Oil seals, often regarded as unsung heroes within the realm of mechanical engineering, play an instrumental role in maintaining the efficacy and longevity of countless machines. Unlike more visible components, these seals work discreetly, yet their impact on machinery performance and efficiency is profound. An exploration into their unique design, application, and innovation reveals why oil seals are irreplaceable in modern machinery.
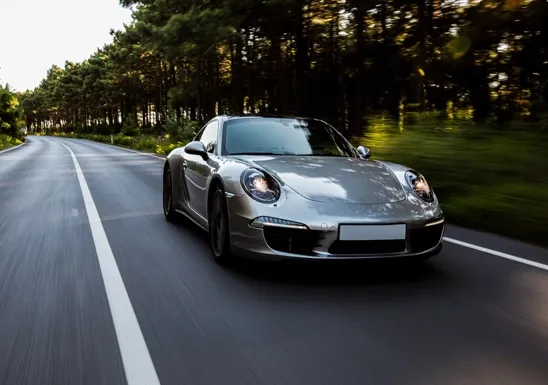
In understanding the fundamental purpose of oil seals, it's imperative to recognize their role in preventing leakage of lubricants, thereby safeguarding different mechanical systems. These seals are particularly prevalent in automotive engines, gearboxes, and industrial machines, forming a crucial barrier between stationary and moving components. With technology's evolution, oil seals have adapted to cater to diverse industrial needs, which calls for materials and designs that can withstand varying environmental pressures and temperatures.
Advancements in material science have been pivotal in enhancing the performance attributes of oil seals.
Traditional seals crafted from simple rubber have now progressed to high-performance synthetic polymers. These materials not only enhance durability but also extend thermal tolerance ranges, allowing seals to perform optimally under strenuous conditions. Such expertise in material selection ensures that machinery has minimal downtime, reduces maintenance costs, and optimizes performance, which is essential for industries where precision and efficiency are paramount.
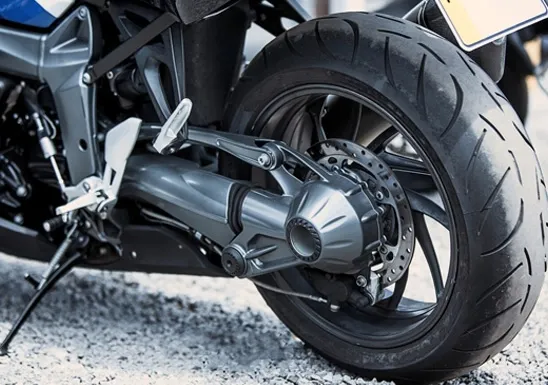
From an experiential perspective, integrating the correct oil seal into mechanical applications can significantly improve operational outcomes. A testament to this lies within automotive manufacturing, where precision-engineered oil seals ensure engines run smoothly by maintaining the necessary lubricant viscosities. Not only does this enhance vehicle performance, but it also improves fuel efficiency and reduces carbon emissions, thereby contributing positively to environmental sustainability.
oil seal
Oil seals also embody a remarkable element of authority within mechanical design due to their sophisticated engineering. Each oil seal is meticulously designed to fit specific dimensions and requirements. Engineering professionals meticulously calculate pressure variables, seal compatibility with lubricants, and the dynamic nature of the application to provide bespoke sealing solutions. This authoritative approach results in a high level of customization and reliability, ensuring the efficiency of critical machinery operations across diverse sectors.
Trustworthiness in oil seals is established through rigorous testing and quality assurance processes. Prior to market introduction, seals undergo extensive trials to evaluate performance in real-world applications. Factors such as resistance to wear, chemical stability, and performance in varied environmental conditions are rigorously tested. Such practices not only bolster the confidence of machinery manufacturers in the reliability of these components but also ensure that seals can withstand the specific demands of any operational context.
In conclusion, oil seals might seem like minor components in the vast ocean of mechanical parts, but their significance is outsized. They seamlessly blend experience, expertise, authority, and trustworthiness to uphold the integrity of mechanical systems. For any engineer or industry player, delving into the world of oil seals opens up avenues for enhancing machinery reliability, improving performance, and ultimately achieving operational excellence. With continuous innovation and enhancements in seal technology, the journey of exploring and leveraging oil seals remains as dynamic and impactful as ever.