Replacing seals on a hydraulic cylinder requires not only mechanical skill but also knowledge of the intricacies of hydraulic systems. The hydraulic cylinder, a crucial component in various machinery, relies heavily on the integrity of its seals to function effectively. Here’s a step-by-step guide to help you navigate this process with confidence.
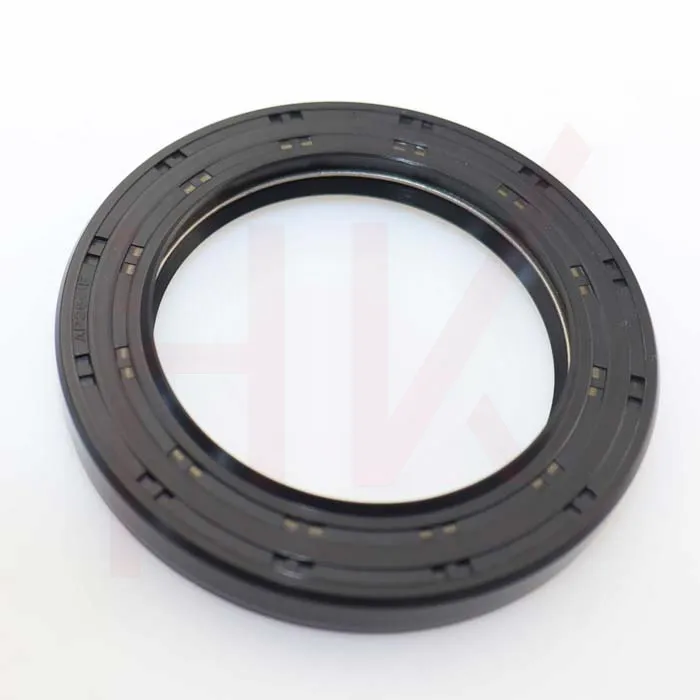
Understanding the Role of Seals
Hydraulic cylinders are designed to transfer force in a linear motion, and their performance is highly dependent on the seals. These seals prevent fluid leakage, maintaining the high-pressure environment needed for the cylinder to operate efficiently. Over time, seals can wear out due to factors like friction, heat, or contamination, resulting in decreased performance or failure of the hydraulic system.
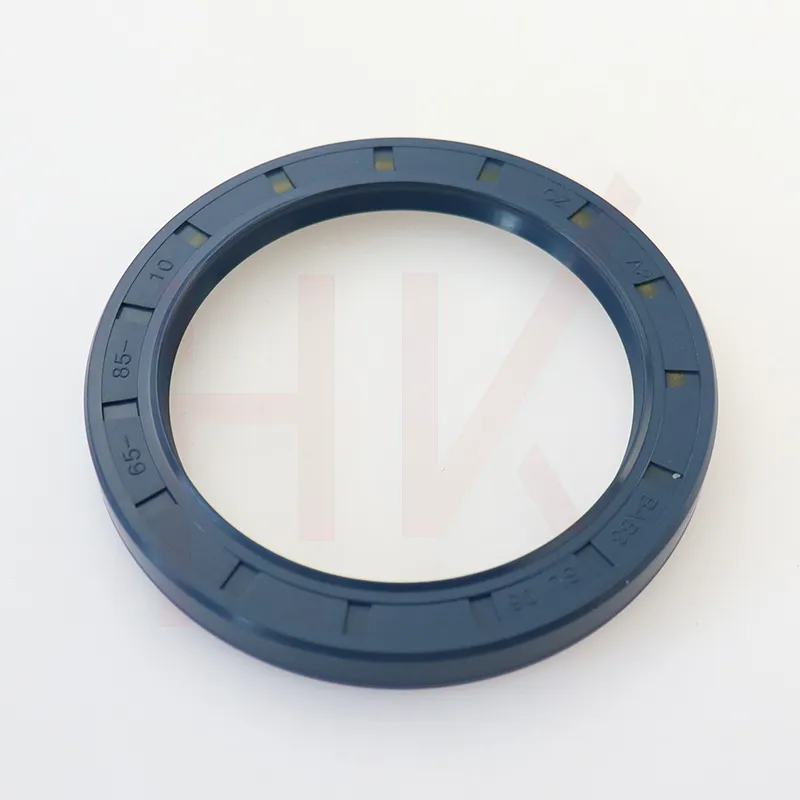
Safety First Preparing for Seal Replacement
Before attempting any replacement, ensure that all safety protocols are observed. Begin by depressurizing the system. Make sure that the machinery is turned off and is not connected to any power source. It is also advisable to use personal protective equipment (PPE) to safeguard against any accidental spillage or injury.
Dismantling the Hydraulic Cylinder
Start by removing the hydraulic cylinder from the equipment. This typically involves loosening the bolts and disconnecting the hydraulic lines. Carefully secure the cylinder in a stable position to prevent it from rolling or falling. Once secured, remove the cylinder head, usually held in place by a set of lock rings or bolts. Be cautious as there might still be some residual hydraulic fluid inside.
Removing the Old Seals
With the cylinder open, you will gain access to the piston, rod, and seals. Carefully extract the old seals using appropriate tools, such as a seal pick or a small screwdriver. Take care not to scratch or damage the metal surfaces during this process. Inspect the surfaces for any signs of wear or damage that could affect the new seals' performance.
replacing seals on a hydraulic cylinder
Selecting the Right Replacement Seals
Choosing the correct replacement seals is critical. Consider factors such as the type of hydraulic fluid used, the temperature range, and the pressure ratings of the system. It’s essential to use seals that match the manufacturer’s specifications to ensure compatibility and optimal performance.
Installing New Seals
Before installing new seals, lubricate them with a compatible hydraulic oil to ease installation and reduce the risk of damage. Carefully fit each seal into its designated groove, ensuring it sits perfectly without pinching or twisting.
Reassemble the hydraulic cylinder by reversing the disassembly steps. Make sure all components are aligned correctly, and all bolts are securely tightened to the manufacturer’s specifications.
Testing the Reassembled Cylinder
Once reassembled, reattach the hydraulic cylinder to your equipment. Reconnect the hydraulic lines and slowly repressurize the system. Observe the cylinder in operation to ensure there are no leaks and that the system functions smoothly. It might be necessary to cycle the cylinder several times to ensure proper seating of the new seals.
Regular Maintenance and Monitoring
Regular inspection and maintenance of hydraulic cylinders can prevent premature seal failure. Keep the system clean, monitor for fluid leaks, and address any unusual noises or vibrations promptly. This proactive approach will extend the life of your seals and optimize the performance of your hydraulic system.
By adhering to these meticulous steps, you will not only ensure the longevity of the hydraulic cylinder but also enhance the operational efficacy of the machinery it powers. For complex repairs or if you encounter difficulties, consulting with a hydraulic specialist ensures that the task is handled with the utmost expertise, reinforcing confidence in the system's dependability.