Radial oil seals, often underrated in their scope, are fundamental components in a myriad of mechanical systems, guaranteeing the containment and separation of fluids across rotating shafts. Their unique design ensures unparalleled performance, making them indispensable in industries ranging from automotive to aerospace. However, the secret to leveraging their full potential lies in understanding their operational intricacies combined with the knowledge gained from practical experience and expert insights.
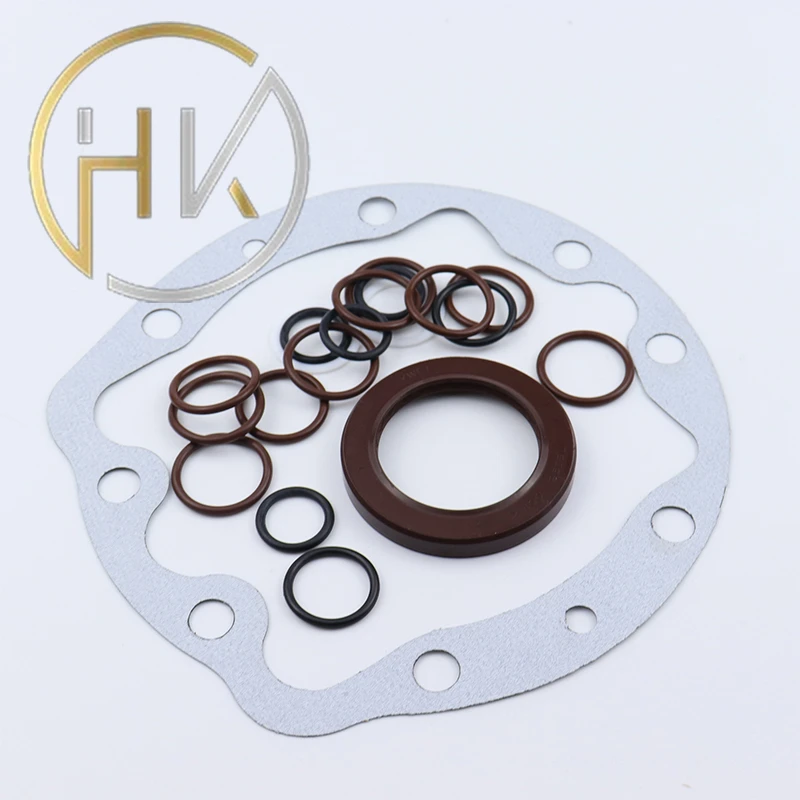
Experience has shown that radial oil seals, though compact, play a critical role in machinery efficiency. A typical scenario is within an automotive engine, where these seals are paramount in preventing oil leaks that could lead to engine failures. Over the years, users have documented instances where selecting the appropriate material for the seal against the operational environment significantly extended the lifespan of the engines. For instance, nitrile rubber seals offer excellent oil resistance and are cost-effective for general applications, while fluoroelastomer seals, although higher in cost, provide superior heat resistance and are optimal for high-temperature environments.
A deep dive into their engineering reveals the expertise embedded in radial oil seal design. At the core of their function is the lip design, which plays a significant role in maintaining the integrity of the seal under pressure differentials. Experts recommend a thorough examination of the lip geometry and its contact with the shaft surface to mitigate wear and tear. The spring-loaded lip construction, often found in modern radial oil seals, exemplifies a design consideration that enhances sealing efficacy by compensating for minor shaft misalignments, thus ensuring a robust seal against contaminants.
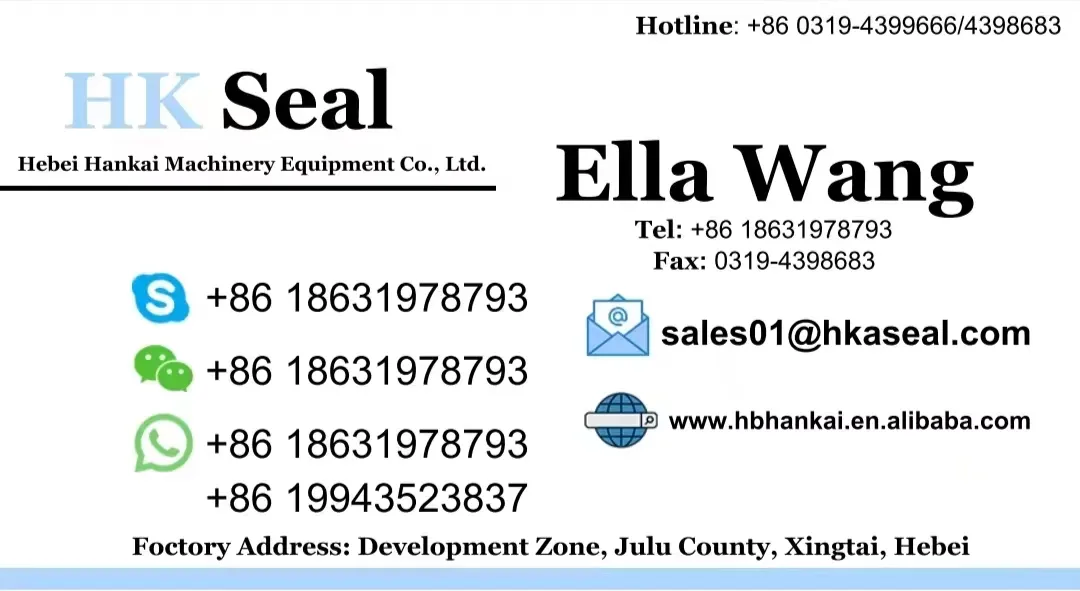
radial oil seal
The authoritativeness of radial oil seals can be attributed to their widespread acceptance across numerous stringent applications. Take the aerospace sector as an illustrative example, where radial oil seals must comply with rigorous standards such as AS9100. Here,
any compromise in seal quality could lead to catastrophic failures. It is this adherence to high manufacturing standards and relentless testing that consolidates these seals as trusted components in critical applications. The expertise of established manufacturers in integrating proprietary compounds and cutting-edge technology into seal production has set benchmarks within the industry.
Trustworthiness in selecting radial oil seals begins with the brand reputation. Leading manufacturers provide comprehensive certifications and quality assurances that underscore their commitment to performance and reliability. Additionally, case studies have frequently highlighted scenarios where adherence to specified maintenance protocols greatly enhanced seal longevity and performance predictability. Professionals also emphasize the importance of partnering with suppliers who offer detailed installation guidelines and post-installation support, thereby fostering an ecosystem of trust between the manufacturer and end-user.
In conclusion, radial oil seals may appear mundane, but their impact is vast and multifaceted. Bridging the expertise in design with empirical experience, while maintaining stringent adherence to quality and reliability, demarcates the profound importance of these components. For companies eager to implement robust solutions, the path is clear invest in expertise, rely on authoritative choices, and cultivate trust through transparent practices. Radial oil seals, when chosen and used correctly, safeguard vital assets, ensuring operational consistency in even the most demanding conditions.