Oil seal kits are essential components in various mechanical systems, offering critical protection against contaminants and ensuring efficient machinery operation. These kits are designed to prevent leakage of lubricants, which not only maintains the optimal performance of equipment but also extends its lifespan. As someone with years of experience in the mechanical industry, I've seen firsthand the transformative impact of using high-quality oil seal kits on machinery maintenance and performance.
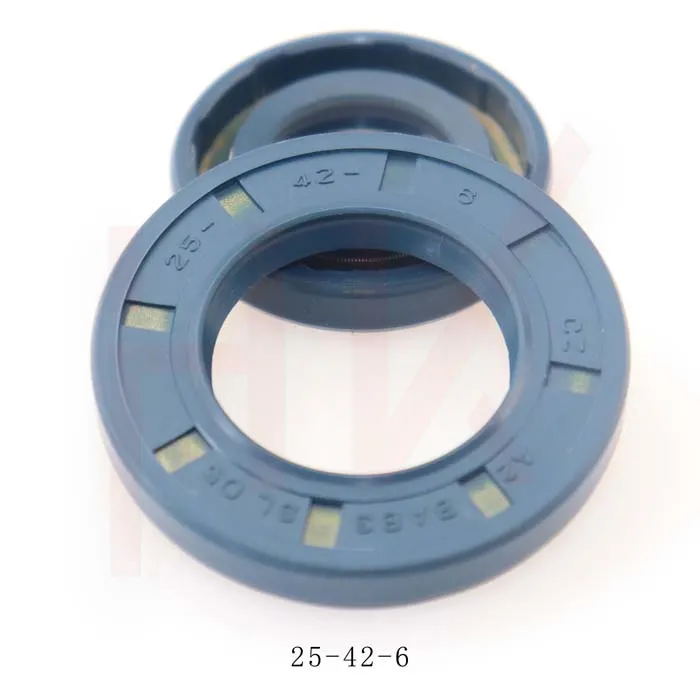
The selection of the right oil seal kit is crucial, and this requires an understanding of the specific requirements of the machinery. Each component within the kit serves a distinct purpose, from sealing to allowing for movement and alignment within shafts and other parts. Therefore, considering factors such as temperature, pressure, and the type of fluid involved is fundamental in choosing the correct kit.
From a professional standpoint, the expertise in oil seal kits begins with recognizing the materials used. Most oil seals are made from materials such as nitrile rubber, fluorocarbon, silicone, and polyurethane, each offering unique benefits. For instance, fluorocarbon is known for its excellent heat resistance and is often recommended for systems operating at high temperatures, whereas nitrile rubber is preferred for applications involving oil and fuel.
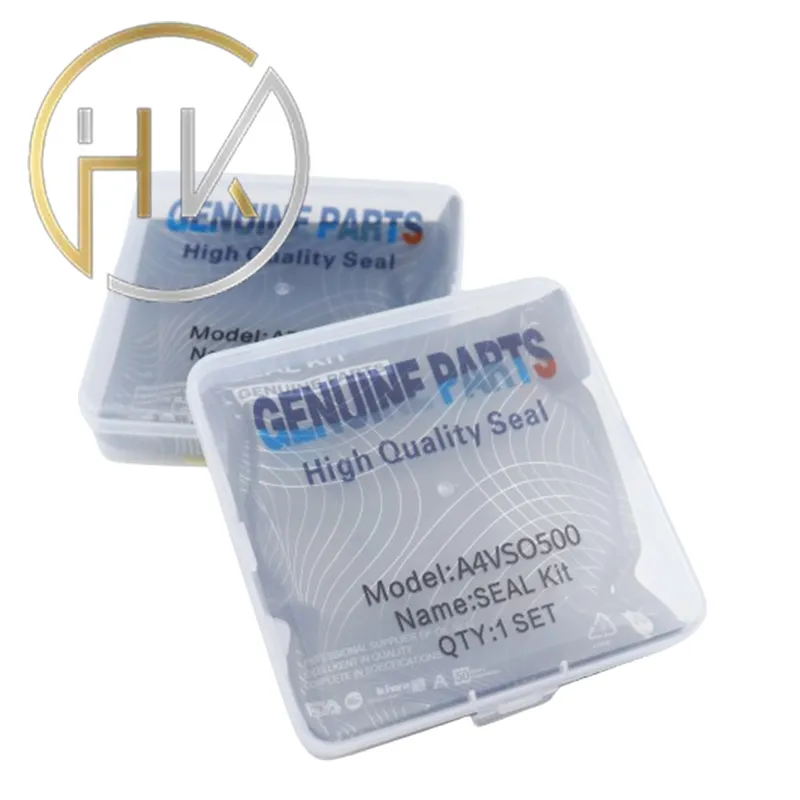
Authoritative knowledge in the field also includes understanding the different types of oil seals available.
This often includes radial lip seals, which are most common in preventing oil leakage at rotating shafts. They are designed with a flexible lip that seals dynamically and statically – this versatility makes them highly sought after in many industries, including automotive and manufacturing.
One of the critical aspects of trustworthiness in utilizing oil seal kits lies in their installation process. Proper installation cannot be overstated; it is often where failures occur that lead to costly downtimes. Misalignments or incorrect sizing during installation can negate all design intentions, leading to leaks and mechanical failures. This is why my advice always emphasizes following manufacturer guidelines carefully and using proper installation tools.
oil seal kit
Moreover, maintenance and regular inspection of oil seals can further ensure longevity and reliability. Regular checks can help identify signs of wear or damage, such as hardening, cracking, or swelling, which are critical indicators that a replacement is necessary. Being proactive rather than reactive when it comes to seal maintenance can save significant costs and prevent unexpected machinery stoppages.
Another important subject in my field relates to advancements in oil seal technology. Over recent years, innovations have focused on enhancing the durability and adaptability of oil seals. For instance, developments in material science are continuously improving the resistance of seals to extreme conditions, expanding their applications in more challenging environments. As a professional, staying updated with these advancements is crucial for providing the best recommendations to clients.
Trustworthiness in the context of oil seal kits also involves sourcing them from reputable manufacturers. Quality assurance in manufacturing, adherence to international standards, and positive customer feedback are critical indicators of a reliable product. Investing in certified oil seal kits equates to investing in long-term performance and safety.
Finally, sharing knowledge based on real-world experiences is fundamental in refining the understanding of oil seal kits. My advice is grounded in a balance between theoretical understanding and practical application, ensuring that clients appreciate not just the 'what', but the 'why' behind each choice. For businesses, optimized machinery function directly translates into tangible productivity gains, thus underscoring the critical role of selecting and maintaining the right oil seal kits.
In summary, oil seal kits, though small in size, play an indispensable role in machinery efficiency and longevity. Their correct selection, installation, and maintenance are vital for preventing leaks and ensuring optimal performance. By leveraging both expertise and advancements in seal technology, businesses can achieve significant improvements in their mechanical systems' reliability and effectiveness. Through informed decisions and adherence to best practices, oil seal kits remain a cornerstone of efficient and sustainable mechanical operation.