High-speed rotary shaft seals are essential components in many industrial applications, playing a crucial role in ensuring the efficient and reliable operation of machinery. At the heart of various high-velocity systems, these seals help maintain the integrity of fluids, protect bearings from contaminant ingress, and enhance the overall life of the equipment.
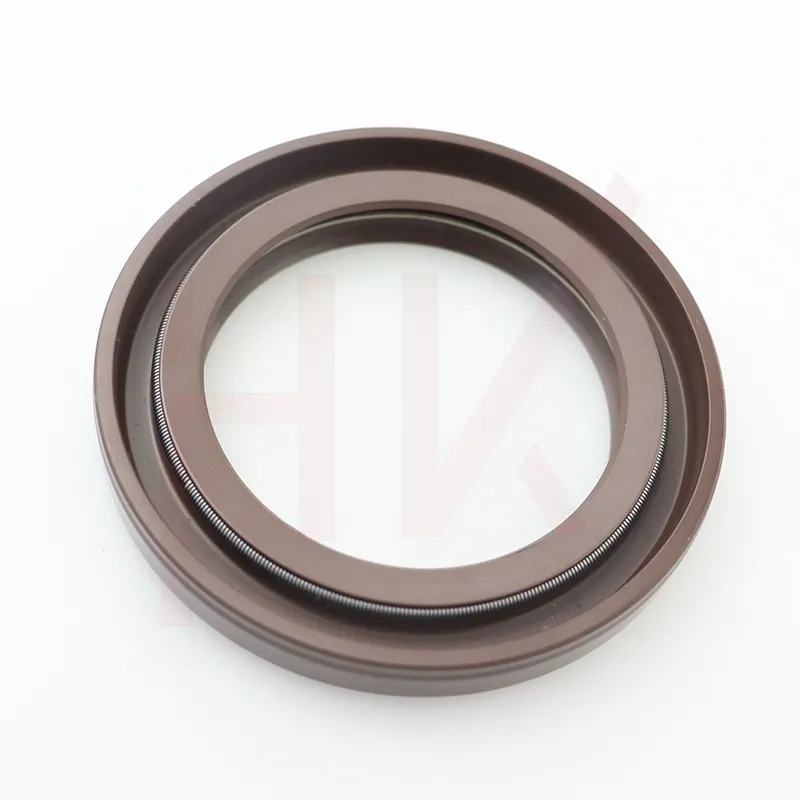
The necessity of high-speed rotary shaft seals cannot be overstated in industries such as aerospace, automotive, oil and gas, and manufacturing. These sectors often require machinery that operates at hundreds to thousands of revolutions per minute (RPM), putting immense stress on mechanical components. Here, shaft seals are instrumental in preventing the leakage of lubricants, which are integral to reducing friction and preventing overheating and wear.
Expertise in selecting the right seal for high-speed applications involves understanding the intricate balance between several important parameters, such as speed, temperature, pressure, and fluid compatibility. An authoritative approach involves recommending materials specifically engineered to withstand these challenging conditions. For instance, seals made from advanced composites or specially coated elastomers can endure the demanding environments where high-speed shafts are prevalent.
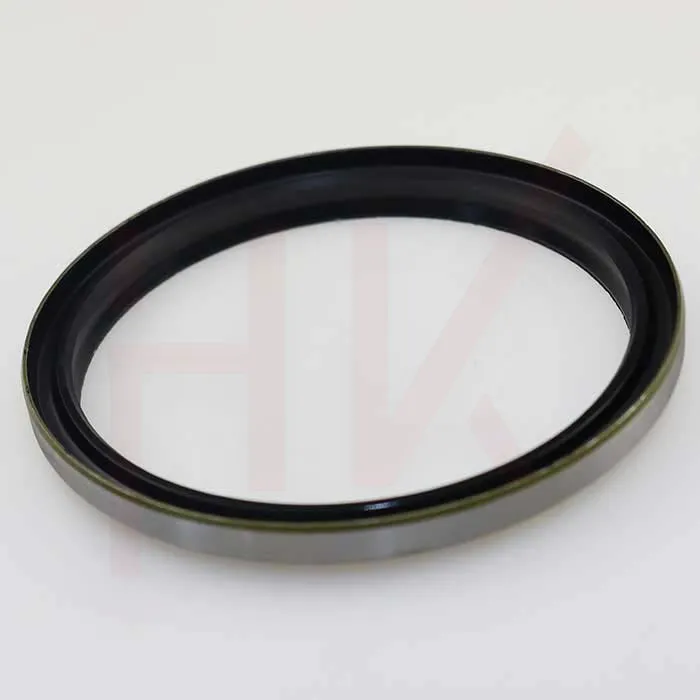
A key factor in the effectiveness of high-speed rotary shaft seals is their ability to handle thermal expansion and contraction. Their design must allow for some movement while maintaining a tight seal, which requires both material flexibility and structural strength. The choice of seal lip geometry, surface finish, and spring-loaded mechanisms are critical decisions made based on real-world engineering experience and predictive modeling.
Trustworthiness in seal performance is of utmost importance to end users, who rely on consistent and predictable operation. Manufacturers must adhere to strict quality control practices, using rigorous testing procedures to simulate intense operational conditions. Furthermore, compliance with industry standards and certifications reinforces the seals’ credibility, offering assurance of their reliability and longevity.
high speed rotary shaft seals
Advanced technological advancements have introduced innovative seal designs and manufacturability improvements. For example, the development of labyrinth seals and magnetic fluid seals provides alternative solutions for environments where traditional contact seals may not perform adequately. Incorporating magnetic fields to contain fluids without physical contact significantly lowers wear and friction, extending maintenance intervals and reducing operational costs.
Customized solutions are often necessary to meet the specific demands of individual applications. Tailoring seals to fit non-standard shaft sizes or creating bespoke material blends that cater to unique chemical exposures and temperatures can make a substantial difference in operational efficiency. Companies that specialize in high-speed rotary shaft seals work closely with engineers to evaluate all aspects of the application, ensuring optimal seal performance and service life.
Building trust with users and ensuring high satisfaction levels demands clear communication about installation, maintenance, and potential troubleshooting. Providing comprehensive guides and training support for operational teams enhances the user experience and maximizes the return on investment.
In conclusion, high-speed rotary shaft seals represent a significant investment in the sustained, efficient operation of high-speed machinery across multiple industries. Their design and application require deep technical knowledge, stringent quality processes, and a commitment to innovation. Organizations dedicated to these principles play a vital role in advancing industrial capabilities and ensuring the reliable functioning of critical equipment worldwide.