Oil wiper rings are crucial components in a multitude of machinery, playing an essential role in ensuring the efficient operation and longevity of various systems. These rings, often overlooked in the grand scheme of engine mechanics and mechanical assemblies, serve the critical purpose of managing oil flow and minimizing leakage. Understanding their function, development, and proper application can dramatically impact the performance and reliability of machinery.
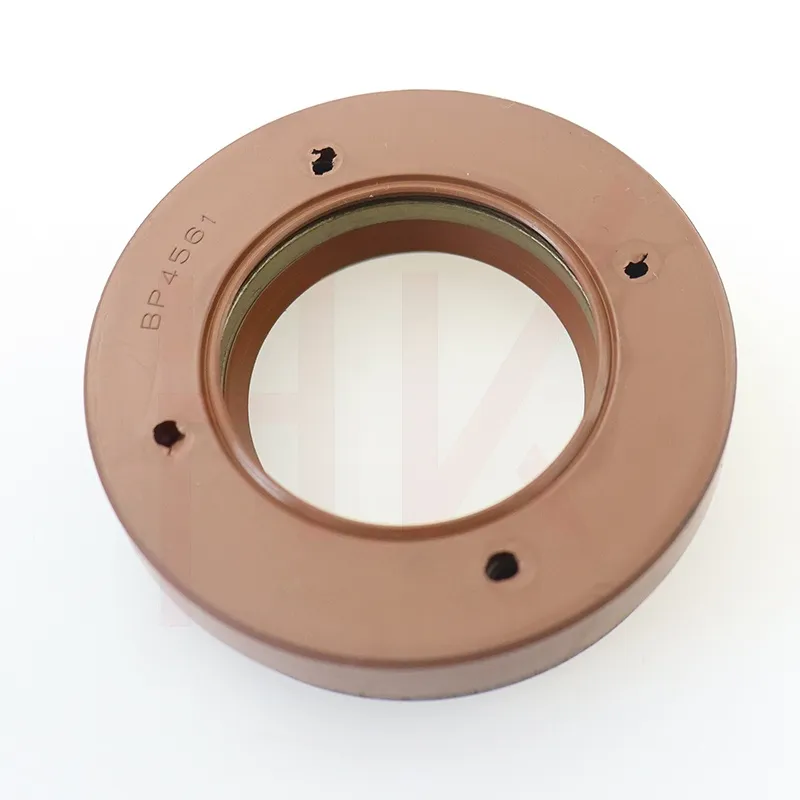
Oil wiper rings, also referred to as oil control rings, are primarily used in engines and compressors. Their role is to scrape excess oil off the cylinder walls back into the crankcase, preventing it from entering the combustion chamber. This function is vital, as excessive oil consumption can lead to increased emissions and reduced efficiency in combustion engines. Moreover, in non-combustion environments, such as compressors, improper oil management can cause contamination, elevating maintenance requirements and potentially leading to mechanical failure.
The design of oil wiper rings involves precise engineering to cater to the specific requirements of different machinery. Each ring must be crafted to endure high temperatures, pressure variations, and friction, maintaining its integrity over extensive periods of operation. Material selection is crucial; high-quality metals and advanced composites are commonly used to withstand the demanding conditions of various applications. The surface finish and tension of these rings are meticulously calibrated to offer optimal performance, reducing wear and tear on both the rings and the cylinder walls.
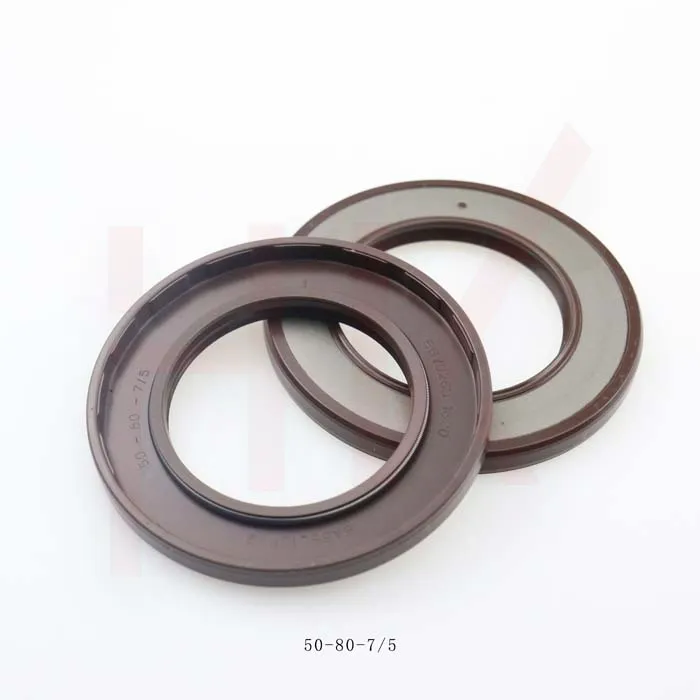
In terms of experience, having encountered numerous instances where improper oil wiper ring selection or installation led to mechanical issues, it becomes clear how decisive these components are. Oil wiper ring failure can manifest as excessive oil consumption, smoke emission from the exhaust, or reduced engine efficiency. Regular inspections and maintenance are essential to identify signs of wear or damage in the rings. Anomalies such as scoring on the cylinder walls or unusual oil consumption metrics can often be traced back to failing oil wiper rings.
oil wiper ring
Professionals in the field understand the necessity of matching the correct oil wiper ring specifications with the intended application. Expert installation is paramount; improper seating or incorrect tension settings may lead to premature failure. Training and experience play a significant role here. Mechanics and technicians with a deep understanding of engine dynamics and component behavior can foresee potential issues and optimize ring performance through precise installation and adjustment.
Authoritative manufacturers of oil wiper rings commit to rigorous testing procedures and quality standards, ensuring each product performs under expected conditions. These manufacturers often provide detailed guidelines and support to assist in the correct implementation of their products. It's advisable for practitioners to rely on established brands and suppliers known for their research and development capabilities, as these companies offer products with verified performance records and durability.
Trust in the longevity and performance of oil wiper rings is further enhanced through certifications and adherence to industry standards. Compliance with ISO and ASTM standards indicates that the rings have been produced under stringent quality control measures. Such certifications are not just formalities but provide assurance of the product's reliability, reinforcing trustworthiness among users.
To conclude, oil wiper rings, though often underestimated, are indispensable in maintaining the efficiency and integrity of engines and compressors. Their expert design, informed application, and trustworthy performance underscore their value in mechanical systems. For optimal machinery performance, invest in quality oil wiper rings, installed by knowledgeable professionals, and sourced from reputable manufacturers. This approach not only ensures maximum efficiency but also extends the operational lifespan of the machinery, delivering measurable benefits in performance and cost-efficiency over time.