Navigating the intricacies of machinery maintenance, particularly when it comes to enhancing the longevity and efficiency of hydraulic systems, demands a keen understanding of oil seal kits. These integral components are designed not just for preventing leakages but significantly contribute to the smooth functioning of mechanical systems. This guide delves into the pivotal aspects of oil seal kits, equipping you with knowledge that is both profound and actionable.
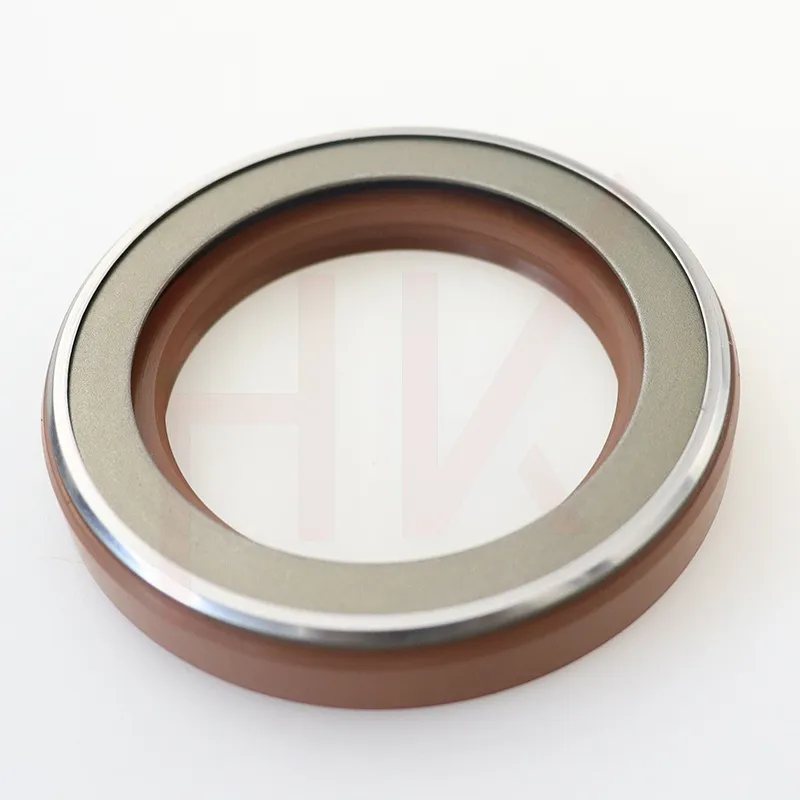
Understanding Oil Seal Kits The Basics
Oil seal kits are comprehensive assemblies utilized in various mechanical systems to contain lubricants, thereby preventing leakage and contamination. Their primary role is to maintain an effective seal between stationary and moving components within an assembly. By ensuring that lubricants like oil remain within certain structures, they also prevent harmful contaminants from penetrating the machinery, which could lead to deterioration and performance inefficiency.
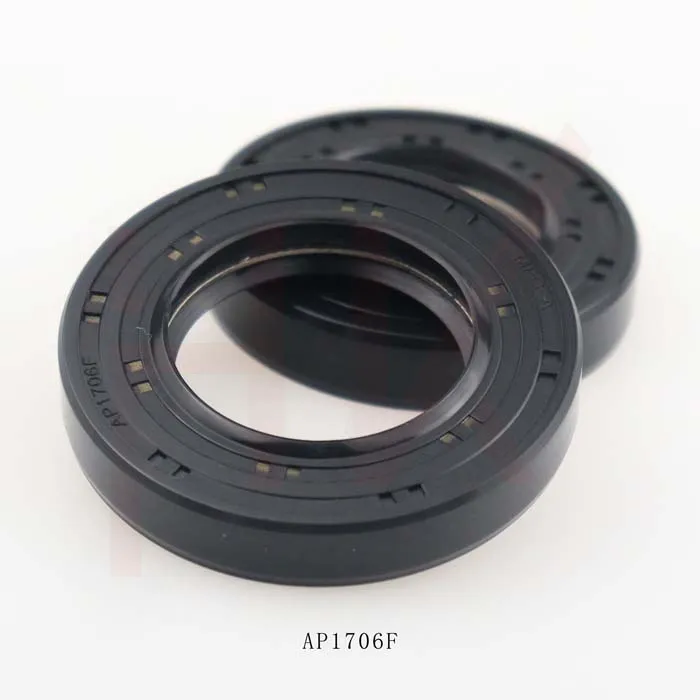
Key Components and Material Composition
A typical oil seal kit comprises a variety of components including the outer casing, the sealing element, and the spring. Each plays an integral role
- The outer casing, generally made from metals such as stainless steel or aluminum, provides structural integrity and ensures a secure fit within the housing.
- The sealing element, often crafted from robust materials such as nitrile rubber, silicone, or Viton, offers excellent resistance to temperature variations and chemical reactions.
- Springs, typically composed of high-tensile materials, support the sealing element by applying consistent pressure, ensuring that a tight seal is maintained even under arduous conditions.
Applications Across Industries
Oil seal kits find applications in numerous industries, from automotive and aerospace to manufacturing and heavy machinery. Their versatility is a testament to their design, with each kit being tailored to meet specific operational requirements. In the automotive industry, for instance, they are crucial in ensuring the efficiency of engines by keeping lubrication systems intact. Similarly, in manufacturing, oil seals are indispensable in protecting hydraulic systems from contaminants, which could lead to costly downtime.
oil seal kit
Selecting the Right Oil Seal Kit
Choosing the correct oil seal kit necessitates a clear understanding of the operational environment it will be subjected to. Factors to consider include the temperature range, chemical exposure, and the type of lubricant being used. Durability and compatibility are key, and making an informed decision can mean the difference between optimal performance and frequent maintenance issues. Consulting specifications provided by manufacturers and aligning them with your systems’ requirements is an essential step in this selection process.
Installation and Maintenance Best Practices
The installation of oil seal kits must be performed with precision to avoid potential damage or misalignment, which could compromise their functionality. Cleanliness is paramount; any dust or debris on the sealing surfaces can lead to premature failure. Adopting a systematic approach during installation, such as using the correct tools and inspecting components for wear, greatly enhances the longevity of the oil seal kit.
Ongoing maintenance should never be neglected. Regular inspections for signs of wear and tear, including checking the flexibility of the sealing element and ensuring the casing isn’t corroded, are essential. By incorporating preventive maintenance into your routine, you safeguard against unscheduled downtimes and extend the lifespan of your machinery.
Conclusion The Importance of Expertise and Trust
The role of oil seal kits in enhancing machinery reliability cannot be overstated. As a professional or enthusiast keen on maximizing the efficiency of your systems, understanding the intricacies of these components is vital. Sourcing these kits from reputable suppliers not only ensures you receive high-quality products but also guarantees access to expert advice, reinforcing the trustworthiness of your maintenance practices. By valuing expertise and prioritizing quality, you align your operations with time-tested standards, fostering an environment of efficiency and excellence.