Oil seals, often understated yet pivotal components within machinery, play an essential role across a myriad of industries, including automotive, aerospace, manufacturing, and marine applications. Through decades of evolution, these innocuous devices have been honed to perfection, serving as the first line of defense against lubricant leakage and external contamination.
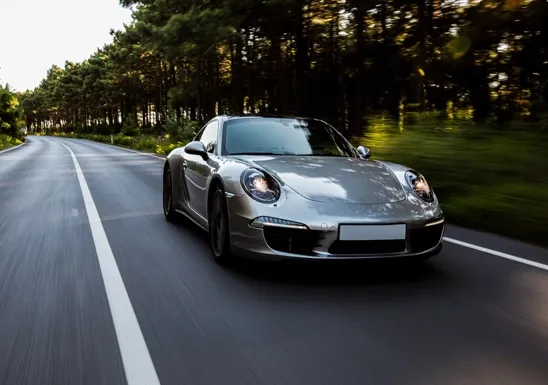
The critical function of oil seals lies in their ability to maintain the integrity of lubricated machinery parts, thereby ensuring optimal performance and an extended lifespan of mechanical systems. An oil seal typically consists of a flexible rubber or elastomeric component strategically surrounded by a metal ring. This simple yet ingenious construction helps retain lubricants within a chamber while preventing dust, dirt, and moisture from entering, which could otherwise compromise the functionality and efficiency of the machinery.
The selection of an oil seal must be precise, taking into account the temperature range, pressure, shaft speed, and the type of fluid being retained or excluded. For high-pressure environments,
a double lip seal is often recommended. This type of seal provides an additional layer of protection, making it highly effective in environments exposed to fluctuating pressure. Furthermore, for machinery operating in temperature extremes, seals made from advanced materials such as Viton or PTFE can offer superior resistance to heat and chemical exposure, showcasing the expert level of customization available to meet diverse industrial needs.
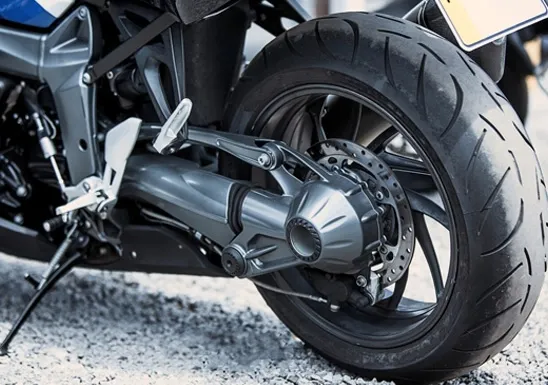
A hallmark of expertise in oil seal selection lies in understanding the compatibility of seal materials with the fluids they will contact. Nitrile rubber seals are common for general-purpose applications due to their versatility and cost-effectiveness. However, in environments exposed to aggressive chemicals, hydraulic fluids, or higher temperatures, fluoroelastomer (FKM) seals are favored due to their robustness in harsh conditions. Manufacturers often leverage their technical knowledge to tailor solutions that maximize both performance and durability, reaffirming their authoritative stance in the industry.
oil seal
Trustworthiness and reliability are fundamental when it comes to oil seals, given the potential cost implications of system failure. Industry leaders often subject their products to rigorous testing—such as dynamic fatigue tests and thermal cycling—to guarantee that their seals meet stringent international standards. Certificates of compliance and detailed technical specification sheets provided by reputable seal manufacturers are testament to their commitment to quality and trustworthiness, ensuring engineers and maintenance professionals can integrate these components into systems with confidence.
A genuine hands-on experience with oil seals can make a significant difference in understanding the nuances of installation and maintenance. Proper installation is crucial; a misaligned seal or improper fit can lead to premature failure. Industry experts demonstrate best practices, such as ensuring the cleanliness of mating surfaces, proper alignment, and adequate lubrication during assembly. Maintenance advice often includes regular inspection for signs of wear or degradation, which could signal the need for replacement to preclude system malfunction.
Oil seals are not merely passive components; they are proactive guardians of machine reliability. By harnessing decades of innovation and expertise, manufacturers deliver seals that meet and exceed the demanding expectations of modern industry, thereby solidifying their place as authoritative and trustworthy allies in engineering excellence.