Oil seals are essential components in various machinery and automotive systems, preventing leakage of lubricants and blocking entry of contaminants. Their functionality hinges on an effective seal between two surfaces in various operating conditions. When contemplating oil seal prices, numerous factors play a role, impacting their cost-effectiveness and functionality in applications.
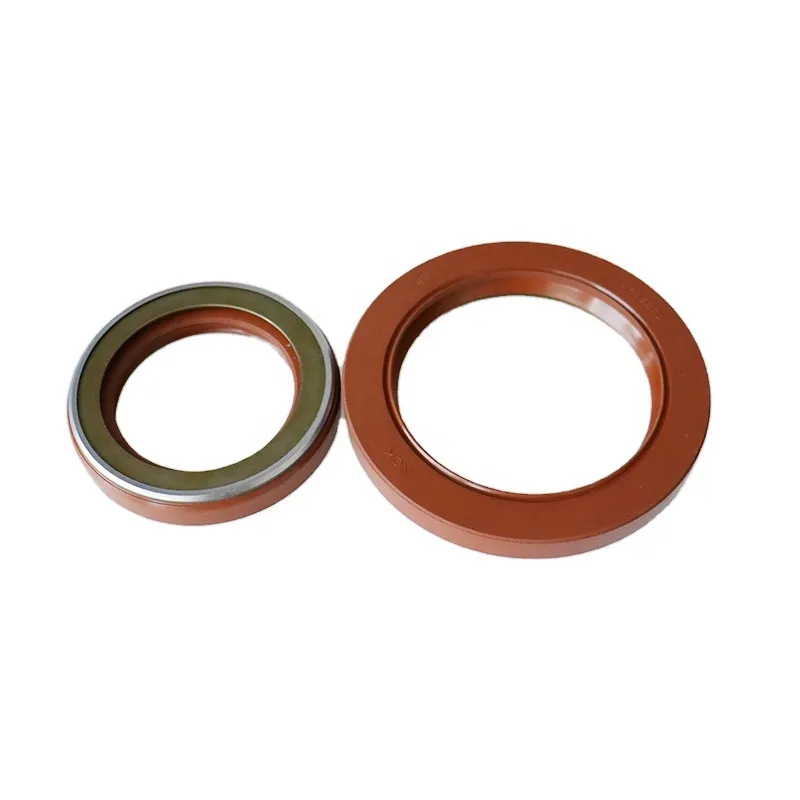
Understanding what influences oil seal pricing begins with the material choices available. Oil seals are typically made from nitrile, silicone, fluorocarbon, or PTFE, each offering unique properties suited for specific environments. Nitrile rubber seals are generally more affordable due to their versatility and adequate performance in moderate temperature environments. In contrast, fluorocarbon seals, suited for high-temperature and chemically aggressive applications, demand higher prices, reflecting their specialized usage and superior durability.
Manufacturing processes also contribute significantly to oil seal prices. Precision engineering ensures optimal performance, with costs reflecting the manufacturing complexity and material waste management. Although mass production can reduce individual unit costs, custom-designed seals cannot leverage economies of scale, leading to higher price points. These bespoke solutions often necessitate an intricate manufacturing process to meet specific operational demands, which explains the price disparity between standard and specialized seals.
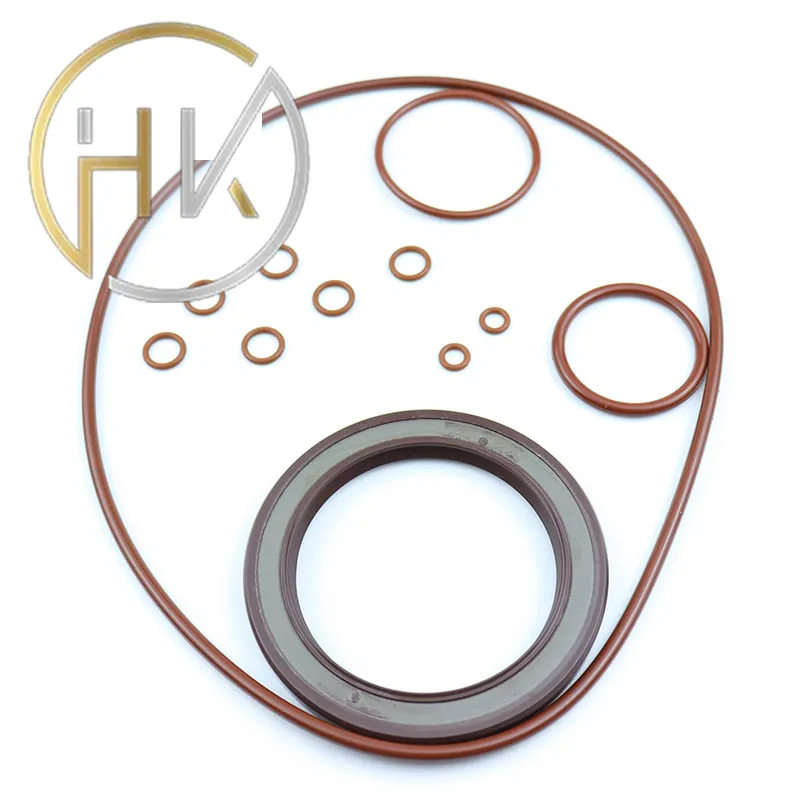
When evaluating oil seal prices, it's also crucial to consider the technical specifications required for your specific application. Seals that must withstand extreme pressures or rotational speeds may incur additional costs due to enhanced designs or unconventional materials. Seals with unique profiles or integrated features, such as dust lips or composite materials, also factor into the pricing structure due to their complexity and enhanced utility.
Furthermore, emphasis on brand reputation and origin can influence oil seal pricing. Reputable brands often price their products higher based on a legacy of quality and reliability, providing assurance and consistency to end-users. Such products are likely subject to rigorous testing and quality assurance protocols, justifying their price by reducing failure rates and downtime in applications. Meanwhile, oil seals manufactured in regions with higher labor costs or stringent regulatory requirements may also be priced higher, reflecting the manufacturing conditions.
oil seal price
Additionally,
oil seal distribution channels can impact price variations. Direct purchases from manufacturers might afford savings compared to retail purchases, which could include additional logistical and branding costs. Online platforms may offer competitive pricing due to reduced overheads, though caution should be exercised to verify product authenticity and reliability.
In evaluating oil seal costs, weigh them against the total cost of ownership. High-quality oil seals, though initially more expensive, can offer long-term savings by minimizing maintenance cycles and preventing costly equipment failures. Consideration of the seal's lifecycle, energy savings from improved efficiency, and reduced environmental impact should also factor into the cost assessment.
Finally, staying informed about market trends and technological advancements in oil seals can aid in cost-effective purchasing. Emerging materials with improved performance characteristics may offer better value propositions. Additionally, innovations in seal design can enhance efficiency and lifespan, providing long-term benefits that might not be immediately apparent in the price tag.
Ultimately, the decision on oil seal selection should not pivot solely on price. Instead, it should harmonize with application requirements, reliability, and quality. By understanding the multifaceted influences on oil seal pricing, businesses can make informed decisions that align with their operational goals and budgetary constraints, ensuring optimal performance and value.