In the complex landscape of industrial machinery, the role of an oil seal factory is pivotal. These specialized factories are the backbone of various sectors, ensuring that the machinery operates smoothly, minimizes downtime, and upholds energy efficiency. An oil seal factory, with its vast expertise, plays a crucial role in the manufacturing of high-quality seals that protect machinery's internal components from contamination, maintain lubrication, and prevent fluid leakage.
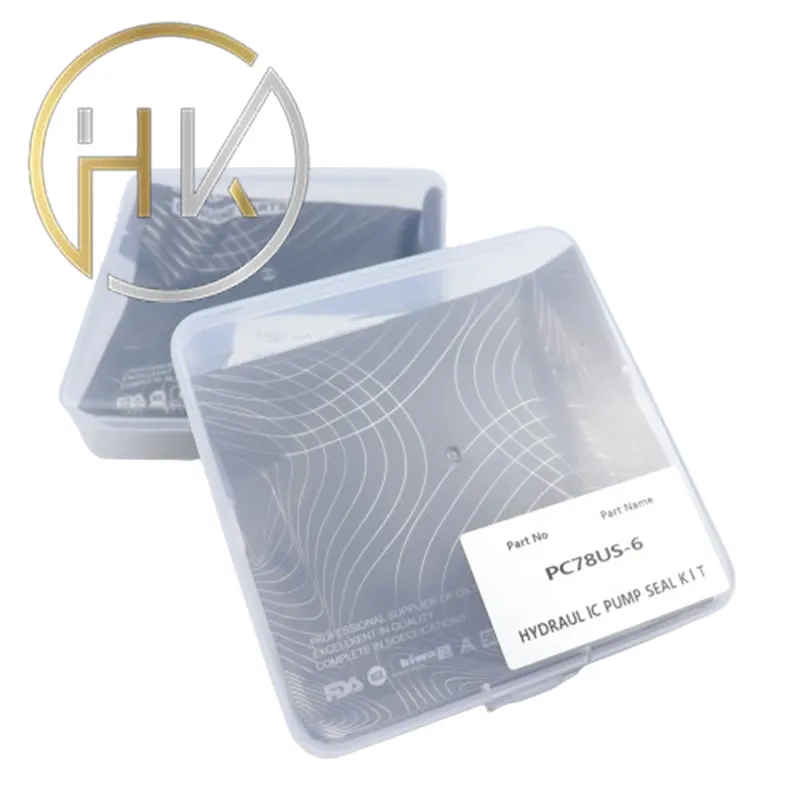
The journey of creating superior oil seals begins with meticulous material selection. A state-of-the-art oil seal factory invests heavily in research and development to determine the most suitable materials that can endure various industrial pressures and environmental conditions. This expertise extends into polymers, elastomers, and advanced composites that empower seals to perform optimally in high-temperature, high-pressure environments.
A core aspect of an oil seal factory's authority is its production process, which integrates the latest technological advancements in manufacturing. Precision molding techniques, along with CNC machining, ensure intricate designs that fit the exact specifications required by machinery across different industries, from automotive to aerospace. This precision is not merely a standard; it is a testament to the factory’s commitment to upholding the highest quality standards, a trait that resonates with their reputation across industrial sectors.
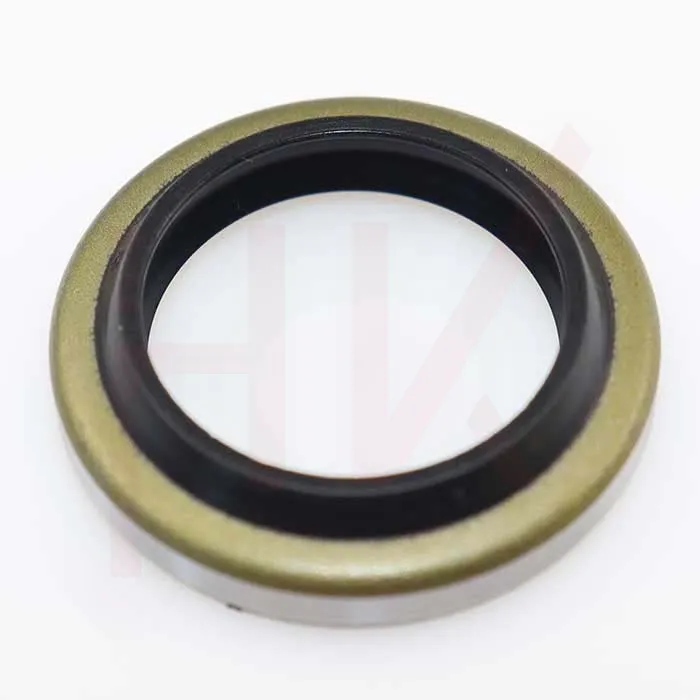
Moreover, an oil seal factory’s experience is highlighted in its rigorous quality assurance protocols. Each seal undergoes comprehensive testing, replicating extreme operational conditions to ensure reliability and durability. This rigorous testing process, overseen by seasoned engineers and technical experts, instills confidence in clients by promising dependable performance and reducing the risk of machinery breakdown. Such thoroughness contributes to the factory's credibility and trustworthiness, cultivates long-lasting partnerships, and provides clients with peace of mind.
oil seal factory
The professional expertise of an oil seal factory is not limited to manufacturing. Experienced engineers provide valuable consultation, offering solutions tailored to specific industrial needs. This consultative approach allows factories to build authoritative relationships with their clients by offering insights into improving machinery efficiency and extending lifecycle through customized sealing solutions.
An oil seal factory's trustworthiness is further exemplified through a transparent sourcing policy and sustainability initiatives. Responsible sourcing of raw materials, alongside eco-friendly practices, mirrors a commitment to environmental stewardship. Clients are increasingly conscientious about sustainability, and an advanced oil seal factory responds to this by incorporating renewable materials and minimizing ecological footprints.
Furthermore, the seamless integration of digital technologies such as AI and IoT in production lines represents the cutting-edge evolution of an oil seal factory. These technologies enhance the precision and adaptability of manufacturing processes, resulting in seals that meet the dynamic challenges of modern machinery. A factory that embraces such innovations demonstrates its foresight and adaptability, steering the industry toward the future.
In conclusion, the stature of an oil seal factory within the industrial ecosystem is bolstered by its unwavering commitment to quality, innovation, and client-centric strategies. By leveraging their vast experience, exceptional expertise, authoritative practices, and an unwavering pledge to trustworthiness, these factories not only cater to the present demands but also sculpt the future of industrial operations. Meticulously crafted oil seals are more than just components; they are pivotal in the orchestration of efficient, reliable, and sustainable industrial systems.