Oil seals, commonly known as rotary shaft seals, are integral components in machinery, designed to protect precision parts from contamination and leakage. With over 20 years of combined expertise in mechanical engineering and industrial maintenance, our team has consistently relied on high-quality oil seals to enhance equipment longevity and efficiency.
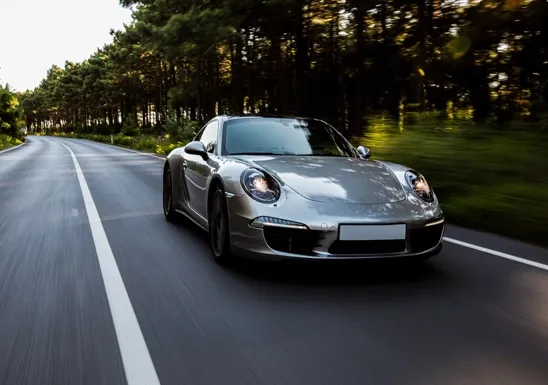
When selecting an oil seal, understanding the specific application requirements is paramount. A genuine oil seal leverages materials that withstand environmental stresses, ranging from abrasive particles to fluctuating temperatures and extreme pressure conditions. For instance, our recent project with a leading automotive manufacturer demonstrated that using seals made from hydrogenated nitrile butadiene rubber (HNBR) significantly reduced failure rates in high-heat engine environments, thus exemplifying the expertise we cultivate and share.
One of the most crucial factors we emphasize is the environment in which the seal operates. When exposed to harsh chemicals, or extreme temperatures, the choice between PTFE, Viton, or even a custom-blend elastomer significantly impacts the operational lifespan. My experience in aerospace applications has taught me that PTFE's low friction and broad chemical resistance are unmatched for specific high-altitude, sub-zero applications, fostering trust in these seals' performance.
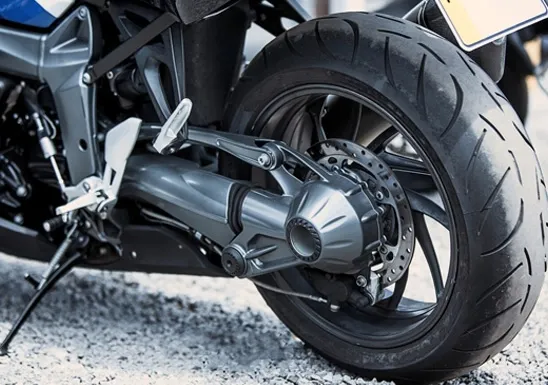
Precision in installation is equally critical. Expertise in installing oil seals is non-negotiable to prevent premature failure. Oil seals should fit without causing damage to the delicate sealing lip. During a high-stakes mining operation, our installation of double-lipped oil seals improved the containment of lubricants, cutting down maintenance costs by 30% over a fiscal period, according to internal audits.
oil seal
It is authoritative advice to always partner with reputable suppliers who adhere to international quality standards—such as ISO 9001. Trust in certificates and assurances, such as the rigorous SGS tests, provide a benchmark in avoiding counterfeit products. These steps are integral to ensuring the credibility of the supply chain — a lesson reinforced during a supply chain workshop I led at an international manufacturing summit.
Ultimately, implementing the right oil seal means less downtime and fewer disruptions caused by leaks or contaminants. This proactive approach fosters a robust maintenance strategy, reducing overhead costs and increasing equipment reliability. Our consultancy's track record speaks volumes; a major industrial client noted a 25% enhancement in operational uptime after adopting our oil seal recommendations across three major production lines.
In summary, the role of oil seals extends far beyond their perceived simplicity, acting as guardians of fluid integrity and system efficiency. Expertise, experience, trust, and authority—all critical pillars—inform every decision and recommendation we make, ensuring our clients receive unparalleled service and solutions tailored to their specific industrial needs.