Rotary Oil Seals Ensuring Efficient and Seamless Mechanical Operations
In the intricate world of mechanical engineering, rotary oil seals play an indispensable role in ensuring the smooth functioning of various systems. These specialized components are designed to provide a reliable barrier against oil leakage, thereby maintaining the integrity and efficiency of machinery that relies on lubrication. The significance of rotary oil seals extends beyond mere leak prevention; they are crucial for prolonging the lifespan of equipment and preserving the performance standards expected from modern machinery.
A rotary oil seal operates by forming a tight fit around a rotating shaft, effectively separating lubricant from the external environment. This sealing mechanism is typically achieved using materials such as rubber or synthetic compounds that are resilient enough to withstand the constant motion and pressure variations inherent in mechanical operations. The design of these seals often includes features like springs or elastomeric lips that adapt to the shape of the shaft, creating a dynamic yet secure barrier against oil migration.
The importance of rotary oil seals becomes evident when considering the potential consequences of oil leakage. Not only can leaks result in loss of lubricant, leading to increased wear and tear on moving parts, but they also pose environmental hazards and add to maintenance costs. In high-performance applications such as automotive engines or industrial machinery, the failure of an oil seal can lead to catastrophic system failure, underscoring the critical nature of their role In high-performance applications such as automotive engines or industrial machinery, the failure of an oil seal can lead to catastrophic system failure, underscoring the critical nature of their role
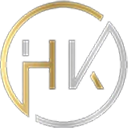
In high-performance applications such as automotive engines or industrial machinery, the failure of an oil seal can lead to catastrophic system failure, underscoring the critical nature of their role In high-performance applications such as automotive engines or industrial machinery, the failure of an oil seal can lead to catastrophic system failure, underscoring the critical nature of their role
rotary oil seals.
Manufacturers invest considerable effort into optimizing the design and material selection for rotary oil seals to ensure compatibility with a wide range of operating conditions. Factors such as temperature extremes, chemical resistance, and physical endurance are all taken into account during the development process. Furthermore, advancements in technology have led to the creation of smarter seals that can self-diagnose issues and even adapt to changing operational demands.
In conclusion, rotary oil seals represent a vital component within the mechanical sector, safeguarding against oil leakage and ensuring machines operate at peak efficiency. Their design and implementation reflect a deep understanding of mechanical dynamics and material science. As technology progresses, it is likely that these seals will continue to evolve, enhancing their effectiveness and expanding their applicability across diverse industries. By preventing small leaks, rotary oil seals contribute significantly to the larger goal of minimizing downtime, reducing environmental impact, and promoting sustainable practices within the mechanical realm.