When it comes to ensuring the optimal performance and longevity of hydraulic and pneumatic systems, piston wiper seals play an indispensable role. At first glance, these components might appear minor compared to the complex equipment they inhabit. However, the truth is that the piston wiper seal is a linchpin in safeguarding your machinery from the adverse effects of environmental contaminants such as dirt, dust, and moisture.
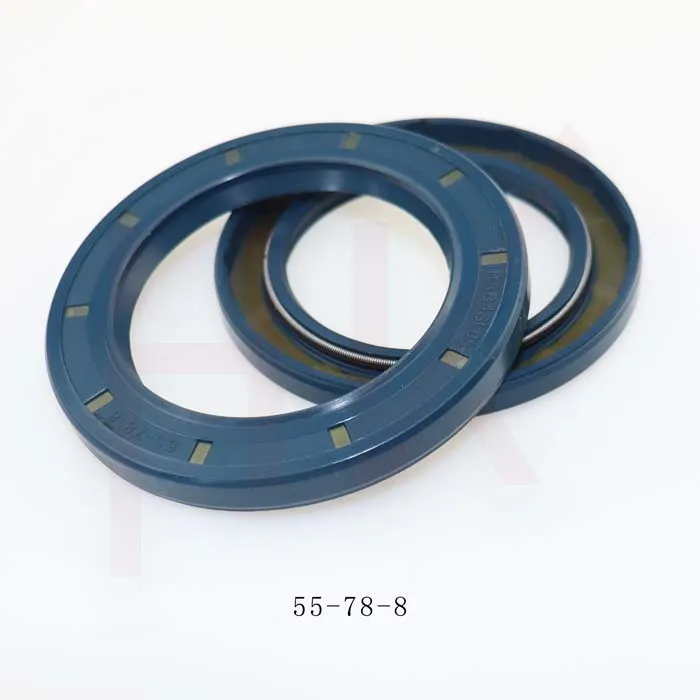
Every system using pistons can benefit immensely from this unassuming yet crucial seal. Designed specifically to keep your systems free from contamination, piston wiper seals prevent the ingress of foreign particles that might otherwise accumulate within cylinder assemblies and compromise the efficiency and functionality of the equipment. A poorly functioning piston wiper seal can lead to wear and tear that is both premature and costly. This makes the choice of the right material and design essential for industries relying on such systems.
Material selection for piston wiper seals is key to ensuring their efficacy and durability. They are typically made from high-quality elastomers or thermoplastic polyurethane (TPU), each offering unique advantages. For example, elastomers provide excellent flexibility and resistance to dynamic thermal conditions, making them suitable for a range of temperatures. On the other hand, TPU is renowned for its abrasion resistance and strength under high-pressure conditions, often preferred in more demanding applications.
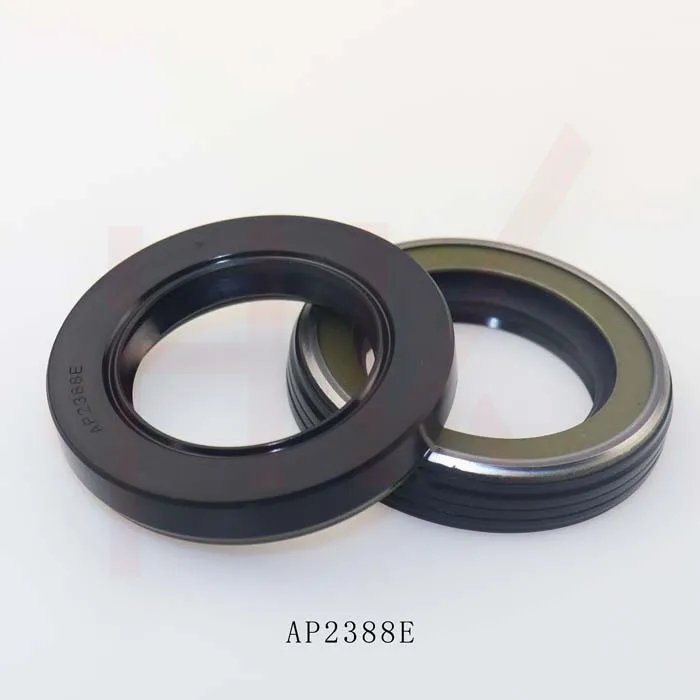
The expertise behind choosing the right piston wiper seal involves assessing both the operational environment and the specific requirements of the machinery. Understanding these dynamics allows engineers to recommend seals that not only meet but exceed performance expectations. This expert-driven selection process is underpinned by a deep knowledge of fluid dynamics, material science, and mechanical engineering.
It's not enough to merely select the right piston wiper seal; proper installation and maintenance are paramount in realizing their full potential. During installation, care must be taken to prevent any deformation of the seal, and lubrication is often necessary to reduce initial friction. Once installed, regular maintenance checks should be implemented to ensure that the seal remains intact and is not subject to any wear that could compromise its effectiveness. Maintaining proper records of these checks can help track the performance of the seal and anticipate any needs for replacement or adjustment.
piston wiper seal
Furthermore, the authoritative reliance on piston wiper seals extends across a multitude of industries, from automotive and aerospace to heavy machinery and industrial manufacturing. In automotive systems, they are critical in shock absorbers and steering systems, demonstrating trustworthiness by enhancing vehicle safety and performance. Aerospace applications depend heavily on piston wiper seals to maintain the integrity of hydraulic systems in aircraft, where failure is not an option.
In the world of heavy machinery, failure to implement effective piston wiper seals can lead to substantial downtime and financial loss due to repairs and lost productivity. Hence, these seals become a deciding factor in operational reliability and cost efficiency.
The trust placed in piston wiper seals by industry professionals stands as a testament to their authority in maintaining system performance and reliability. Critical system failures can often be attributed to the oversight in seal selection or maintenance, underscoring their role as key players in industrial safety and efficiency.
In conclusion, the unrivaled significance of piston wiper seals lies in their role as guardians against contamination and wear. With expertise in material selection and maintenance, these seals extend machinery life and enhance operational reliability. For anyone invested in the efficient operation of hydraulic and pneumatic systems, understanding and utilizing the full capabilities of piston wiper seals is not just an option but a necessity. Their authoritative impact across various industries underscores the trust and reliance placed upon them by professionals worldwide, affirming their place as a cornerstone of modern mechanical applications.