When considering the efficiency and longevity of machinery, the oil seal emerges as a pivotal component often underestimated by novices but revered by experts. Experience in machinery maintenance vividly underscores the critical role oil seals play in safeguarding equipment integrity. Real-life scenarios repeatedly demonstrate that a high-quality oil seal not only ensures smooth operation but significantly reduces long-term maintenance costs.
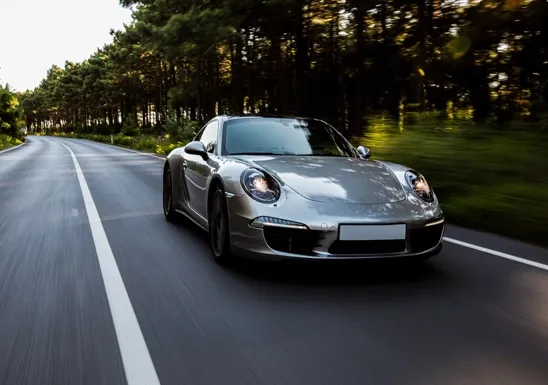
The essence of an oil seal lies in its ability to prevent lubricant leakage, a task seemingly simple yet fraught with complexity upon closer inspection.
An expert's foray into the subject reveals the nuanced engineering behind these seals. Crafted from advanced elastomers or metal, each seal is designed with precision to withstand extreme temperatures and pressures, protecting the moving parts within any mechanical system. The selection of the appropriate oil seal material, therefore, cannot be overstated as it directly influences heat resistance and friction levels—known variables that impact machinery performance.
Authoritative insights into oil seal technology disclose the innovation driving contemporary designs, such as dual lip structures and spring reinforcement, which enhance sealing efficacy. Such innovations have redefined operational limits, consistently pushing the boundaries of what mechanical systems can achieve. Industry leaders often verify these designs, reinforcing their reliability through rigorous testing and compliance with international standards.
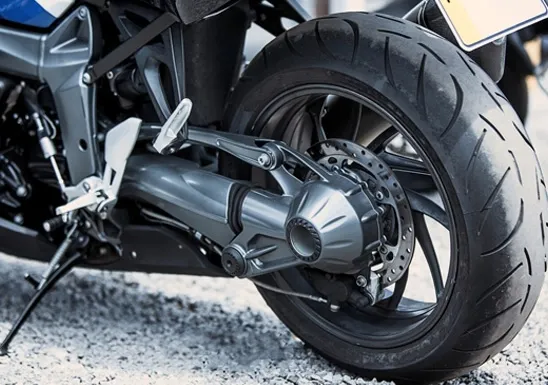
Trustworthiness of oil seal manufacturers becomes indispensable when sourcing seals for critical applications. An informed purchase relies not only on specifications but also on an evaluation of the manufacturer's reputation, peer reviews, and case studies. Manufacturers who uphold transparency about their testing processes and certification ratings build credibility, fostering trust with their clientele. A company's commitment to quality assurance programs often reflects in the durability and reliability of their oil seals.
oil seal
In industrial sectors where downtime equates to financial loss, choosing the right oil seal is a decision intertwined with strategic foresight. Industrial professionals typically advocate for regular maintenance checks to monitor seal wear and anticipate replacements before a failure occurs. Adopting a proactive maintenance approach, supported by the expertise of seasoned industrial engineers, optimizes machinery lifespan and operational efficiency.
Moreover, understanding the integral role of oil seals in energy conservation is crucial. Effective seals minimize friction, facilitating smoother operation, which in turn optimizes energy consumption within machines. This economic and environmentally positive aspect of oil seal application cannot be overlooked in the sustainable operations narrative.
As machinery evolves, so too does the methodology surrounding oil seal application. Emerging trends focus on integrating smart technologies, enabling real-time monitoring of seal conditions. This innovative leap empowers operators to preemptively address potential issues, thereby averting the cascading failures that often result from seal impairment.
In conclusion, the oil seal, an often-overlooked element, remains a linchpin in the operational success and longevity of machinery. The integration of superior engineering, rigorous testing protocols, and forward-thinking maintenance strategies underscores its indispensable value. Investing in credible sources and embracing technological advancements ensures that oil seals continue to serve as the unsung heroes in the diverse world of mechanical operations.