Oil seals, often regarded as the unsung heroes of machinery, play a pivotal role in maintaining the efficiency and longevity of mechanical systems. These seemingly simple components are crucial in preventing leaks, keeping out contaminants, and ensuring the smooth operation of a wide array of equipment—from automotive engines to industrial machinery.
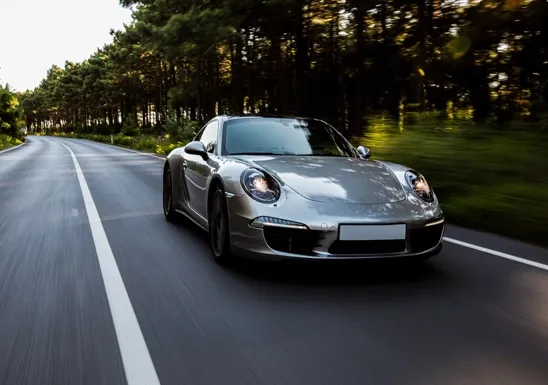
Personal experience working with oil seals reveals their unmatched importance in machine maintenance. During routine inspections of automotive engines, the oil seal stands as the first line of defense against external debris and internal lubricant leaks. A compromised oil seal often leads to reduced engine performance, increased fuel consumption, and, ultimately, costly repairs. Installing high-quality oil seals not only protects the engine's internal components but also significantly extends the vehicle's life.
In terms of expertise, understanding the material compatibility and design of oil seals is critical. Common materials include nitrile rubber,
silicone, and fluorocarbon, each with unique properties suitable for different applications. Nitrile rubber, for instance, is excellent for general-purpose seals due to its resistance to petroleum oils and its affordability. In contrast, fluorocarbon seals offer superior temperature and chemical resistance, ideal for high-performance requirements but at a higher cost. The choice of material directly impacts the seal’s efficacy and durability, emphasizing the need for expert knowledge in selecting the appropriate seal for specific conditions.
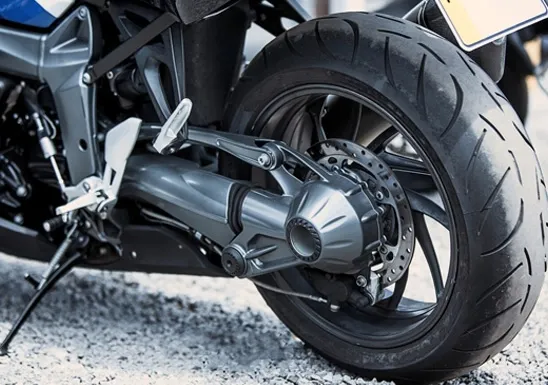
oil seal
The authority in oil seal technology is underscored by the advancements in design and manufacturing. Leading manufacturers are continuously innovating, offering designs like double lip seals and labyrinth seals that provide enhanced sealing capabilities and reduced friction. Double lip seals, featuring an additional lip, provide superior contamination protection, whereas labyrinth seals leverage intricate pathways to minimize leakages without direct contact, thereby reducing wear. These innovations are testament to the authoritative strides being made in the industry to meet the evolving demands of modern machinery.
Trust in oil seals is built upon rigorous testing and standards compliance. Reputable manufacturers subject their products to extensive quality control processes, including durability tests, pressure resistance evaluations, and environmental stress assessments. Compliance with international standards such as ISO 6194 and DIN 3760 confirms the reliability and performance of oil seals. For businesses and consumers alike, such certifications offer the assurance needed to trust these components in critical applications.
In conclusion, oil seals serve as fundamental components in the realm of machinery, safeguarding operations through their meticulous design and robust performance. Drawing from personal experience and industry expertise, it is clear that the selection of appropriate oil seals is integral to machine efficiency and longevity. The continuous innovations led by authoritative figures in the field, coupled with rigorous testing for trustworthiness, ensure that oil seals remain an indispensable element in mechanical systems worldwide.