reducing the chances of unexpected failures.
Experience has shown that even the smallest imperfections or failures in oil seals can lead to catastrophic results. For example, in automotive engines, a leaky seal might result in oil spilling onto other engine parts, potentially causing fires or severe engine damage. Thus, investing in high-quality rotary oil seals is not just a recommendation—it's a necessity. Manufacturers now understand the importance of precision manufacturing in these parts, using advanced materials such as silicone nitrile or fluoroelastomer that can withstand significant temperature fluctuations and chemical exposures.
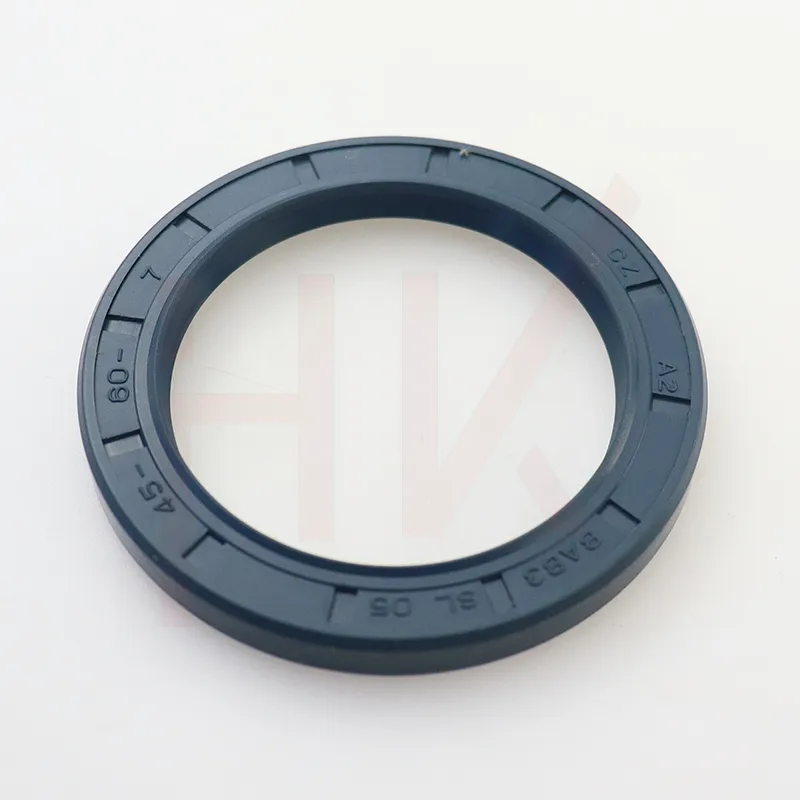
Expertise in selecting the appropriate oil seal for specific applications makes a noteworthy difference. Various factors need consideration when making this selection operating temperature, pressure ratings, shaft speed, and media compatibility are crucial. For high-speed applications, seals with reduced friction structures and improved lubrication processes are preferable. In an environment churning at thousands of revolutions per minute, even the slightest reduction in friction can lead to energy savings and less heat generation, thus prolonging seal life.
rotary oil seals
The array of designs available for rotary oil seals can cater to various specific needs. For instance, the implementation of labyrinth seals in environments where oil leakage is unacceptable has resulted in highly efficient sealing solutions. These design innovations cater to complex systems, from jet engines to precision laboratory equipment. It's not merely about plugging a gap; it's about optimizing the entire system for smooth performance.
Authoritativeness in the domain of rotary oil seals is highlighted by continuous research and development from industry leaders. They are involved not only in manufacturing but also in rigorous testing to ensure seals can withstand real-world applications. Companies often offer detailed case studies and white papers that provide insights into seal performance under myriad conditions, allowing professionals to make evidence-based decisions.
Trustworthiness builds on the shoulders of brands that stand by their product integrity. A seal's performance doesn't depend solely on its material composition but also on the quality assurance processes it undergoes before reaching the consumer. Trust is fostered through warranties, customer support, and an unwavering commitment to quality. When machinery maintenance professionals speak to their suppliers about rotary oil seals, it is the reputation and track record of the brand that often determines their choice.
In conclusion, rotary oil seals are an unsung hero in mechanical systems. Their role in ensuring the longevity and efficiency of machinery is indispensable. Understanding the intricacies involved in their selection and application can not only prevent costly damage but can also offer a competitive edge in machinery performance optimization. Professionals tasked with system maintenance owe it to themselves to keep abreast of developments in seal technologies and to partner with reputable manufacturers who offer proven solutions.