The right piston seal kit can make all the difference in the performance and longevity of hydraulic and pneumatic systems. Industries worldwide rely on these kits to maintain efficiency and prevent downtime, underscoring their crucial role in operational mechanics.
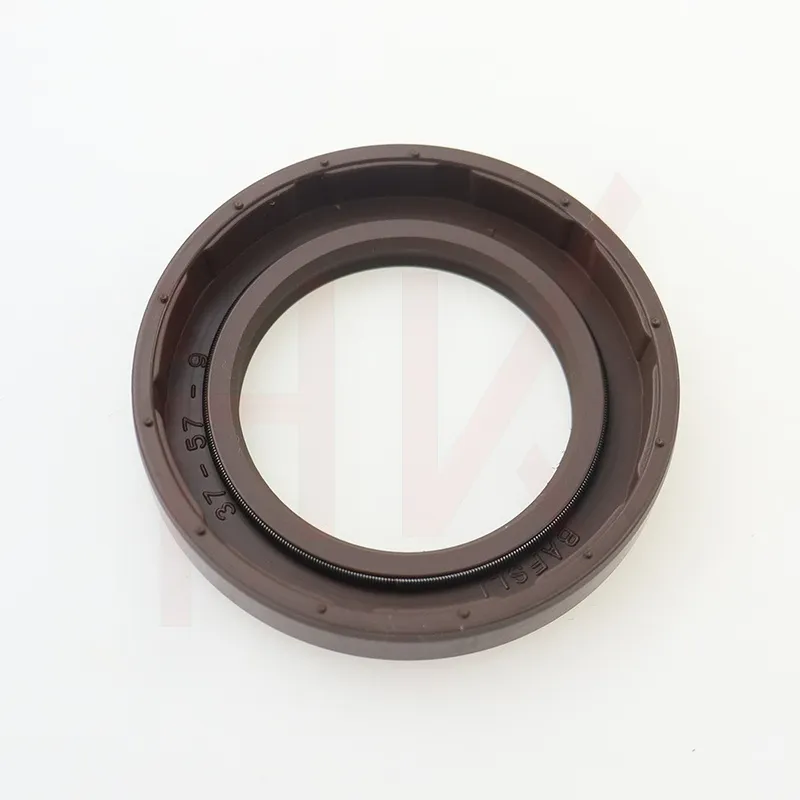
From agriculture to aerospace, piston seal kits are integral to the seamless function of machinery, providing a reliable barrier against fluid leakage. When selecting a piston seal kit, it's essential to understand the unique intricacies and components that contribute to optimal performance.
Piston seal kits consist of several key components, each designed to enhance performance and reliability. Commonly, these kits include the primary seal, wear rings, and a secondary seal that work in unison to ensure maximum effectiveness. The primary seal acts as the primary defense against fluid leakage, ensuring pressure is maintained throughout the cylinder. Wear rings serve as stabilizers that optimize concentricity and prevent metal-on-metal contact. Secondary seals provide an additional layer of protection, ensuring minimal fluid escape even in cases of primary seal failure.
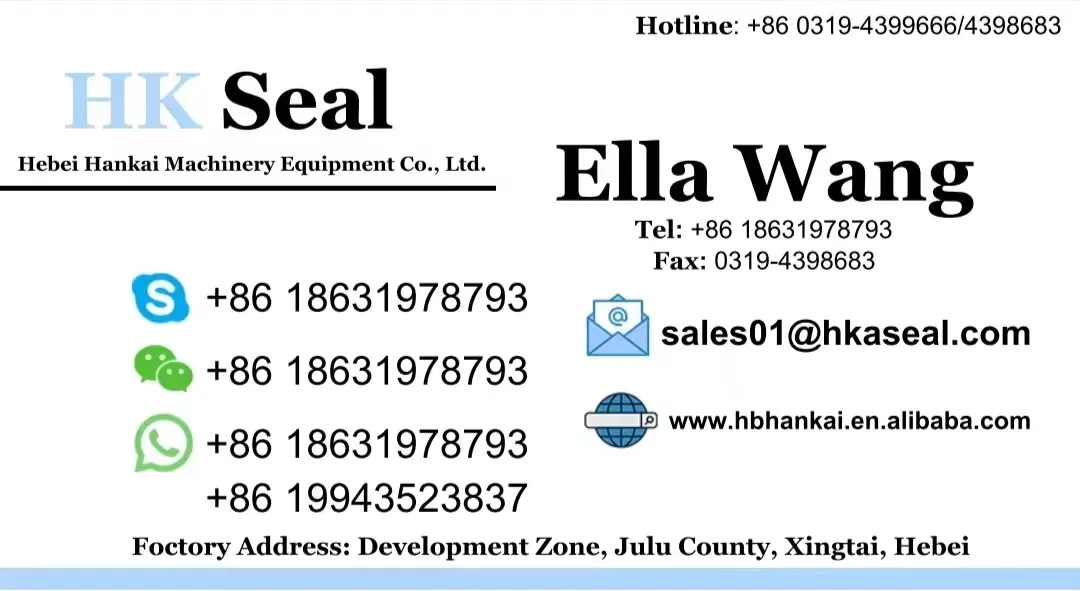
One of the most critical aspects affecting the choice of a piston seal kit is the material composition. Many kits use elastomers like polyurethane, which offer excellent abrasion resistance and longevity. Alternatively, PTFE (Polytetrafluoroethylene) seals provide exceptional chemical resistance and can function efficiently across a wide temperature range.
Understanding the specific application environment is vital in selecting the right piston seal kit. Industries such as construction require piston seals that can endure extreme environmental conditions, like exposure to dust and variations in temperature. In contrast, the pharmaceutical industry may prioritize piston seals made from materials that can resist aggressive cleaning agents and comply with stringent regulatory standards.
The advancements in seal technology have transformed how industries view operational efficiency. Modern piston seal kits are designed with precision engineering to minimize friction, thereby reducing wear and energy consumption. The integration of advanced manufacturing techniques, like computer-aided design and 3D printing, ensures that piston seals meet the highest standards of accuracy and reliability.
piston seal kit
Customization is another factor that enhances the expertise in piston seal kits. Manufacturers now offer personalized solutions tailored to specific machine models and operational needs, providing clients with kit options that precisely match their mechanical and environmental demands. This level of customization is particularly advantageous for organizations looking to optimize their machinery’s performance and extend its service life.
Authoritativeness is demonstrated through rigorous testing and adherence to industry standards, which adds layers of trustworthiness to piston seal kits. Accredited laboratories conduct durability tests under simulated working conditions, ensuring each kit can withstand real-world challenges. Compliance with international standards like ISO and ASTM further underscores the reliability and performance of these kits.
It's essential to rely on reputable suppliers who can offer not only top-quality piston seal kits but also expert guidance and customer support. A trusted supplier will have a proven track record, backed by verifiable customer testimonials and industry certifications.
Investing in high-quality piston seal kits is not merely a purchasing decision but a strategic move towards enhancing machinery lifespan and operational efficiency. The proactive approach involves routine inspections and timely replacements, preventing potential downtimes and reducing costly repairs.
In summary, the relevance of piston seal kits in various industries highlights the importance of informed decision-making, expert knowledge, and reliable supplier partnerships. Every piece of machinery represents a significant investment, and a piston seal kit is an essential component in safeguarding that investment. The future of operational efficiency and durability will greatly depend on innovations and advancements in piston seal technology, paving the way for more resilient and robust mechanical systems.