Hydraulic cylinders are an essential component in many industrial and manufacturing processes. They are used to generate linear motion and force by converting hydraulic energy into mechanical energy. Over time, the seals in hydraulic cylinders can wear out or become damaged, resulting in leaks and reduced performance. When this happens, it is important to replace the seals promptly to prevent further damage and ensure the proper functioning of the hydraulic cylinder.
Replacing seals in a hydraulic cylinder may seem like a daunting task, but with the right tools and knowledge, it can be done efficiently and effectively. The first step in replacing seals is to identify the type of hydraulic cylinder and seals that need to be replaced. It is essential to use the correct seals for the specific cylinder to ensure a proper fit and prevent leaks.
Once the type of seals needed has been determined, the next step is to gather the necessary tools and equipment. This may include a seal kit, hydraulic fluid, wrenches, pliers, and a clean work area. Before starting the replacement process, it is important to release the pressure in the hydraulic cylinder to prevent any accidents or injuries.
To replace the seals, the hydraulic cylinder must be disassembled carefully. This involves removing the end cap, piston, and other components to access the seals. It is important to pay attention to the orientation and placement of each component to ensure proper reassembly later on It is important to pay attention to the orientation and placement of each component to ensure proper reassembly later on
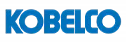
It is important to pay attention to the orientation and placement of each component to ensure proper reassembly later on It is important to pay attention to the orientation and placement of each component to ensure proper reassembly later on
replacing seals hydraulic cylinder.
After the old seals have been removed, the new seals can be installed. It is crucial to lubricate the new seals with hydraulic fluid before placing them in the cylinder to prevent damage during installation. Once the new seals are in place, reassemble the hydraulic cylinder in the reverse order of disassembly.
After reassembly, it is important to test the hydraulic cylinder for leaks and proper functioning. This can be done by pressurizing the cylinder and checking for any visible leaks or issues. If everything appears to be in working order, the hydraulic cylinder can be put back into service.
Regular maintenance and inspections of hydraulic cylinders can help prevent seal failures and other issues. It is recommended to inspect the seals regularly for wear and damage and replace them as needed to ensure the optimal performance of the hydraulic cylinder.
In conclusion, replacing seals in a hydraulic cylinder is a necessary maintenance task that can help prolong the lifespan and efficiency of the cylinder. By following the proper procedures and using the correct tools and seals, the replacement process can be completed successfully. Regular maintenance and inspections are key to preventing seal failures and ensuring the proper functioning of hydraulic cylinders in various industrial applications.