When selecting the right hydraulic oil seal material for your machinery, understanding the nuances of each option can make a significant difference in performance and longevity. Hydraulic oil seals are vital in preventing fluid leakage, maintaining pressure, and excluding contaminants, thus safeguarding equipment and ensuring operational efficiency. A variety of materials are available for crafting these seals, each with unique properties and suited for specific applications.
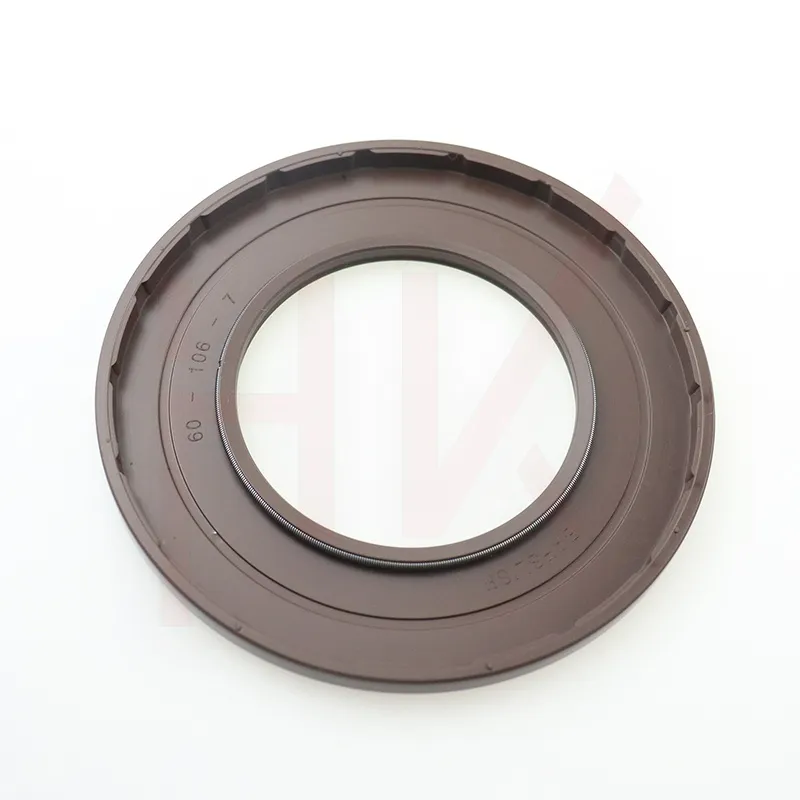
Nitrile Butadiene Rubber (NBR), commonly known as Nitrile, tops the list for its widespread usage. Known for its excellent resistance to petroleum-based oils and fuels, it serves a range of industries. Typically, NBR shines in moderate temperature applications from -40°C to 120°C. Its robustness in resisting wear and tear as well as its flexibility, makes it suitable for most common hydraulic systems. However, it’s less effective when exposed to ozone or weathering, which should be kept in consideration.
For applications where high temperature resistance is crucial, Fluorocarbon Rubber, known as Viton, becomes the material of choice. It withstands temperatures up to 250°C,
making it ideal for high-heat environments. Beyond temperature, Viton exhibits superior chemical resistance to various fluids and gases. This makes it ideal for specialized industries using aggressive fluids. However, its higher cost may not justify its use in all applications.
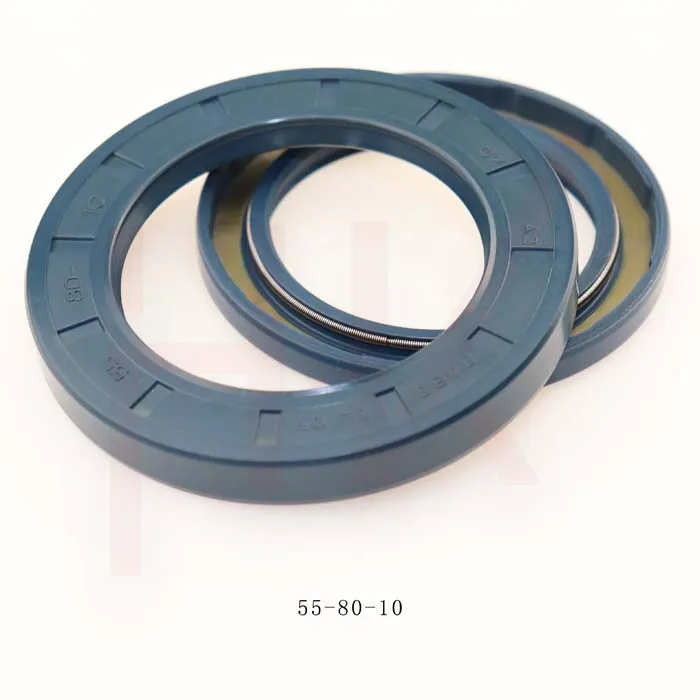
In scenarios where affordability and temporary performance are desired, Polyurethane (AU, EU) emerges as an appealing option. Polyurethane seals boast exceptional mechanical properties including high tensile strength and excellent abrasion resistance. These properties make them well-suited for high-pressure hydraulic systems. Though, polyurethane can become brittle at low temperatures and may not offer the same chemical resistance as more expensive options.
hydraulic oil seal material
For applications in extreme cold or where flexibility is paramount, Silicone rubber is unmatched. It retains its elastomeric properties at temperatures as low as -60°C. Additionally, silicone has excellent thermal stability up to 200°C and good resistance to ozone and weathering. These characteristics make it invaluable in aerospace and food processing equipment where stringent requirements prevail.
Ethylene Propylene Diene Monomer (EPDM) is another viable choice, particularly in applications involving water or steam. It's highly resistant to water, making it ideal for hydraulic systems exposed to moisture or steam. EPDM also stands up well to heat, light, and ozone exposure. However, its performance decreases when in contact with petroleum-based fluids and greases.
Material selection for hydraulic oil seals should also consider hardness, a factor influencing both static and dynamic seal performance. The right hardness ensures a balance between flexibility and durability. A softer seal provides better leakage control while a harder seal might withstand higher pressures without deforming.
Ultimately, the decision on the right hydraulic oil seal material hinges on a keen understanding of the operational environment, the properties required to withstand the application’s challenges, and a strategic weighing of cost versus longevity. Consulting with manufacturers or material experts offers valuable insights and further assurance that the best choice is made for your specific hydraulic needs. Prioritizing material integrity and suitability will not only extend the life of the seals but also protect the equipment, optimizing performance and productivity across its lifecycle.