When discussing the critical component of an electric motor often overlooked, the oil seal plays a pivotal role. Those with experience in maintaining electric motors understand that the seemingly unassuming oil seal holds the key to motor efficiency and longevity. This article offers an authoritative look into the significance of oil seals in motors, drawing from extensive expertise and real-world applications.
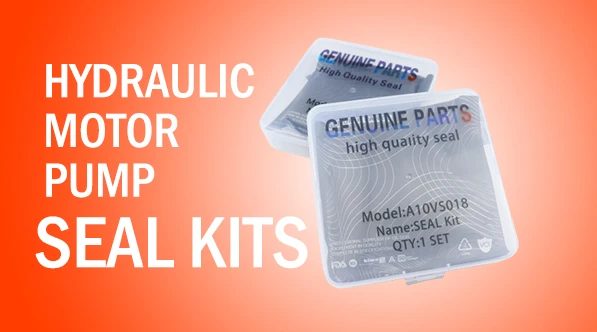
Electric motors, renowned for their robust performance, often operate in challenging environments where dust, debris, and moisture are prevalent. These elements pose a severe threat to the internal components of motors, with the bearing system being particularly vulnerable. An effective oil seal serves as the first line of defense against these environmental threats, ensuring the motor operates at peak performance.
An oil seal, also known as a rotary shaft seal, functions by surrounding the rotating shaft, forming a barrier that prevents lubricants from leaking out of the assembly. It simultaneously restricts the ingress of contaminants, which is crucial for maintaining the purity of the lubricants inside. Without a reliable oil seal, even the highest grade lubricants would quickly deteriorate, leading to increased friction, wear, and eventually, premature motor failure.
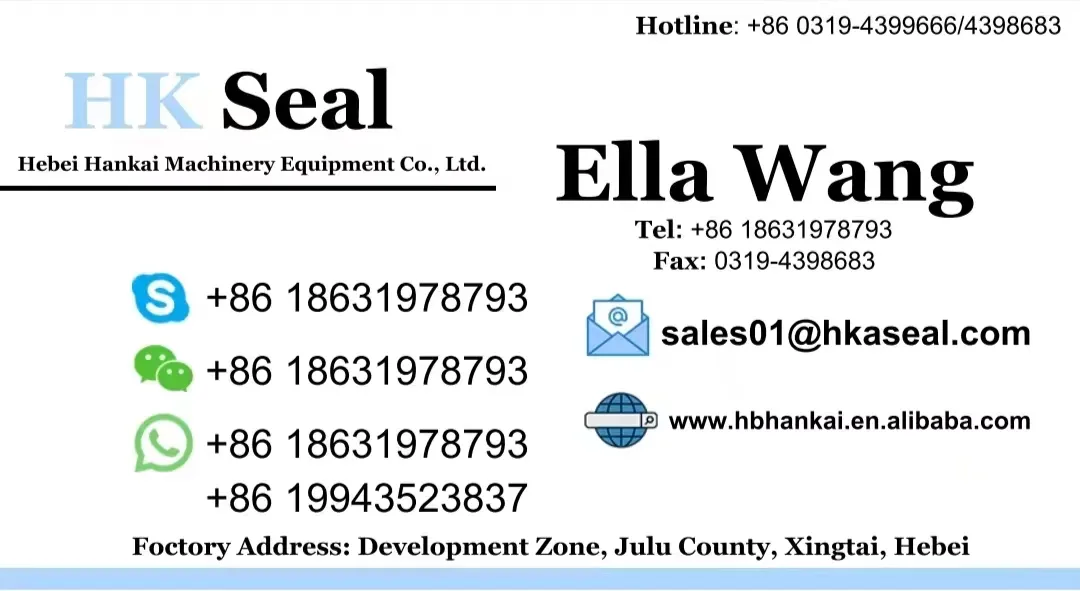
The material composition of an oil seal is critical and varies depending on the specific application of the motor. Nitrile rubber seals are frequently used due to their excellent resistance to fuels and oils, making them ideal for general-purpose motors. For applications involving high temperature or aggressive chemicals, Viton or silicone-based seals offer superior performance. Each material brings a unique set of properties, ensuring that the seal performs optimally under specified conditions.
From an expertise standpoint, selecting the correct oil seal is not a one-size-fits-all decision. It necessitates an understanding of the motor's operating environment, including temperature ranges, the type of lubricant used, and the nature of external contaminants. Engineers and maintenance professionals must assess these factors meticulously to choose a seal that offers the best performance, thereby prolonging the life of the motor and reducing maintenance downtime.
oil seal for motor
Trustworthiness in manufacturing oil seals is also paramount. Reputable manufacturers often subject their seals to rigorous testing protocols, simulating real-world operating conditions to ensure durability and reliability. These tests might include exposure to temperature extremes, chemical resistance trials, and endurance testing to observe the seal's performance over extended periods.
Furthermore, the installation process of oil seals demands precision and care. Improper installation can lead to seal failure, resulting in the very issues the seal was supposed to prevent. Training and expertise in installation procedures contribute significantly to the effectiveness of oil seals, underscoring the need for skilled technicians equipped with the necessary tools.
Real-world experience underscores the importance of a proactive maintenance schedule that includes regular inspection of oil seals. Early detection of wear or damage can prevent severe motor failures, saving significant costs associated with complete motor replacement or extensive repair work. Field technicians with the hands-on experience necessary to identify early signs of seal degradation are invaluable in maintaining motors' operational integrity.
In conclusion, while oil seals may seem a minor component in the grand scheme of motor mechanics, their role is indispensable. For those responsible for the upkeep of motors, the wisdom borne from experience and expertise reinforces the critical nature of selecting, installing, and maintaining high-quality oil seals. Therefore, recognizing the importance of oil seals not only extends the lifespan of motors but also safeguards against unnecessary failures, ensuring efficiency and reliability in motor operations across countless industries.